Advances in Additive Friction Stir Processes
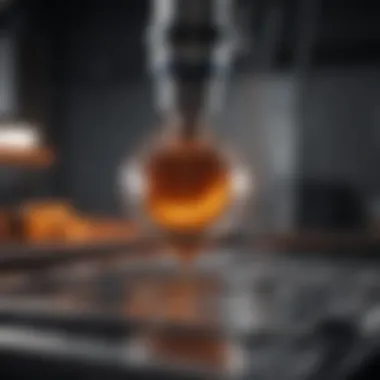
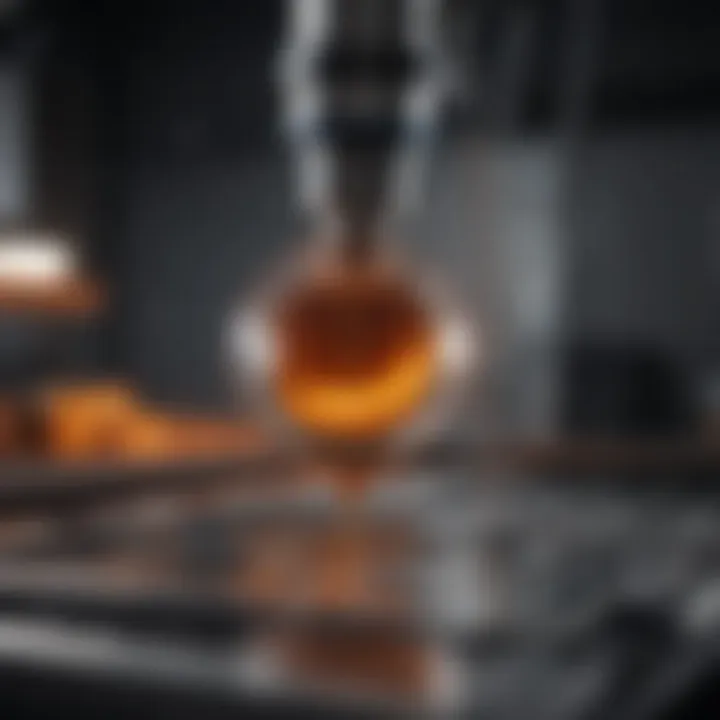
Intro
Additive friction stir processes represent a significant evolution in manufacturing technology. These processes merge the principles of friction stir welding with additive manufacturing techniques, creating an innovative approach to material fabrication. This article aims to explore the intricate mechanics, benefits, and practical applications of these processes, shedding light on their growing relevance in various industries.
Understanding the core concepts behind friction stir welding is essential. This process uses a rotating tool to generate heat through friction, allowing materials to soften and bond. The adaptation of this technique into additive manufacturing involves using similar mechanisms to allow for the addition of new material layers. Such integration increases the versatility and potential of traditional manufacturing methods.
In recent years, advancements in materials science and engineering have enhanced the effectiveness of additive friction stir processes. As industries increasingly demand better efficiency, reduced waste, and higher performance materials, it becomes crucial to investigate how these processes meet such needs.
Preface to Additive Friction Stir
Additive friction stir processes (AFSP) embody a significant evolution in manufacturing techniques that merges the principles of friction stir welding with additive manufacturing. This combination is important as it introduces innovative ways to fabricate complex geometries and enhance material properties. As industries move towards more efficient and sustainable production methods, understanding AFSP becomes crucial. The nuances of this technology can reveal new paths for research and practical applications across various fields.
Overview of Friction Stir Technology
Friction stir technology itself is pivotal in the modern manufacturing landscape. It utilizes a rotating tool to generate frictional heat and stir materials together, leading to solid-state bonding. This process minimizes defects commonly associated with traditional welding techniques, such as porosity and cracking. The absence of melting also preserves the material's intrinsic properties.
Friction stir welding has gained recognition in industries like aerospace and automotive for its ability to join materials of different grades and alloys effectively. This foundation lays the groundwork for integrating friction stir techniques into additive manufacturing, which can redefine how we think about part creation and assembly.
