Exploring Laser Sintering in Additive Manufacturing
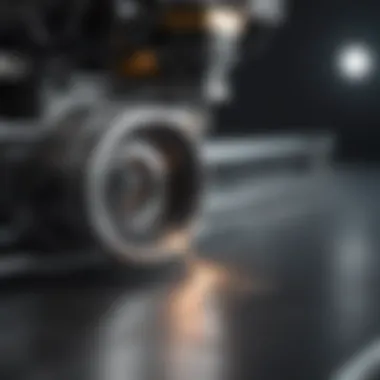
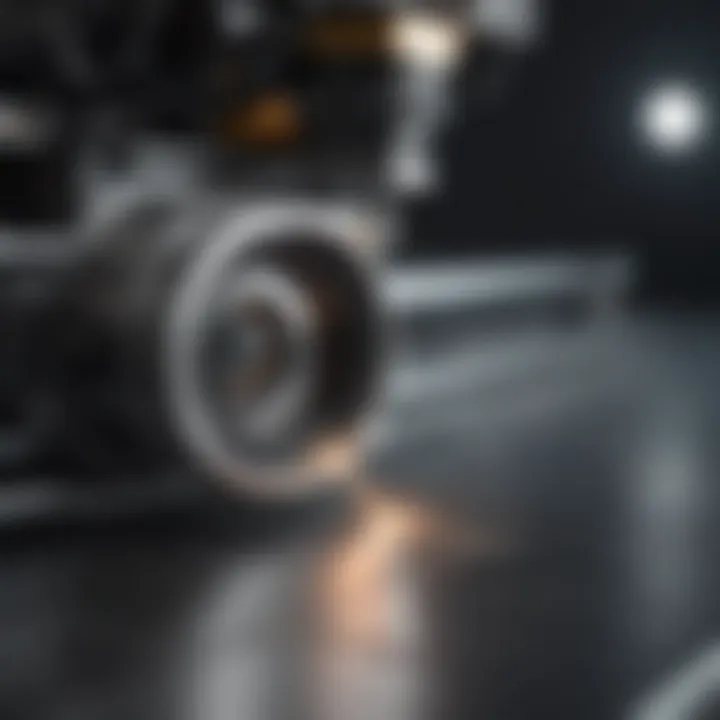
Intro
Laser sintering is a captivating technology that stands at the intersection of innovation and engineering. As a subset of additive manufacturing, it employs a highly focused laser beam to fuse powdered materials into solid structures. This transformative approach to 3D printing is making waves in various sectors, including aerospace, biomedical, and automotive industries.
At its core, laser sintering not only challenges conventional manufacturing methods, but it also opens avenues for complex geometries and customized solutions. This article aims to explore the fundamental principles, materials involved, and the far-reaching implications of this technology. With an eye on the future, it will also highlight advancements and trends that may shape the landscape of manufacturing.
In an age where efficiency and personalization are paramount, understanding laser sintering is essential for professionals and academics alike. It is imperative to grasp the subtleties of the processes and applications involved, as these insights will pave the way for informed decisions and innovative strategies. Let’s take a closer look at the highlights that lay the foundation for our exploration of this fascinating field.
Prelims to Laser Sintering
Understanding laser sintering offers a glimpse into an innovative world that has the potential to reshape industries and redefine manufacturing processes. It's no longer just about traditional methods; with the advent of laser sintering technology, the boundaries of creativity and efficiency are expanding rapidly. This section aims to elucidate the critical elements surrounding laser sintering, including its definitions, historical evolution, and its myriad applications.
Definition and Context
Laser sintering involves the use of laser technology to fuse powder materials into solid structures. This technique is part of the broader category of additive manufacturing, where materials are added layer by layer to produce three-dimensional objects. Often regarded as a cornerstone in 3D printing, it allows for creating complex geometries that would be nearly impossible to achieve through conventional methods.
To put it simply, the process starts with a thin layer of powdered material spread over a platform. Then, the laser selectively melts the powder in specific areas, creating a solid layer that, once cooled, bonds with the layers above and below. This method not only minimizes waste but also offers a level of precision and control that is hard to replicate in older systems.
