CW Laser Technology and Its Impact on Fabrication
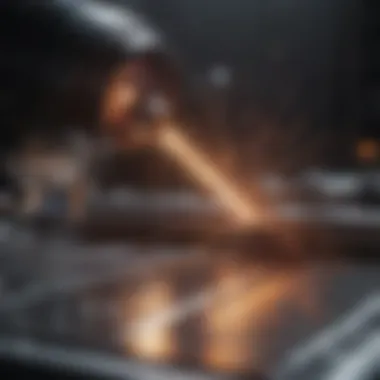
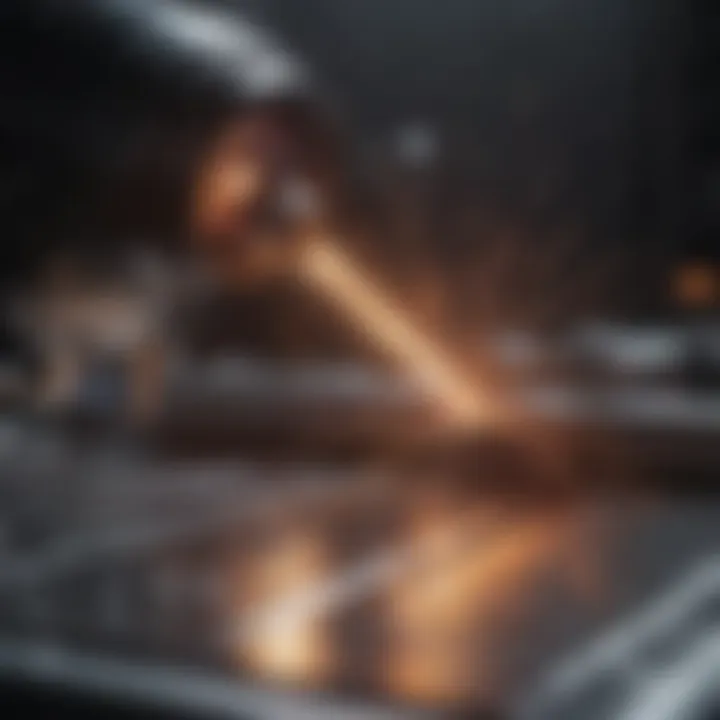
Intro
Continuous wave (CW) laser technology has emerged as a pivotal force in the evolution of fabrication processes across diverse industries. This technology operates on the principle of delivering a continuous stream of laser light, leading to enhanced precision and efficiency in various applications. The integration of CW lasers into manufacturing highlights a shift towards adopting high-tech solutions that drive productivity and quality.
The relevance of this topic cannot be overstated. With the growing demands for faster production times and improved output quality, manufacturers are increasingly turning to innovative technologies like CW lasers. The impact reaches beyond mere operational effectiveness; it fundamentally changes the standards by which products are created and measured.
In this article, we will unpack the core principles of CW laser operation, explore their myriad applications, and discuss the challenges they present. Our examination is aimed at giving students, researchers, educators, and professionals a profound understanding of how CW lasers have transformed fabrication methodologies. Equally, we will consider future prospects, ensuring a holistic view on the technology and its implications in manufacturing.
Prologue
Continuous Wave (CW) laser technology represents a significant advancement in the field of fabrication processes. The emergence of CW lasers has transformed how various industries approach manufacturing, offering new levels of precision and efficiency. This technology leverages a constant output of laser energy, which is essential for numerous applications ranging from metal cutting to additive manufacturing.
The importance of CW lasers lies not only in their operational characteristics but also in the multiple benefits they confer in fabrication. These lasers enable smoother processing of materials, which can reduce energy consumption and waste. For manufacturers, this means optimizing production workflows and minimizing downtime.
Moreover, as industries evolve toward more automated and digital manufacturing environments, CW lasers are becoming central to achieving competitive advantages. The ability to integrate seamlessly with robotic systems adds to their value in manufacturing settings.
As the article unfolds, we will explore three key areas:
- Definition of CW Lasers
- History and Evolution of Laser Technology
- Purpose of the Article
These sections will provide a foundational understanding of what CW lasers are, trace their development over time, and clarify the objectives and significance of this overview.
Understanding CW laser technology is crucial for students, researchers, educators, and professionals as it highlights the technological advancements shaping the future of fabrication processes.