Intro to Additive Manufacturing
Additive manufacturing, often termed 3D printing, signifies a transformative change in how products are designed and produced. The technique builds objects layer by layer, responding to the demand for customized solutions and reducing material waste. With advancements in materials and technologies, additive manufacturing is now capable of producing components that were previously impossible or economically unfeasible.
This method allows for the creation of intricate designs that conventional subtractive methods cannot achieve. As industries explore more adaptable production methods, the synergy between additive techniques and established manufacturing processes, such as friction stir welding, becomes increasingly relevant.
The Intersection of Friction Stir and Additive Processes
The integration of friction stir technology within additive manufacturing marks a significant advancement. By combining the speed and precision of additive methods with the benefits of friction stir processing, manufacturers can enhance mechanical properties and achieve better overall functionality in final products.
This intersection enables the construction of complex parts with tailored properties. For instance, the mechanical properties of a part can be adjusted by changing the material feed during the additive process. The resulting components exhibit improved strength, ductility, and fatigue resistance, aspects critical for high-performance applications in various sectors.
Overall, the introduction of additive friction stir processes provides a robust framework for developing innovative solutions in manufacturing and engineering. As we delve further into this topic, understanding the principles, advantages, and practical applications will be essential for leveraging the full potential of AFSP in diverse industries.
Principles of Additive Friction Stir Processes
Understanding the principles behind additive friction stir processes is crucial for grasping how this technology will evolve and integrate into various applications. These principles not only highlight the mechanics of the process but also underline the benefits that accrue from its adoption in diverse industries. Key elements include the interplay between mechanical forces and thermal effects, which are central to producing high-quality welds and build-ups in distinct materials.
Mechanics of Friction Stir Welding
Friction stir welding (FSW) is a solid-state joining process. In this technique, a rotating tool generates friction and heat, locally softening the material without melting it. The mechanical action of the tool then stirs the softened material. Once the tool passes, the material cools down, resulting in a strong bond that maintains the integrity of the original material. This method is known for creating welds with minimal thermal distortion, as it avoids the melting phase typical of conventional welding methods. The specific parameters, such as tool speed, rotational torque, and feed rate, directly affect the quality of the weld. Adjusting these parameters can optimize strength and depth of penetration.
Additive Techniques in Friction Stir
The integration of additive manufacturing techniques with friction stir processes elevates the capability of traditional FSW. Instead of only joining materials, this methodology allows for the addition of material to create complex geometries layer by layer. This capability expands the applications of friction stir processes considerably, enabling the creation of new components or the repair of existing ones. In this context, additive techniques utilize material rods or wires, which are fed into the weld zone. The tool then facilitates a mixture of the new material with the substrate, enhancing the resulting builds with desired properties, like strength and corrosion resistance.
Material Interaction and Heat Generation
In additive friction stir processes, the interaction between the tool, the substrate, and the added material is fundamental. As the tool rotates and moves along the material, it generates frictional heat. This heat softens the surrounding material while also affecting the mechanical properties of both the base and the added materials. The heat distribution is a critical factor; too much heat can lead to defects such as voids or excessive grain growth, while too little may not yield sufficient bonding.
