Exploring the Viability of 3D Printing with Silicone
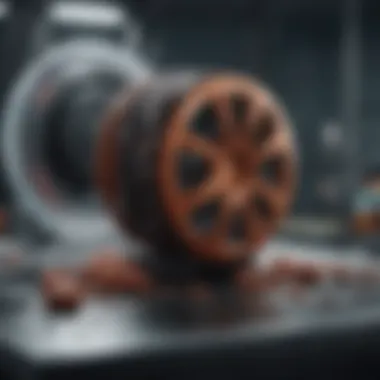
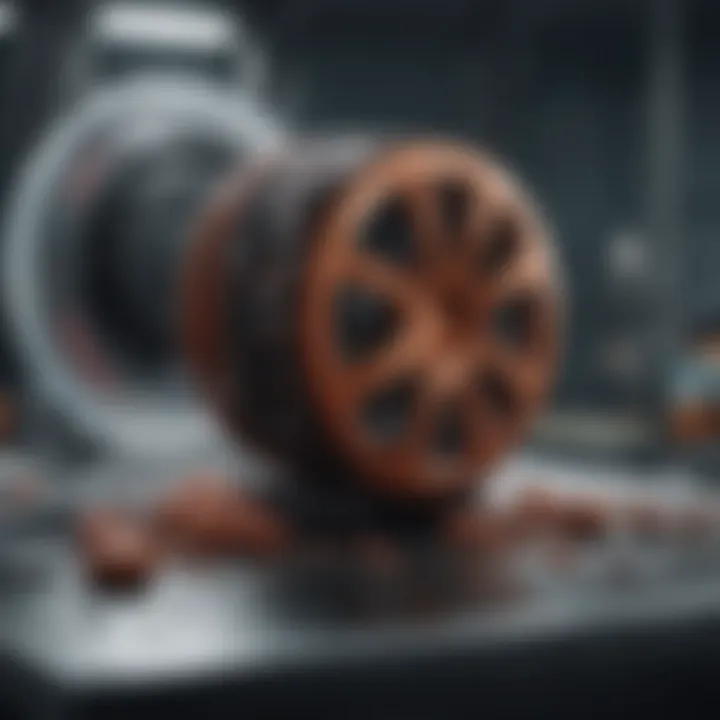
Intro
3D printing technology has revolutionized manufacturing in recent years. Among various materials, silicone stands out due to its unique properties. Understanding the viability of 3D printing with silicone is crucial. This exploration involves recognizing advancements, challenges, and varied applications.
In various industries, silicone is valued for its flexibility, biocompatibility, and durability. The potential for 3D printing with silicone offers exciting prospects for custom solutions. However, it also requires in-depth analysis of the material's properties and compatibility with existing technologies.
The significance of this topic resonates throughout a wide array of fields. From healthcare to automotive design, the implications of successful silicone 3D printing extend beyond simple production. They may enable innovative designs which were previously unachievable. Hence, delving into this subject sheds light on the promising future of additive manufacturing with silicone materials.
Research Highlights
Key Findings
Research into 3D printing with silicone has revealed substantial findings:
- Material Flexibility: Silicone exhibits exceptional flexibility, often exceeding that of other materials. This is vital for applications demanding movement and shape adaptability.
- Biocompatibility: The inert nature of silicone makes it ideal for medical applications, such as prosthetics or implants.
- Surface Finish: The finish quality attained through 3D printing with silicone can meet or exceed traditional manufacturing methods, yielding aesthetically pleasing results.
- Customization: 3D printing allows for unprecedented levels of customization and personalization in product design.
Implications and Applications
The implications of 3D printing with silicone stretch across various industries:
- Healthcare: Customized prosthetics and implants tailored to patient-specific anatomy.
- Automotive: Lightweight components that maintain durability and performance.
- Consumer Products: Unique designs for everyday items, such as kitchenware or wearable tech.
Methodology Overview
Research Design
The methodology comprises both experimental and theoretical approaches. It aims to comprehensively assess the 3D printing processes involved with silicone. Researchers focused on understanding material behaviors when subjected to different printing technologies.