Principles of CW Laser Operation
Understanding the principles of continuous wave (CW) laser operation is vital for realizing its transformative impact on fabrication processes. CW lasers provide a constant output of laser light, which is significantly beneficial in various industrial applications. This section dissects the fundamental aspects of laser emissions, elucidates the advantages inherent in CW operation, and compares CW lasers to their pulsed counterparts. These insights are critical for students, researchers, educators, and professionals aiming to leverage this technology in practical applications.
Basic Mechanisms of Laser Emission
The basic mechanism of laser emission involves stimulated emission, which is a crucial process for generating coherent light. In a typical laser environment, atoms in a gain medium are excited to higher energy levels. Once these atoms return to their lower energy states, they emit photons. This specific photon emission can trigger further emissions from other excited atoms, leading to a cascading effect. The emitted light is then amplified through optical feedback within a laser cavity, producing a highly concentrated laser beam.
A key characteristic of CW lasers is the continuous nature of this emission. Unlike pulsed lasers that emit light in brief bursts, CW lasers maintain a steady output, which is essential for several applications such as cutting and welding.
Advantages of Continuous Wave Operation
Continuous wave operation offers several distinct advantages that make CW lasers particularly suited for industrial use. Some of the prominent benefits include:
- Steady Power Output: CW lasers provide a consistent beam with constant energy, enabling stable processing conditions.
- Enhanced Thermal Effects: The continuous operation leads to increased thermal effects at the material surface, which facilitates effective melting and vaporization, critical for cutting and welding applications.
- Improved User Control: Operators can precisely adjust the power levels based on the needs of the process, optimizing performance for different materials.
These advantages translate into enhanced precision and efficiency during fabrication processes, solidifying the role of CW lasers in modern manufacturing environments.
Comparison with Pulsed Lasers
While both CW and pulsed lasers have their unique applications, there are key differences that set them apart. The comparison between CW lasers and pulsed lasers can be summarized as follows:
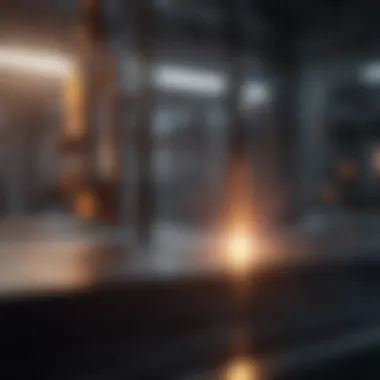
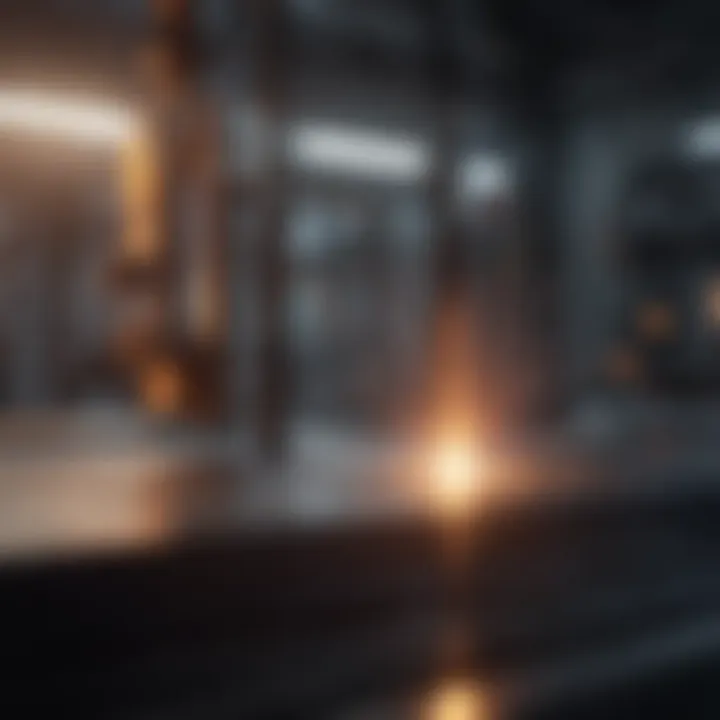
- Operating Mechanism: CW lasers emit a continuous light beam, while pulsed lasers release light in short bursts, adjusting the total energy output by varying pulse width and frequency.