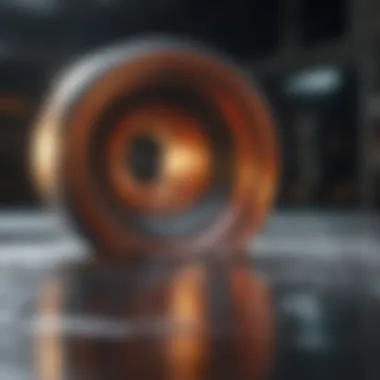
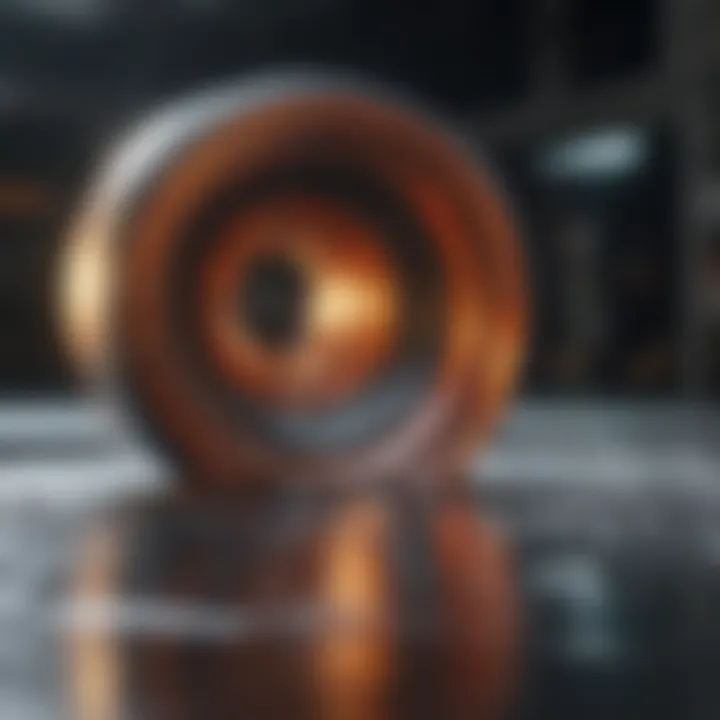
The composition and thermophysical properties of the materials also play a role. Different materials react uniquely to heat generation and mechanical stresses. Optimizing these interactions through careful selection of materials and processing parameters can significantly improve the performance of the resultant component.
Understanding these principles assists engineers and researchers in effectively applying additive friction stir processes, ultimately leading to innovations across sectors.
These principles pave the way for significant advancements and potential applications in fields like aerospace, automotive, and construction, where material performance and structural integrity are paramount.
Benefits of Additive Friction Stir Processes
The benefits of Additive Friction Stir Processes are crucial to understanding its place in modern manufacturing. This technology combines the principles of friction stir welding with additive manufacturing techniques. The outcome is significant improvements in material properties, production efficiency, and environmental considerations, leading to its growing adoption across various industries.
Enhanced Material Properties
Additive Friction Stir Processes greatly enhance material properties. When compared to traditional manufacturing methods, this technique optimizes the mechanical characteristics of materials, which results in stronger and more durable components. The process generates a refined microstructure that can withstand higher stresses. It is also effective in producing materials with better fatigue resistance.
In addition to strength, this process can facilitate the creation of materials with unique properties. For instance, it allows for the mixing of different alloys which leads to customized material profiles. This flexibility can satisfy specific requirements in high-performance applications like aerospace or automotive manufacturing. The ability to control the heat input during processing helps in achieving desired properties without compromising material integrity.
Improved Production Efficiency
Improved production efficiency is another obvious benefit. Additive Friction Stir Processes reduce material waste, which is common in subtractive manufacturing techniques. The additive nature means that materials are only used where needed. In turn, this efficiency leads to cost savings. Moreover, the processes can achieve complex geometries that might not be feasible with traditional methods. This capability shortens lead times and can result in faster production cycles.
Importantly, the scalability of the process enhances productivity. Implementing this technology allows manufacturers to produce large quantities while maintaining high quality. Companies that adopt Additive Friction Stir Processes can respond more quickly to market demands, as production can be adjusted more easily than with conventional methods.
Environmental Considerations
Environmental considerations come into play as global industries strive for sustainability. Additive Friction Stir Processes show promise in reducing carbon footprints. Due to the lower waste generation compared to traditional methods, this process contributes to more sustainable practices. Furthermore, the ability to process recycled materials enhances its eco-friendliness.
Moreover, these processes typically require less energy due to their efficient material utilization. An important aspect is also the reduction in harmful emissions associated with many manufacturing processes. By adopting Additive Friction Stir Processes, companies can align their practices with environmental regulations and standards, thus enhancing their corporate responsibility.
The integration of Additive Friction Stir Processes not only advances manufacturing capabilities but also aligns with sustainability efforts, making it a responsible choice for modern industries.