Experimental Procedures
- Material Selection: Various silicone formulations were tested to evaluate their compatibility with specific 3D printing technologies.
- Printing Process: Different 3D printers, such as Stratasys and Formlabs, were utilized to assess variations in output quality and precision.
- Performance Testing: Samples were subjected to tensile strength, flexibility, and durability tests to generate comparative data against traditional methods.
This in-depth investigation highlights not only the promising future for 3D printed silicone but also the implications of ongoing research efforts that aim to refine techniques further.
Preamble to 3D Printing with Silicone
The focus on 3D printing with silicone offers insights into a sophisticated and evolving segment of manufacturing technology. This article seeks to unravel the multifaceted aspects of this innovative process. It is critical because silicone presents unique qualities unlike other commonly used materials in 3D printing. Its flexibility, durability, and biocompatibility make it suitable for varied applications, particularly in healthcare and consumer products.
3D printing with silicone represents a shift in how we visualize and create objects. Unlike traditional methods that often involve the use of rigid plastics or metals, silicone allows for greater adaptability in design. Understanding silicone's role in 3D printing can highlight its benefits and the challenges it introduces, such as specific printing technologies and post-processing requirements.
Historical Context of 3D Printing
The journey of 3D printing began in the early 1980s. The concept transformed from theoretical discussions into practical applications. Initially, 3D printing primarily focused on plastics, particularly with the advent of stereolithography. However, the evolution of materials and technology soon expanded the possibilities significantly. Over the years, advancements have allowed for a broader array of materials, including metals, ceramics, and now, silicone.
As manufacturing processes have evolved, so too have the techniques employed in 3D printing. The rise of silicone as a prominent material has been tightly linked to advancements in both printing technology and material science. Researchers continuously seek ways to enhance the capabilities of silicone for different applications, marking a pivotal shift in the industry.
The Rise of Silicone in Manufacturing
Silicone's emergence in manufacturing is rooted in its impressive properties. Known for its thermal stability, silicone can withstand extreme temperatures. This quality makes it ideal for various industries, including automotive and consumer electronics. Furthermore, silicone offers excellent flexibility and elasticity, which is beneficial in applications that require intricate designs.
Over time, industries have acknowledged silicone’s advantages as they seek materials that can meet modern demands. The healthcare sector, in particular, has shown a growing interest in silicone due to its biocompatibility. This trait ensures that silicone products can safely come into contact with human tissues, making it a favored material for medical devices and prosthetics.
In summary, the combination of silicone's physical properties and its application potential drives its growing adoption in 3D printing. This appeal can be seen as a reflection of changing industry needs and technological capabilities.
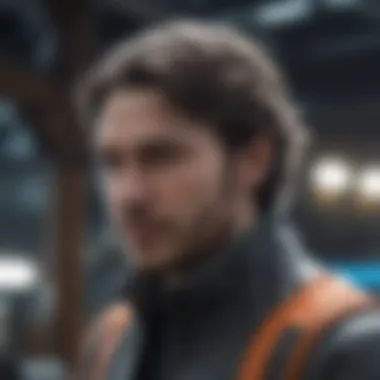
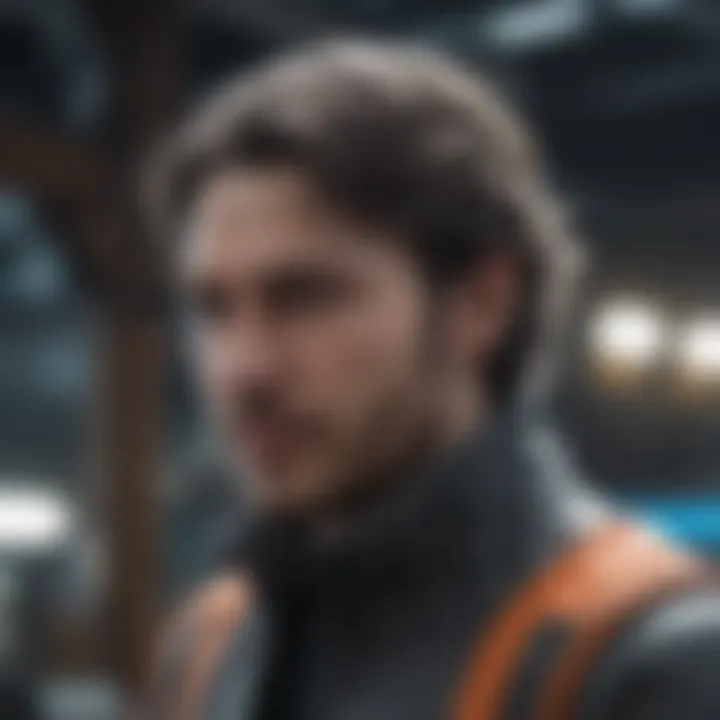
Understanding Silicone Materials
Understanding silicone materials is critical for grasping the potential of 3D printing with these substances. Silicone is a unique material that varies significantly from traditional plastics and other polymers typically utilized in printing. Comprehending the chemical composition, properties, and advantages of silicone leads to better innovation in using it for 3D printing applications.