- Application Suitability: CW lasers are favorable for processes that require steady heat input, such as welding and cutting. In contrast, pulsed lasers are often used for applications needing high peak power in short time spans, such as micromachining.
- Heat Management: CW lasers tend to create a larger heat-affected zone than pulsed lasers, which can be an advantage or disadvantage depending on the desired thermal effect on the material.
Applications of CW Lasers in Fabrication
Continuous wave (CW) lasers have become pivotal in various fabrication processes, revolutionizing how industries approach tasks like cutting, welding, and additive manufacturing. Their unique ability to maintain a steady beam output over time enhances precision and control in applications. Moreover, their versatility across multiple materials underscores their significance in both traditional manufacturing and high-tech fields. This section will delve deeper into specific applications of CW lasers, elaborating on their benefits and implications for industrial practices.
Metal Cutting and Welding
CW lasers are extensively used for metal cutting and welding due to their capability to provide clean, precise cuts with minimal heat affected zones.
- The power and consistency of the laser beam allow for a fine focus on the material, resulting in high-quality cuts that require little to no finishing work.
- When welding, the continuous energy input ensures stronger joints without the complications typical of pulsed lasers, which might introduce thermal stresses or defects.
In industries where metal fabrication is critical, such as automotive and aerospace, the efficiency of CW lasers brings significant advantages, reducing production time and costs while maintaining quality standards.
Additive Manufacturing
In additive manufacturing, CW lasers play a crucial role in processes like selective laser sintering (SLS). This application involves the precise melting of powders to form engineered components layer by layer.
- The ability of CW lasers to deliver a constant energy source enhances the melt pool stability, promoting better layer adhesion and less warping.
- This leads to improved mechanical properties of the final products, making them suitable for high-stress applications.
Additionally, the versatility of CW lasers allows for the use of a broader range of materials compared to traditional methods, fostering innovation in product design and functionality.
Surface Treatment Processes
CW lasers are also employed for various surface treatment processes, such as hardening and cleaning materials. By focusing a continuous beam on the surface, the laser modifies materials’ properties without affecting the overall structure.
- For instance, laser hardening increases surface hardness while keeping the inner qualities intact, extending the life of components significantly.
- Cleaning applications, like removing contaminants or old coatings, benefit from the precision of CW lasers, leading to reduced waste and chemicals.
These treatments demonstrate how CW lasers contribute to sustainability and efficiency in fabrication processes.
Micro and Nano Fabrication Techniques
The use of CW lasers in micro and nano fabrication is a rapidly developing field. At such small scales, control over laser parameters becomes crucial.
- CW lasers offer fine control over depth and precision, enabling the creation of intricate patterns or structures on materials, essential for electronics and medical devices.
- Techniques such as laser lithography harness the precision of CW lasers to produce micro-scale features that cannot be achieved with traditional machining methods.
The implications of micro and nano fabrication with CW lasers can transform product designs, leading to smaller, yet more powerful, electronic components and innovations in medical technology.
"The precision and efficiency of CW lasers in fabrication applications like metal cutting and additive manufacturing exemplify their integral role in modern industry."
Advantages of Using CW Lasers in Fabrication
The significance of continuous wave (CW) lasers in fabrication processes cannot be overstated. CW lasers represent a foundational shift in how various materials can be manipulated with precision and speed. Their unique operational characteristics offer numerous advantages that are transforming manufacturing methodologies globally. This section will explore the critical benefits of CW lasers, highlighting their impact on precision and accuracy, speed and efficiency, and versatility across different materials.