In summary, the benefits of Additive Friction Stir Processes highlight advances in material properties, production efficiency, and environmental awareness. Understanding these advantages is essential for industries looking to innovate while addressing the challenges of modern manufacturing.
Applications in Various Industries
The integration of additive friction stir processes into various industries has generated significant interest due to its potential to transform traditional manufacturing approaches. The unique attributes of this technology allow for enhanced material properties and production efficiency. As industries increasingly seek sustainable and effective solutions, the relevance of these applications becomes clear. The application of additive friction stir processes not only optimizes production but also addresses specific challenges faced in diverse fields. These advancements can lead to innovations that push the boundaries of current manufacturing capabilities.
Aerospace Industry Applications
In the aerospace sector, the need for lightweight yet durable materials is critical. Additive friction stir processes offer an effective approach by enabling the production of complex geometries with optimized mechanical properties. The combination of friction stir welding with additive techniques allows manufacturers to join materials such as aluminum and titanium, commonly used in aircraft components. These components demand high strength-to-weight ratios, as well as the ability to withstand extreme conditions. The adoption of these processes can result in significant weight savings, optimizing fuel consumption and improving overall aircraft performance.
Automotive Industry Innovations
The automotive industry has recognized the advantages of using additive friction stir processes in vehicle manufacturing. With the push for lighter, more efficient vehicles, this technique can provide innovative solutions for joining different materials, including advanced high-strength steels and aluminum alloys. For example, the ability to produce intricate designs and components that require minimal machining is a substantial benefit. Furthermore, the reduction in thermal distortion compared to traditional welding methods results in higher precision components, which can significantly enhance vehicle performance and safety. Companies are investing in these processes to meet regulatory demands and consumer expectations for more eco-friendly vehicles.
Healthcare and Biomedicine Applications
In healthcare, additive friction stir processes are emerging as vital for producing medical devices and implants. The ability to fabricate titanium and specialty alloys using this technology allows for the creation of strong yet lightweight implants that can improve patient outcomes. Moreover, the processes can produce unique porous structures that promote bone ingrowth, enhancing biocompatibility. This capability is particularly important in orthopedic and dental implant applications. The technology supports tailored solutions, as medical professionals seek customized implants to meet individual needs effectively.
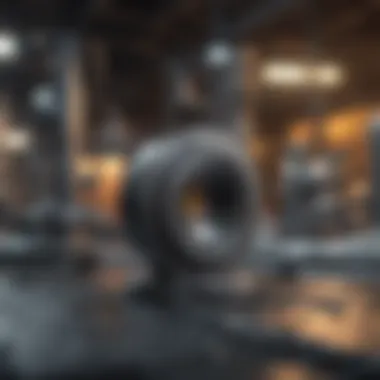
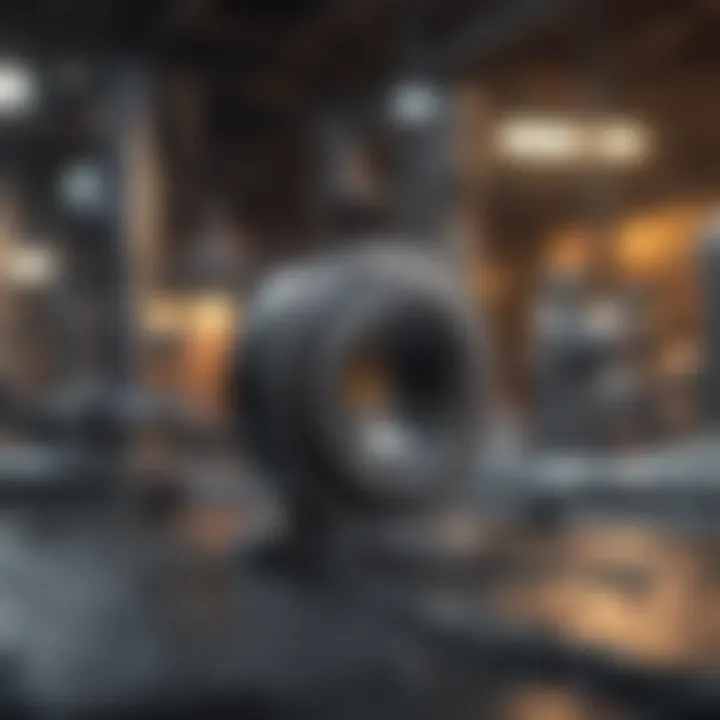
Construction and Structural Engineering
In construction, the advantages of additive friction stir processes are becoming increasingly recognized. The construction industry often requires robust materials that can withstand various environmental factors. Using these advanced processes allows for the fabrication of structural components that are both strong and lightweight. The ability to create large-scale components with minimal waste speaks to the industry’s growing demand for sustainability. Furthermore, structural engineering applications benefit from the improved reliability and performance consistency that these processes can offer, ensuring safer and more efficient building practices.