The flexibility, heat resistance, and biocompatibility of silicone make it particularly suitable for diverse industries. These characteristics ensure its reliability and longevity in practical applications. Thus, exploring silicone materials is not just about material science; it also encompasses engineering principles, production considerations, and user needs, making it essential for informed decision-making in the field of 3D printing.
Chemical Composition of Silicone
Silicone is a synthetic polymer made from silicon, oxygen, carbon, and hydrogen. Its basic structure involves a repeating unit of siloxane, which is a chain of alternating silicon and oxygen atoms. The presence of organic groups attached to the silicon atom, such as methyl or phenyl groups, plays a vital role in determining the properties of the silicone.
This chemical structure contributes to the material’s unique characteristics, making it suitable for 3D printing. More specifically, the presence of silicon allows for a high degree of flexibility and durability. This stability in structure under a range of environmental conditions gives silicone a significant advantage in various applications.
Properties of Silicone
The properties of silicone are diverse and significantly influence its usability in 3D printing. Understanding these properties helps stakeholders make informed choices when adopting silicone materials in manufacturing processes.
Flexibility and Elasticity
Flexibility and elasticity are key features of silicone. The material can effortlessly return to its original shape after deformation, a quality highly valued in numerous applications. This flexibility allows for intricate designs and fluid movements in printed products.
Advantage: The capacity to withstand bending and stretching without damage makes silicone ideal for products like seals and gaskets in automotive applications. Its elasticity reduces the risk of breakage during handling and usage, thus enhancing durability. The inherent design capabilities also mean that manufacturers can create complex shapes with ease, improving product functionality.
Temperature Resistance
Temperature resistance is another significant property of silicone. It maintains its integrity across a wide temperature spectrum, often from -60 °C to +200 °C. This resilience is crucial when applications require exposure to extreme heat or cold.
Advantage: The ability to withstand high temperatures makes silicone suitable for components in automotive and aerospace industries where these extremes are commonplace. Moreover, this characteristic reduces failure rates and increases reliability in systems that overlap with thermal management applications.
Biocompatibility
Biocompatibility is an essential aspect when silicone is utilized in medical applications. Silicone exhibits excellent compatibility with biological tissues, making it suitable for various medical devices like implants and prosthetics.
Advantage: Its biocompatibility ensures that silicone products do not provoke adverse reactions in the body. This property supports long-term usability within medical contexts, providing additional safety to patients.
The unique array of properties of silicone positions it as a prime candidate in the evolving landscape of 3D printing, marking its significance in several innovative applications.
In summation, understanding silicone materials, from their chemical composition to their critical properties, is vital in harnessing their full potential within the realm of 3D printing. The careful consideration of these factors impacts production efficiency and product performance, ultimately driving advancements across multiple sectors.
3D Printing Technologies Compatible with Silicone
The evolution of 3D printing technologies has opened the door to new possibilities in manufacturing. Among these, the integration of silicone as a material offers unique advantages. Various printing techniques adapt to silicone, each presenting distinct benefits and challenges. Understanding these technologies is crucial in maximizing the potential of silicone in diverse applications.