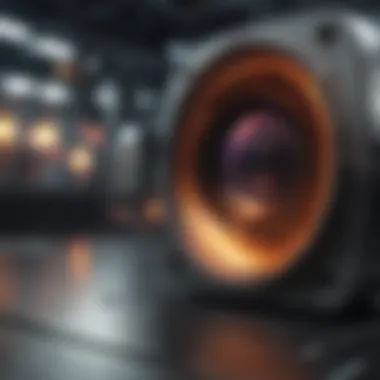
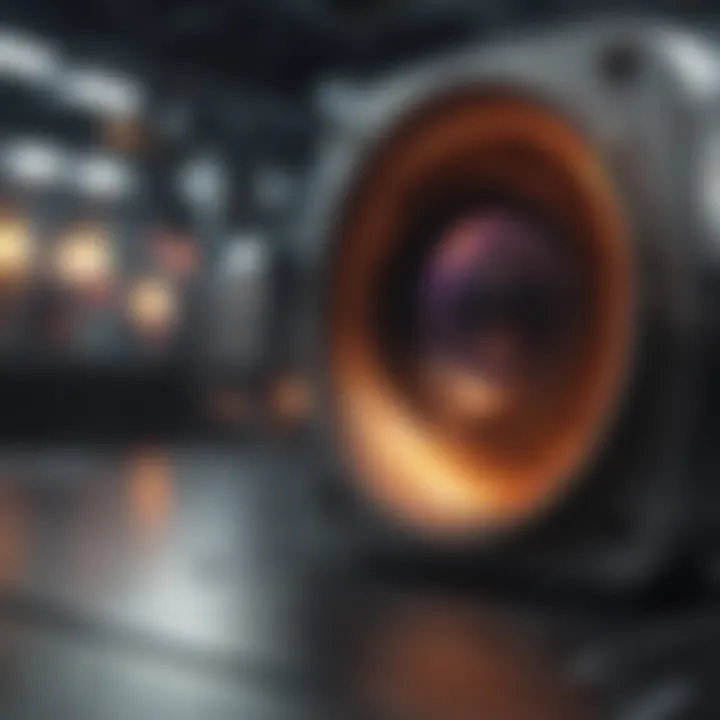
Increased Precision and Accuracy
CW lasers provide an unparalleled level of precision in fabrication tasks. The steady, uninterrupted beam ensures uniformity, which is critical in applications such as cutting and welding. This consistent operation minimizes material loss and produces cleaner cuts, which can significantly affect the final product quality. By employing CW lasers, manufacturers can achieve tolerances in the range of micrometers.
Moreover, the use of advanced beam shaping technologies enhances the topological characteristics of the laser output. This leads to better control over the thermal and mechanical properties of materials during processes like heat treatment or surface modification. As a result, companies relying on CW laser technology report improvements in their product consistency and overall performance.
Enhanced Speed and Efficiency
The operational efficiency of CW lasers is a standout feature. Unlike pulsed lasers that can experience delays between emissions, CW lasers continuously emit energy. This translates to faster processing times, allowing businesses to increase output rates significantly. For instance, in metal cutting, CW lasers can achieve cutting speeds that traditional methods find hard to match.
This speed does not come at the expense of material quality. On the contrary, the heat involved in CW laser processing can be optimized to reduce cycle times without compromising structural integrity. Manufacturers benefit from decreased labor costs and shorter lead times, enabling them to respond more dynamically to market demands.
Versatility Across Materials
One of the strongest advantages of CW laser technology is its versatility in handling a broad spectrum of materials. From metals to polymers, CW lasers can adapt to different fabrication needs. For instance, in the automotive and aerospace industries, CW lasers are employed for cutting and welding high-strength alloys. In contrast, in the electronics sector, they are adept at processing delicate materials like glass and ceramics.
The ability to tailor the laser parameters to suit various materials also enhances productivity. Adjustments in beam intensity, focus, and wavelength allow for efficient processing of different substrates. Manufacturers do not need to invest in a separate machine for each material type, which represents cost savings and space efficiency in production environments.
"The integration of CW lasers has enabled manufacturers to broaden their capabilities with increased efficiency and quality in fabrication."
Overall, the ongoing adoption of CW laser technology in fabrication processes promises to optimize production standards significantly. By improving precision, enhancing speed, and offering adaptability across materials, CW lasers are helping industries evolve and become more competitive.
Challenges in CW Laser Fabrication
Continuous Wave (CW) lasers have reshaped contemporary fabrication processes, advancing precision and efficiency. However, embracing this technology brings forth a series of challenges. Understanding these factors is crucial for industries aiming to optimize their manufacturing. Key challenges include material limitations, the formation of heat affected zones, and cost considerations. Each of these aspects requires careful attention and strategy to mitigate their impact on the overall fabrication process.