The applications in these industries demonstrate the extensive versatility of additive friction stir processes, emphasizing their role in driving innovation and efficiency across sectors.
Technological Advancements
Technological advancements play a crucial role in the evolution of additive friction stir processes. These developments are pivotal for enhancing efficiency, improving material properties, and expanding the range of applicable industries. As the field of additive manufacturing grows, innovation in machinery, materials, and integration with digital techniques becomes essential for maintaining a competitive edge.
Recent Developments in Machinery
The machinery used in additive friction stir processes has seen significant improvements. New models are more sophisticated, enabling higher precision and better control over the friction stir welding process. This precision is critical for complex geometries, particularly in aerospace and automotive applications.
Recent advancements in drive systems and tool designs have also changed the landscape. For example, the introduction of advanced spindle systems allows for variable speeds, helping to tailor the process according to the material and geometry being processed. Improved cooling systems in machinery have decreased thermal impact, further enhancing material characteristics and overall performance.
Innovations in Material Input Strategies
Innovations in material input strategies have garnered attention as a key aspect of additive friction stir processes. The focus has shifted to optimizing material feed mechanisms to improve process reliability and speed. Traditional methods are being complemented by newer techniques that enhance the material's interaction with the tool, thus boosting weld quality and material properties.
One approach involves using composite materials as input. These materials have shown promise in adding strength and reducing weight, critical factors in sectors like aerospace. Moreover, alternative feedstock such as recycled materials is gaining traction, promoting sustainability while maintaining performance standards.
Integration with Digital Manufacturing
The integration of additive friction stir processes with digital manufacturing technologies represents a significant shift in production capabilities. Digital tools enable real-time monitoring and process adjustments based on data analytics. This feedback loop allows manufacturers to maintain optimal conditions throughout production, significantly minimizing defects and wastage.
Moreover, the synergy between additive processes and digital design tools like CAD (Computer-Aided Design) streamlines the development of complex parts. This integration can accelerate prototyping and promote innovation by enabling more creative designs that were previously unattainable.
"Technological advancements in additive friction stir processes are essential for enhancing production reliability and material performance."
Challenges Faced in Implementation
In the realm of additive friction stir processes, several challenges emerge that can hinder its widespread adoption. Understanding these challenges is crucial as it allows researchers and industry professionals to devise strategies that enhance the efficiency and effectiveness of these processes. Each obstacle can have significant implications on material selection, process management, and scalability. The following sections will delve into the specific hurdles that professionals face in implementing additive friction stir technologies.
Material Limitations and Compatibility
Material selection is a critical factor in the effectiveness of additive friction stir processes. Not all materials exhibit the necessary properties to withstand the unique stresses and thermal conditions encountered during the technique. For instance, while aluminum alloys are widely accepted due to their malleability and strength, other materials like certain steels can present difficulties in the integration process.
The compatibility of different materials also poses a significant obstacle. When combining dissimilar materials, issues such as bonding strength and thermal expansion discrepancies may arise, often leading to compromised integrity of the final product. Moreover, the presence of impurities within materials may also impact their performance during the process. This necessitates ongoing research into new materials that can be better suited for additive friction stir techniques, ensuring that material interactions do not hinder advancements in this field.