Key Points in Context:
- Efficiency and Precision: It reduces material waste compared to traditional subtractive manufacturing methods.
- Material Versatility: Supports a variety of materials, making it adaptable to numerous industries.
- Design Freedom: Enables the production of complex shapes that challenge conventional manufacturing limits.
Historical Development
Delving into the historical background of laser sintering illuminates how technology can progress from rudimentary concepts to today’s sophisticated applications. The foundation of laser sintering dates back to the 1980s, when early innovators began to explore how lasers could be employed to build objects layer by layer.
In 1984, the term "selective laser sintering" was first coined by Dr. Carl Deckard at the University of Texas. This marked the beginning of a new era in manufacturing.
By the 1990s, commercial applications started emerging, largely in engineering and prototyping contexts. Companies recognized the potential to quickly produce functional prototypes, which helped accelerate product development cycles. More recently, technological advancements have transformed laser sintering into a mainstream solution for not just prototyping, but also for final part production in sectors like aerospace, automotive, and medical devices.
The continuous evolution of materials and processes, including advancements in laser technology itself, has led to more refined results and expanded capabilities. These historical strides highlight a relentless pursuit of excellence that continues to shape today's landscape of manufacturing.
"The history of laser sintering is not just about technology; it's about reimagining what’s possible in manufacturing."
In summary, the introduction to laser sintering reveals its pivotal role in evolving manufacturing practices. Understanding its definition and historical background allows readers to appreciate its relevance and potential in various fields.
Fundamental Principles of Laser Sintering
Understanding the Fundamental Principles of Laser Sintering is essential for comprehending how this technology transforms digital designs into tangible products. The mechanisms at play, the pivotal role of the laser, and the detailed process of sintering all contribute to the overall efficiency and effectiveness of this additive manufacturing method. By dissecting these principles, we can better appreciate the nuances of laser sintering, which has become a cornerstone in industries like aerospace, automotive, and biomedical applications.
Basic Mechanisms
At its core, laser sintering operates through the precise fusion of powdered materials, often metal or polymer, via heat generated by a focused laser beam. This process starts with a thin layer of powder being spread across the build platform. The laser selectively targets areas according to a digital file that dictates the object’s geometry. This action induces localized heating, raising the temperature of the particles just enough to allow them to adhere to each other without reaching a full melt.
The key mechanisms include:
- Layering: Each layer of powder is applied methodically, allowing for a build-up of the product incrementally.
- Selective Heating: The laser's precise movement and control ensure that only intended areas are sintered, achieving intricate designs and reducing material waste.
- Cooling: Post-laser exposure, the parts must cool down gently to prevent deformities, allowing for stable structures to form.
"Laser sintering combines precision with versatility, making it an invaluable tool in creating complex geometries that traditional manufacturing methods struggle to replicate."
Role of the Laser
The laser plays an instrumental role in the laser sintering process. It's not just any beam of light; it's a finely-tuned, high-intensity laser designed to operate in specific wavelengths depending on the material in use. It’s the magic wand that brings digital designs into reality.
Several aspects highlight its significance:
- Intensity Control: Adjusting the laser's intensity can determine how much heat is delivered to the powder, affecting the density and strength of the finished product.
- Precision: The focused beam allows for intricate design details to be realized, enabling manufacturers to produce models that wouldn’t be feasible through conventional methods.
- Speed: Rapid scanning capabilities mean lasers can cover large surface areas quickly, which is crucial for increasing overall build speeds in production settings.
Sintering Process Explanation
The sintering process is a sequence of meticulously orchestrated steps that unfold as the powdered material is transformed. After the initial layer of powder is laid down and the laser traces the defined pattern, the real act of sintering starts.
- Laser Activation: The laser beam hits the selected areas, causing the powder to fuse together. This creates a solid outline of the desired part.
- Layer Addition: Once the first layer cools and solidifies, a new layer of powder is spread over the build area, repeating the activation step in targeted areas.