Selective Laser Sintering (SLS)
Selective Laser Sintering is a powder-based 3D printing technique. It uses a laser to fuse small particles of plastic, metal, or ceramic into a solid structure. With silicone, SLS allows for complex geometries that others methods may not support. The process involves layering powder, which is selectively sintered by a laser.
A key advantage here is the ability to create highly detailed and intricate designs. However, one must also consider the cost and setup of SLS machines. Their operation may require more intensive training compared to simpler methods. It is also essential to ensure materials used are compatible with the specific laser parameters.
Fused Deposition Modeling (FDM)
Fused Deposition Modeling is a popular method known for its accessibility and ease of use. This technology extrudes thermoplastic filaments through a heated nozzle. Though not the primary method for silicone, recent advancements have enabled the use of silicone filaments.
FDM systems offer a variety of profile settings. This flexibility allows for altering the temperature and speed for optimal silicone flow. However, the silicone must be appropriately formulated to maintain print quality. Furthermore, the printed structures may require additional post-processing to enhance mechanical properties.
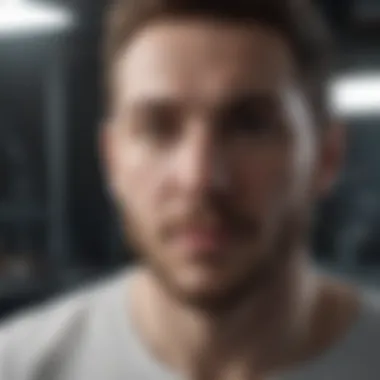
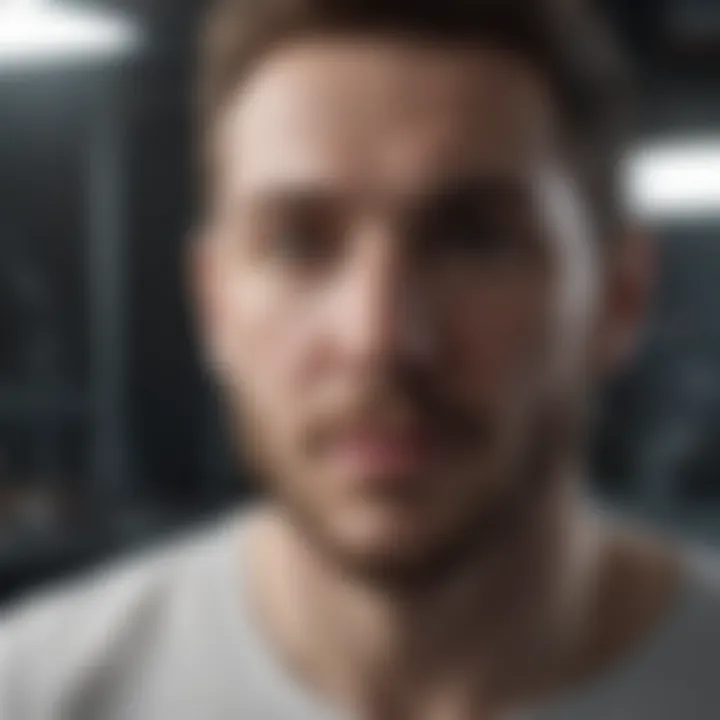
Digital Light Processing (DLP)
Digital Light Processing utilizes a digital light source to cure liquid resin layer by layer. When it comes to silicone, this method provides high resolution and smoother surface finishes. DLP is particularly useful for applications needing detailed features, like dental and medical devices.
The curing process poses some challenges. The silicone material must exhibit compatibility with the UV light source used by DLP printers. In addition, managing the viscosity of silicone is critical to ensure successful printing without excess material waste.
Direct Ink Write (DIW)
Direct Ink Write is an innovative technique perfect for various materials, including silicone. This method involves extruding a "ink" directly through a nozzle. The versatility of DIW stands out, as it allows the incorporation of multiple materials in a single print.
One of the strongest points of DIW is its ability to control the material flow precisely. This allows for complex shapes and designs, contributing to innovative product development. Nevertheless, ensuring that the silicone maintains its structure during the printing process remains a challenge. This might require additional calibration and experimentation.