Technical Complexity in Process Control
The implementation of additive friction stir processes is also complicated by the technical complexity inherent in process control. Achieving optimal parameters—such as tool rotation speed, feed rates, and the pressure applied during the process—requires precise calibration. Variations in these parameters can lead to significant differences in the quality and structural integrity of the resultant material.
Additionally, the integration of real-time monitoring systems for feedback during production is still in its early stages. Many current systems lack the sophistication to provide actionable insights into thermal profiles or material flow behavior, which are vital in ensuring consistent outcomes. Improvement in process control strategies is essential for reducing defects and enhancing the predictive capabilities of outcomes in additive friction stir applications.
Scalability of Manufacturing Processes
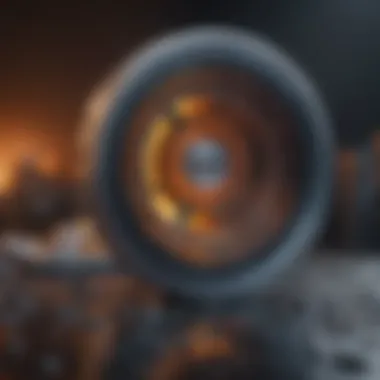
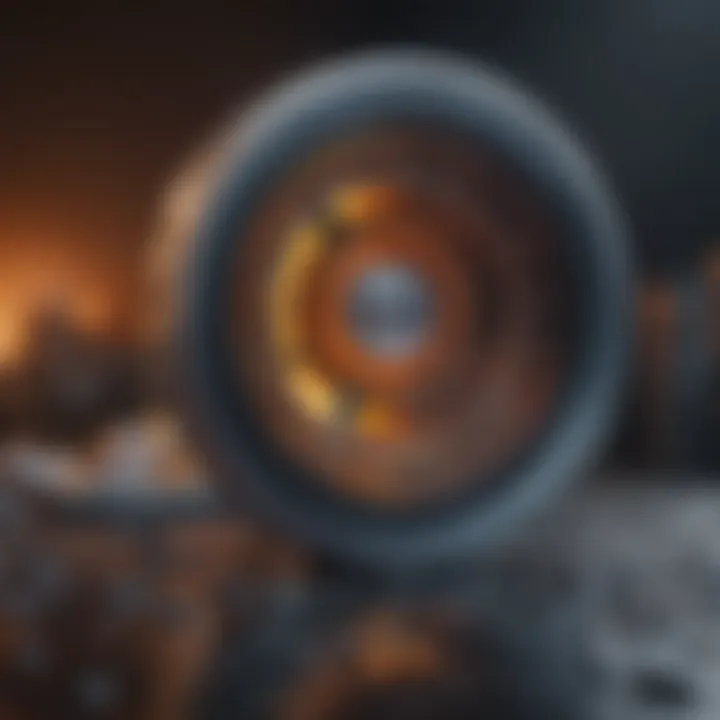
Scalability is another prominent challenge impacting the adoption of additive friction stir processes in various industries. While the advantages of this technology are clear in small-scale applications—such as prototypes or small batches—transitioning to larger-scale manufacturing is fraught with difficulty.
The intricacies of scaling up require re-evaluation of equipment and processes. Higher production volumes necessitate modifications in tool configuration and operational speed, which must still adhere to the high quality standards established in smaller-scale operations. Additionally, factors such as increased heat generation and material wastage must be addressed to ensure a sustainable approach to scaling.
"Successfully overcoming these challenges is essential for the broader implementation and acceptance of additive friction stir processes in industries that demand high-quality materials and components."
Navigating these challenges is critical for professionals in the field. As research and technology continue to evolve, focusing on solutions to these obstacles will enhance the viability of additive friction stir processes in diverse applications.
Future Directions and Research Opportunities
The landscape of additive friction stir processes continues to evolve, demanding rigorous attention to future directions and research opportunities. Focusing on this aspect is crucial because it lays the foundation for enhancing current technologies and unlocking novel applications. Moreover, as industries push for greater efficiency and sustainability, the role of research in this area becomes increasingly significant. Identifying emerging materials, refining process optimization, and fostering collaborative research initiatives are three critical elements that promise to shape the future of additive friction stir processes.