- Layer Consolidation: This layering continues until the part is fully formed, with each layer bonding to the one below it, resulting in a cohesive solid object.
- Post-Processing: Finally, the component is removed from the build chamber and may undergo additional processes such as cleaning, curing, or machining to achieve the intended final properties.
Through these principles, laser sintering establishes itself as a foundational technology within modern manufacturing landscapes. As more industries recognize the flexibility and accuracy it brings, understanding these fundamental aspects becomes increasingly important for everyone involved in product development and production.
Materials Used in Laser Sintering
Understanding the materials used in laser sintering is crucial for anyone interested in this technology. The choice of materials can greatly influence the quality of the final product, the manufacturing process, and the overall effectiveness of the technique in various applications. This section will delve into different powder types, their properties, and the criteria for selection, which are all essential for mastering the technology.
Powder Types
Laser sintering predominantly employs a variety of powder types, as the material is the backbone of the whole process. Each powder has its specific characteristics, which make them either advantageous or problematic in certain contexts. Commonly used powders lie within the realms of plastics, metals, and ceramics.
- Polyamide Powders (Nylon): These are widely favored due to their excellent mechanical properties and flexibility. They tend to be less expensive, and the finished parts exhibit strength and resistance to various chemicals.
- Metal Powders: Stainless steel, titanium, and cobalt-chrome tend to be the popular choices. Metal powders provide high strength and are ideal for applications in demanding environments, such as aerospace or medical implants.
- Ceramic Powders: Often used for parts requiring thermal stability or electrical insulation. They find applications in motors or as components in the automotive sector.
Understanding these powder types allows manufacturers and researchers to tailor the materials used in laser sintering to specific needs and industry requirements. The robustness of the material directly influences the structure and functionality of the finished product.
Material Properties
The properties of the powders play an important role in determining the success of laser sintering. Several key attributes should be considered:
- Particle Size and Shape: The shape and size of the particles significantly affect the flowability of the powder and, therefore, the consistency of the layers during sintering. Fine powders tend to provide better resolution but may also create issues with packing density.
- Thermal Conductivity: Powders with high thermal conductivity enable faster heat transfer during the sintering process, which can enhance production speeds.
- Flow Behavior: The ability of materials to flow freely during the sintering process impacts the efficiency of layer deposition. Powders that clump together or flow poorly may lead to defects in the final product.
Honed knowledge of material properties thus directly influences not only the performance during the manufacturing process but also the characteristics of the final piece. The right combination of properties can leapfrog technological boundaries, enhancing the application of laser sintering across various fields.
Selection Criteria for Materials
Selecting suitable materials for laser sintering involves a careful analysis of various factors to ensure the desired outcomes. Here are some aspects to consider:
- Intended Application: Understanding the specific requirements of the final product guides the material choice, as different applications have unique demands, such as load-bearing strength or thermal resistance.
- Cost-effectiveness: The economic aspect cannot be overlooked. Balancing performance with cost allows organizations to maximize their return on investment while ensuring solid resource management.
- Compatibility with Equipment: Not all powders are suitable for all laser sintering machines. It's essential to ensure that the materials selected can seamlessly integrate with the equipment used.
- Post-processing Needs: Considering the potential need for further finishing or treatments is important. Some materials may require extensive post-processing, which can add to the overall production time and cost.