The exploration of these printing technologies reveals a promising horizon for 3D printing with silicone. Each technology holds potential in various applications but also presents unique challenges. The careful selection of a suitable technology can significantly impact the outcome, performance, and efficiency of the final product.
Challenges in 3D Printing with Silicone
In the exploration of 3D printing with silicone, understanding the primary challenges is crucial. Silicone presents unique properties that make it beneficial for various applications, but these same characteristics can complicate the printing process. Identifying and overcoming these challenges can significantly affect the viability and effectiveness of silicone in 3D printing.
Viscosity and Printability Issues
Viscosity plays a pivotal role in the 3D printing process for silicone materials. Different silicone formulations exhibit varying viscosities, which can affect how they flow through the printer's nozzle. High-viscosity silicones can lead to clogging or inconsistent material deposition, making precise printing difficult.
Moreover, the printability of silicone also depends on its consistency and temperature. It is often necessary to adjust the temperature settings of the printer to manage the viscosity effectively. For instance, heating the silicone can reduce its thickness, making it easier to print. However, excessive heat could lead to degradation of material properties.
"Addressing viscosity issues is essential for achieving high-quality 3D prints using silicone materials."
Adhesion to Build Platforms
Another significant challenge in silicone 3D printing is achieving proper adhesion to build platforms. Silicone's inherent properties make it less likely to adhere to common surfaces used in 3D printing, such as glass or plastic. This factor can lead to warping or detachment during the printing process, resulting in failed prints.
Using specialized adhesives or textured surfaces can help improve adhesion. Some manufacturers have developed build plates specifically designed for silicone printing. They often feature surface treatments that enhance silicone's grip. However, optimal adhesion methods can vary depending on the specific silicone blend used.
Post-Processing Requirements
Post-processing is an integral part of the 3D printing process, especially when working with silicone. Due to the material's unique properties, certain finishing techniques become necessary. This may include methods such as cleaning, curing, or additional shaping processes. For example, many silicone prints require curing to achieve their final properties, which may involve heating or exposure to specific conditions.
Additionally, the nature of the intended application often dictates the extent of post-processing needed. In applications such as medical devices, precise surface finishes and biocompatibility are critical. Therefore, understanding and planning for these post-processing requirements is essential before starting a print job.
Applications of 3D Printed Silicone
The applications of 3D printed silicone represent a significant advancement in the flexibility and functionality of manufacturing processes across various sectors. Silicone, known for its unique properties such as elasticity and temperature resistance, is increasingly integrated into diverse applications that benefit from the customization and precision offered by 3D printing. As industries embrace more innovative production methods, understanding these applications is essential for operators, engineers, and designers.
Healthcare and Medical Devices
In the healthcare sector, 3D printed silicone has shown transformative potential. The customization capabilities allow for the creation of tailored medical devices that meet specific patient needs. For example, prosthetic devices and surgical models made of silicone can closely mimic human tissue properties. This enhances the functionality and comfort of prostheses, improving patient outcomes significantly. Furthermore, silicone's biocompatibility facilitates its use in implants and medical consumables without causing adverse reactions. This reliability is crucial in environments where safety is paramount.
Automotive Industry Innovations
The automotive industry also leverages the advantages of 3D printed silicone in developing prototypes and end-use parts. Silicone components are lightweight yet durable, making them ideal for applications such as gaskets, seals, and flexible connectors. These elements can withstand vibrations and temperature fluctuations, an essential feature in vehicles. As manufacturers aim for sustainability, reducing material waste through additive manufacturing presents a compelling case. Companies can create complex geometries that were once unfeasible with traditional methods, leading to innovations in car design and functionality.
Consumer Goods Revolution
The consumer goods sector is experiencing a revolution fueled by 3D printing with silicone. This technology allows for the rapid production of customized items such as phone cases, kitchen gadgets, and wearable technology. Products made from silicone are often more durable than those made from conventional plastics, leading to increased consumer satisfaction. The ability to produce small batches efficiently without extensive tooling means manufacturers can respond more quickly to market trends, enabling a more dynamic and responsive business model.