Emerging Materials for Additive Friction Stir
The exploration of emerging materials plays a pivotal role in additive friction stir technology. As traditional materials face limitations in performance, innovative material formulations may enhance the properties and capabilities of the processes. Advanced alloys, composites, and even biodegradable options are being investigated. These materials can potentially lead to lighter, stronger components in sectors such as aerospace and automotive.
For instance, titanium alloys and high-strength steels are gaining traction due to their favorable characteristics. The integration of these materials demands thorough research into compatibility with existing techniques, mechanics of joining, and overall process reliability. This ensures that the advancements do not compromise the integrity of the final products. As newer materials emerge, they open up a realm of possibilities for applications previously thought unattainable.
Enhancements in Process Optimization
Enhancements in process optimization are essential for improving efficiency and quality in additive friction stir processes. Continuous examination of operational parameters such as tool design, speed, and feed rate aids in identifying optimal settings that yield superior results. Fine-tuning these parameters helps manufacturers reduce waste, enhance cycle times, and improve the consistency of the output.
Research into digital twins and real-time monitoring systems offers a new avenue to optimize the processes dynamically. Such technologies can facilitate immediate adjustments based on live data, ensuring high-quality results while minimizing human intervention. Moreover, artificial intelligence and machine learning algorithms can assist in predicting outcomes and optimizing the processes, further pushing the boundaries of what is achievable in additive manufacturing.
Collaborative Research Initiatives
Collaborative research initiatives offer a platform for pooling knowledge, resources, and expertise from various sectors. Engaging universities, research institutions, and industry leaders can lead to significant innovation in additive friction stir processes. Such alliances can actively contribute to overcoming the technical complexities and challenges faced in implementation.
Partnerships can also drive funding for ambitious projects focused on exploring cutting-edge technologies. By fostering a culture of collaboration, stakeholders can share insights and best practices while working towards common goals, thus amplifying the impact of research outcomes.
"Harnessing collective expertise is vital for advancing additive friction stir technologies and addressing perennial challenges."
The future of additive friction stir processes hinges on a multidimensional approach incorporating emerging materials, process enhancements, and collaborative research. Emphasizing these areas will not only elevate the technological framework but also lead to groundbreaking innovations. As the demand for high-performance, customized solutions increases, these research opportunities present a roadmap for sustained advancement in the field.
Culmination
The conclusion of this article on additive friction stir processes highlights critical findings and implications for future practice. This innovative method stands at the convergence of advanced manufacturing and material science, emphasizing its importance in modern industry. Key benefits of additive friction stir processes include enhanced material properties, improved production efficiencies, and unique applications across sectors such as aerospace, automotive, and healthcare.
Summary of Findings
Throughout the article, several findings have emerged that underscore the promise of additive friction stir processing.
- Material Strength: The processes improve the mechanical properties of materials, allowing for greater durability and performance.
- Cost-Efficiency: Innovations in machinery and materials reduce production costs and time, contributing to an overall increase in manufacturing output.
- Sustainability: Additive friction stir processes align with environmentally conscious practices, reducing waste and enabling recycling of materials.
These findings collectively show that this method is not merely a theoretical exploration; it is a practical approach with tangible benefits in various industries.
Implications for Future Practice
The implications of these findings could reshape how industries approach manufacturing and material engineering.
- Research Initiatives: Further research into this technology is essential. Areas like material compatibility and process optimization call for detailed exploration.
- Education and Training: As additive friction stir technology evolves, professionals in the field must adapt. Educational programs should include advanced training on these processes to prepare upcoming engineers and technicians.
- Collaboration Across Sectors: There is a need for collaboration among industry stakeholders, researchers, and educational institutions. Shared knowledge will drive innovation, leading to more efficient and effective applications of additive friction stir processes.
The advancement of additive friction stir technology offers extensive potential that should not be overlooked. It promises to lead to breakthroughs in material performance and sustainability in manufacturing.