Material Limitations
Material properties play a vital role in the effectiveness of CW lasers during fabrication. Different materials respond uniquely to laser interactions, affecting outcomes in cutting, welding, or surface treatment. Not all materials are suitable for CW laser processes. For example, high reflective materials, like copper, can present difficulty as they do not absorb laser light efficiently. This can result in poor cutting quality or excessive energy consumption.
The challenge lies in selecting appropriate materials that can withstand continuous laser exposure and produce desired mechanical properties. To efficiently use CW laser technology, material scientists and engineers must conduct extensive research on suitable alternatives. This may involve experimenting with coatings or utilizing pre-treatment methods to improve laser absorption.
Heat Affected Zones
CW laser processing can inadvertently create heat affected zones (HAZ). These zones are regions adjacent to the laser-processed area that experience temperature changes due to the intense heat generated during operation. HAZ can influence material integrity and performance. Understanding the extent of HAZ is essential for ensuring that the mechanical properties of the material meet required standards for specific applications.
Managing HAZ involves careful calibration of laser parameters. Factors to consider include laser power, speed, and material thickness. Furthermore, post-processing methods, such as heat treatment or cooling strategies, may be employed to restore material properties in the HAZ. Inadequate management can lead to issues like warping or reduced toughness of the material, affecting its overall durability.
Cost Considerations
Implementing CW laser technology in fabrication processes intensifies scrutiny on cost implications. While CW lasers offer enhanced efficiency, the initial setup and ongoing maintenance can introduce significant expenses. Companies often weigh the benefits of improved speed and precision against these costs.
Additionally, the adoption of CW laser systems demands skilled operators, who require training and expertise to maximize the efficacy of the technology. Recruitment and training costs contribute to the overall expenses associated with this transition.
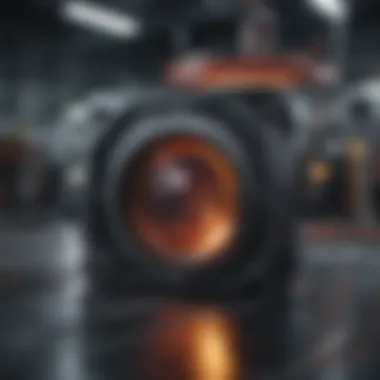
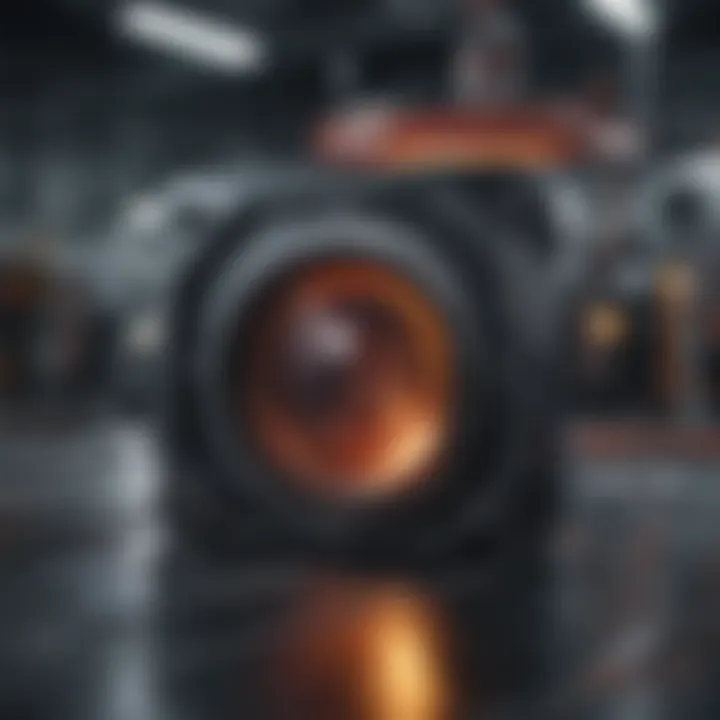
Though the long-term benefits of CW lasers may eventually offset these initial costs, businesses must remain agile in monitoring operational expenses and exploring avenues to maintain cost-effectiveness. A thorough cost-benefit analysis is essential for informed decision-making in investing in CW laser technology.
Future Trends in CW Laser Technology
As industries embrace advancements in manufacturing, the role of continuous wave (CW) laser technology continues to expand. Future trends in CW laser technology focus on enhancing capabilities, integrating novel systems, and addressing sustainability challenges. Understanding these trends is essential as they shape the future landscape of fabrication processes.