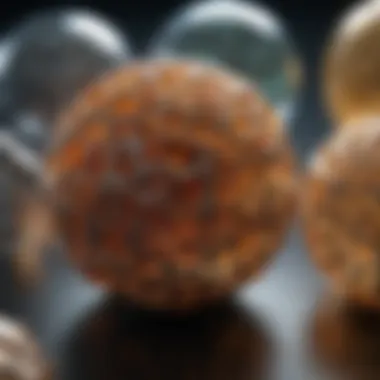
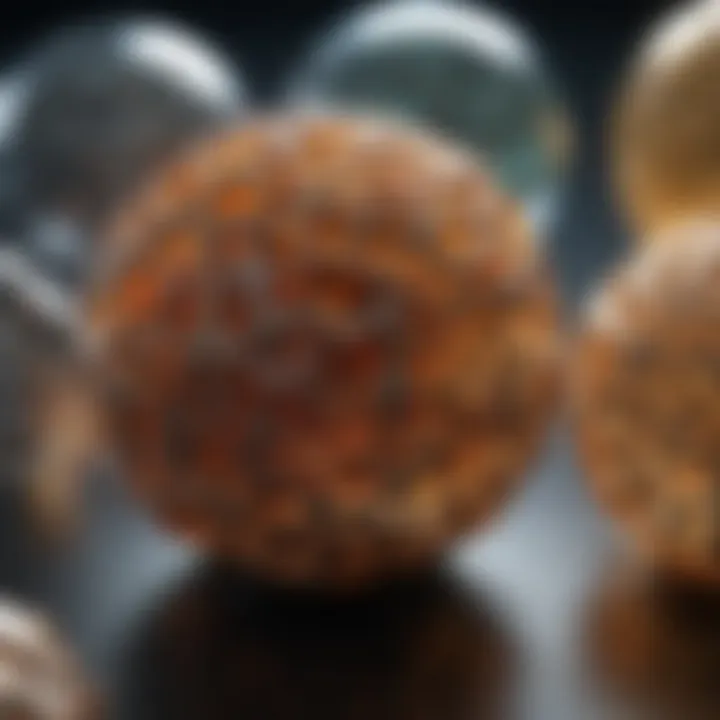
"The choice of material in the laser sintering process profoundly affects everything—from quality to cost, making thoughtful selection an art form in itself."
Choosing the right materials for laser sintering means more than picking a powder; it involves a detailed, multi-faceted approach to attain optimal results.
Advantages of Laser Sintering
Laser sintering stands out as a transformative technology within the realm of additive manufacturing. Its significance cannot be overstated, as it provides an array of benefits that traditional manufacturing processes often struggle to deliver. Delving into these advantages not only uncovers the strengths of laser sintering but also reveals why it is an invaluable option for various industries.
Precision and Detail
One of the most lauded aspects of laser sintering is its precision. The ability to produce intricate designs with remarkable accuracy is a game-changer for companies involved in sectors such as aerospace and biomedical engineering. For instance, when creating a custom implant for a patient, the meticulous detail of laser sintering ensures that the implant fits well and functions as intended. This high level of finesse is due, in part, to the method's ability to layer materials very finely, leading to more complex geometries that would be hard to achieve with other techniques.
Moreover, the precision extends to the overall quality of the parts produced. The smooth finishes and excellent surface detail mean that the final products often require little to no post-processing, saving time and resources in production.
"A stitch in time saves nine"; this old saying rings true here, as the precision offered by laser sintering preempts potential issues down the line.
Versatility of Applications
The versatility of laser sintering is another pillar of its advantages, making it suitable for a broad spectrum of applications across different industries. From crafting prototypes for consumer goods to producing end-use parts for the automotive sector, the adaptability of materials used in laser sintering is remarkable. For instance, polyamide powders can be utilized for anything from complex functional prototypes to lightweight components in vehicle structures.
Furthermore, the ability to work with various materials such as metals, polymers, and ceramics opens doors for innovative applications. In the medical field, the 3D printing of patient-specific devices or instruments has revolutionized treatment methods. Simultaneously, in the aerospace realm, laser sintering assists in creating components that are lightweight yet strong, directly affecting efficiency and performance.
Efficiency in Production
This technology also excels in production efficiency. Unlike traditional methods that can be very time-consuming, laser sintering allows for rapid manufacturing processes whereby multiple components can be produced simultaneously in a single build. This not only minimizes downtime involved in tool changes but also dramatically reduces waste material, which is a growing concern in today’s manufacturing landscape.
In addition, as designs can often be directly imported from CAD software, the leading time is significantly shortened. Quick prototyping is another aspect; adjustments can be made at the design phase and implemented almost immediately through the laser sintering process. Consequently, the reduced lead time can be crucial in industries where time-to-market is vital.