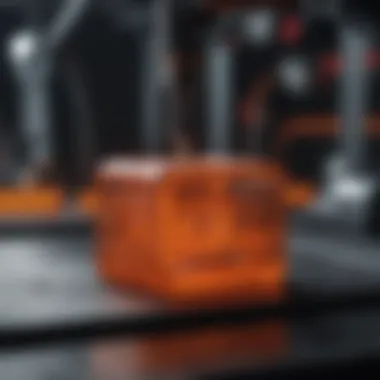
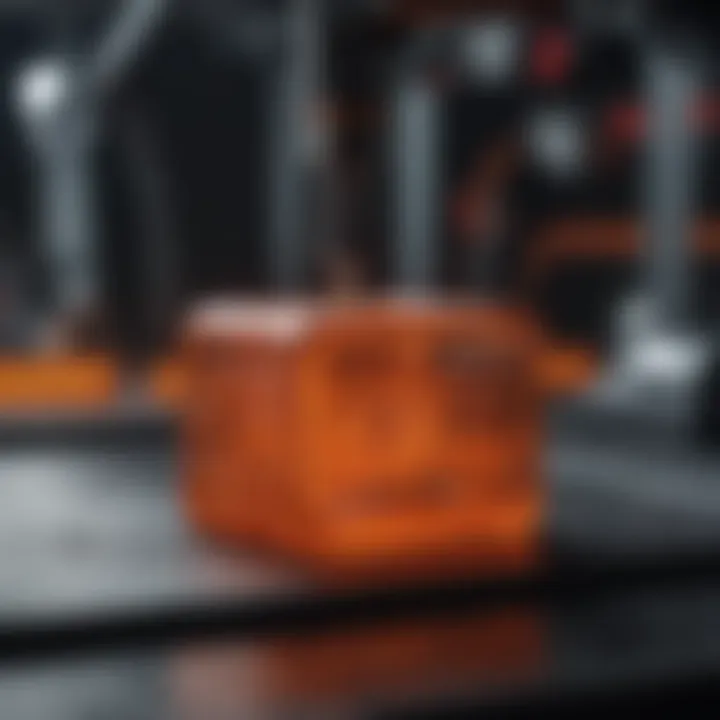
Aerospace Applications
In the aerospace field, the use of 3D printed silicone is still emerging but holds promising potential. Lightweight silicone components can enhance fuel efficiency and performance while maintaining safety standards. For example, custom seals and prototypes of various components can be rapidly produced. The scalability and adaptability required in aerospace projects benefit from the capabilities of 3D printing, facilitating innovation without compromising on quality or reliability. The shift toward more advanced materials like silicone in aerospace represents a strategic move toward improved performance in a highly competitive environment.
"3D printing with silicone is not just a trend; it is reshaping how industries approach manufacturing challenges, enabling them to innovate locally with fewer constraints."
By focusing on these applications, industries can unlock new potentials that reimagine production and design. As technologies evolve and improve, the integration of 3D printed silicone will likely expand further, offering efficiencies and benefits that traditional manufacturing processes struggle to achieve.
The Future of 3D Printing with Silicone
The future landscape of 3D printing with silicone looks promising, driven by technological advancements and an increasing understanding of the material. As industries seek flexible and reliable solutions, silicone's unique properties, like biocompatibility and thermal stability, open numerous applications.
Research continues to emerge in this field, indicating increased investment in methods that enhance the printing processes. Notably, these developments focus on improving print quality and usability. This will likely lead to a broader adoption of silicone in not only specialized fields but also everyday consumer products.
Considerations regarding the scalability of silicone printing processes are crucial. As the demand grows, manufacturers must address challenges in mass production while maintaining quality. The future will focus on optimizing both the material properties and the printed outputs, ensuring they meet rigorous industrial standards.
Emerging Research and Developments
Research in silicone 3D printing has become vibrant, with universities and corporations exploring innovative ways to leverage silicone's versatility. Scientists are looking into various formulations to improve adhesion properties which will enable better printing outcomes. New approaches in chemical engineering can lead to enhanced user experiences, making it easier to print complex geometries.