Innovations in Laser Design
Innovation in laser design is crucial for the ongoing development of CW laser technologies. Advanced designs allow for better beam quality, higher power output, and improved efficiency. Examples of such innovations include:
- Diode Lasers: Recent improvements in diode laser technology have resulted in higher efficiency and better thermal management. These are perfect for industrial applications, offering compact units that are easy to integrate.
- Fiber Lasers: They are increasingly used due to their high output power and excellent beam quality. Fiber laser technology has matured to the extent that it can handle various industrial tasks, including cutting and welding, reliably.
- Solid-State Lasers: Innovations in solid-state designs spotlight variable wavelength capabilities. This flexibility allows for applications across different materials, enhancing the versatility of laser use.
Integrating these advancements into manufacturing not only streamlines processes but also boosts overall productivity.
Integration with AI and Automation
The integration of artificial intelligence (AI) and automation into CW laser processes marks a significant step toward the future of fabrication. Machine learning algorithms can analyze data quickly, which enhances decision-making. Some potential benefits include:
- Predictive Maintenance: AI-driven systems can detect issues before they become critical, reducing downtime and maintenance costs.
- Smart Processing: Automated systems can optimize laser parameters in real-time to adapt to varying material characteristics, leading to better outcomes in quality and efficiency.
- Quality Assurance: AI can monitor production in real-time. It ensures that every piece meets predefined quality standards, reducing waste and enhancing customer satisfaction.
This fusion of technology not only streamlines operations but also creates a more adaptive manufacturing environment.
Sustainability in Fabrication Processes
Sustainability is becoming a core concern in the adoption of CW laser technology. The need for environmentally friendly practices in manufacturing has led to emerging trends in sustainability. Some key points include:
- Energy Efficiency: CW lasers typically consume less energy than traditional methods, making them a greener option. This reduction in energy leads to lower operational costs and a smaller carbon footprint.
- Material Savings: Precision cutting and welding reduce waste, allowing for a more efficient use of resources. CW lasers can process a diverse range of materials with minimal loss.
- Recyclable Materials: The push towards using recyclable materials in laser processing is increasing. Companies are seeking solutions that echo the principles of a circular economy, wherein materials are reused and recycled efficiently.
Incorporating sustainability practices plays an essential role in making fabrication processes more responsible and efficient.
As CW laser technology evolves, its integration with intelligent systems and commitment to sustainability will define the future of manufacturing.
Culmination
In concluding this article, it is vital to underscore the significant role that continuous wave (CW) laser technology plays in contemporary fabrication processes. Understanding the varied applications, advantages, and prevailing challenges provides comprehensive insight into its impact across numerous industries.
Summary of Key Points
CW laser technology stands as a game-changer in the field of fabrication. It offers precise cutting, efficient welding, and innovative opportunities in additive manufacturing. Key takeaways from this article include:
- Precision and Accuracy: CW lasers provide enhanced precision, which significantly reduces waste and improves product quality.
- Efficiency: Compared to traditional manufacturing methods, CW laser applications can lead to substantial time savings without sacrificing quality.
- Versatility: This technology can work well with various materials, making it suitable across diverse industrial applications.
- Challenges: Nonetheless, challenges persist such as limitations regarding certain materials and the implications of heat-affected zones.
These points collectively illustrate the transformative effect CW lasers have on fabrication processes, reshaping the landscape of manufacturing.
Implications for Future Research
Looking forward, future research in CW laser technology is crucial for advancing its applications and addressing existing challenges. Areas worthy of exploration include:
- Material Science: Investigating new materials compatible with CW lasers would broaden the scope of applications in various industries.
- Design Innovations: Focus on innovative laser designs can lead to more efficient and powerful systems, enhancing productivity further.
- AI Integration: Research into the synergy between AI and laser technology can enhance automation and decision-making processes within fabrication settings.
- Sustainable Practices: Exploring sustainable methods in usage and waste management will be key in reducing the environmental impact of manufacturing.
In summary, the ongoing development and integration of CW laser technology will likely redefine the efficiency, quality, and sustainability of fabricating processes. Such advancements are essential not only for industry growth but also for aligning with evolving environmental and economic standards.