Some interesting developments include:
- Bio-based Silicones: The effort to use sustainable materials is gaining traction. Researchers are experimenting with bio-based silicone formulations, blending sustainability with performance.
- Smart Silicones: Advances are also taking place in the creation of silicone that can respond to environmental stimuli, such as heat or pressure. This could be significant for fields like healthcare or aerospace.
- Multi-material printing: Combining silicone with other materials during the printing process can create hybrid products that leverage the strengths of each component.
"Advancements in silicone 3D printing stand to change how we view manufacturing solutions, especially in areas like healthcare where precision is paramount."
Market Trends and Predictions
The market for 3D printed silicone is anticipated to grow significantly within the next few years. Reports indicate an uptick in industries, such as healthcare, automotive, and consumer goods, adopting silicone printing practices.
Key trends shaping this market include:
- Increased Customization: As consumers seek personalized products, the ability to 3D print silicone allows for unparalleled customization.
- Cost-effectiveness: Improved processes are expected to lower production costs over time, making silicone printing more accessible for small and medium enterprises.
- Cross-industry Applications: As technologies improve, silicone 3D printing will likely find its way into industries like fashion and electronics, which are currently nascent fields for this technology.
In summary, the future of 3D printing with silicone is buoyed by emerging research and favorable market conditions. Industries are beginning to see the potential of silicone’s unique qualities, thus paving the way for innovative applications and solutions. As technology advances, we can expect a significant shift in how silicone is incorporated into production.
End
The conclusion serves as a critical synthesis of the insights obtained throughout the article regarding 3D printing with silicone. This topic is significant in multiple ways. First, it highlights the unique properties of silicone materials during the printing process. Understanding these properties is essential for leveraging them effectively in industrial applications. Moreover, the challenges associated with 3D printing with silicone provide a realistic perspective. They encourage researchers and practitioners to innovate solutions that can enhance printability and application scope.
An important benefit of exploring silicone printing is its wide applicability across different sectors. From healthcare to aerospace, the versatility of silicone opens up new avenues for manufacturing processes that were not previously feasible with traditional methods. 3D printed silicone can lead to more sustainable production. This is particularly true as it has potential for reduced waste and lowered energy consumption.
Despite the evident potential, considerations must be made regarding the limitations and the learning curve that accompanies mastering silicone printing technologies. This includes factors like equipment costs and material availability.
In summary, while the challenges in 3D printing with silicone are non-negligible, the prospect of further advancements and applications suggests a promising future for this technology. As industries continue to demand innovative solutions, 3D printed silicone could emerge as a viable alternative to traditional manufacturing techniques.
Summary of Key Insights
The exploration of 3D printing with silicone reveals several key takeaways:
- Technological Advancements: Recent innovations in printing technologies have made the use of silicone more accessible.
- Material Properties: Silicone's unique characteristics, such as flexibility and heat resistance, distinguish it from other materials.
- Challenges: Issues such as viscosity and adhesion must be addressed to ensure successful printing outcomes.
- Applications: The potential for silicone in healthcare, automotive, consumer goods, and aerospace underscores its versatility.
- Future Outlook: Continued research in this field indicates ongoing improvements and broader implementation.
These insights are crucial for understanding both the current landscape and future prospects of silicone in 3D printing.
Final Thoughts on Silicone Printing Potential
In light of the findings discussed in this article, the potential of 3D printing with silicone should not be underestimated. This technology presents opportunities for innovation that can significantly impact various industries. Understanding the chemical composition and properties of silicone allows engineers and manufacturers to push boundaries in product design and functionality.
The future of 3D printing with silicone looks bright, driven by ongoing research and adaptation of new technologies. Emerging methodologies could resolve existing challenges that hinder wider adoption. While progress is apparent, stakeholders must remain aware of the evolving nature of this field.
In closing, engaging with the topic of silicone printing is not merely an academic exercise. It holds tangible implications for real-world applications. As the industry grows and matures, the ability to harness the unique benefits of silicone materials will be an essential aspect of competitive manufacturing.