In summary, the advantages of laser sintering reveal a robust picture of a technology that not only enhances precision and performance but also meets the demands of diverse applications while pushing for efficiency in production. This trio of benefits solidifies laser sintering’s reputation as a frontrunner in the realm of modern manufacturing.
Challenges and Limitations of Laser Sintering
When discussing laser sintering, it's crucial to acknowledge that, like any technology, it comes with its own set of challenges and limitations. Understanding these aspects not only enhances our grasp of the process but also prepares us for potential hurdles in practical applications. The limitations impact material choices, overall costs, and the speed of production. By addressing these challenges, industry professionals and researchers can improve processes and innovate solutions.
Material Limitations
Materials play a central role in laser sintering, impacting the quality and applicability of the finished product. However, not all materials are compatible with the process. Typically, nylon-based powders, metals and certain ceramics are prevalent, but the spectrum of workable materials is not particularly broad.
- Mechanical properties like strength and durability can vary significantly depending on the powder used. For instance, some materials may not achieve desired mechanical properties and can be brittle when printed.
- Thermal behavior is another issue as some powders may not sinter uniformly under the laser beam, leading to defects.
- Furthermore, size distribution of the powder particles can radically affect the results. Poor-sized particles might cause clumping, leading to inconsistent outcomes in the final product.
These material limitations mean that designers must be particularly selective when choosing their materials, limiting the creative scope that can often be found in traditional manufacturing processes.
Cost Considerations
Cost remains a substantial barrier to the widespread adoption of laser sintering. The technology has a sophisticated setup, requiring high-quality machinery and powdered materials that often come with a hefty price tag. Besides the initial investment, ongoing costs can add up too:
- Material Costs: Specialized powders designed for laser sintering tend to be more expensive than conventional materials, limiting the ability for small businesses to enter the market.
- Maintenance and Upkeep: The machines used in laser sintering need regular maintenance and calibration to ensure consistent output and precision, which can further exacerbate costs.
- Training and Expertise: Skilled personnel are essential to operate sophisticated equipment effectively. The requirement for specialized training can lead to increased operational costs and a steeper learning curve.
In the end, while laser sintering offers innovative possibilities, the financial implications can be a challenging hurdle for startups and smaller manufacturers.
Speed Constraints
While laser sintering is often hailed for its precision, it can lag in terms of speed. The layer-by-layer process of sintering powder particles with a laser is inherently time-intensive. Several factors contribute to this aspect:
- Layer Thickness: The general thickness of layers can lead to longer build times, especially if high precision is needed. Thinner layers may result in finer detail but take longer to complete.
- Build Size and Complexity: As the size and complexity of the design increase, the time taken to complete the process escalates. Designers must strike a balance between intricate designs and production time.
- Post-Processing: Once printed, parts often require post-processing steps such as cleaning, curing, or additional finishing which can add another layer to the time taken until the product is fully ready and functional.
The challenges related to speed can serve as a setback in projects where time-to-market is a key factor.
"Understanding these constraints is critical for leveraging the technology effectively and for achieving efficiency in production."
In summary, while laser sintering presents several benefits, addressing these challenges helps navigate its practical applications more effectively. Industry professionals must weigh these limitations against the advantages to make informed decisions regarding their projects.
Applications of Laser Sintering
Laser sintering has carved out a niche in the landscape of manufacturing. Its applications span various industries, highlighting its versatility and transformative potential. This section delves into how laser sintering is applied in real-world scenarios, emphasizing the unique benefits it offers, and considerations when adopting this technology in different sectors. From rapid prototyping to specialized applications in aerospace and automotive fields, the significance of laser sintering cannot be overstated.
Rapid Prototyping
Rapid prototyping is one of the most celebrated applications of laser sintering. The capability to quickly transition from a computer-aided design (CAD) to a tangible model allows designers to iterate rapidly. This quick turnaround not only saves time but also reduces costs associated with traditional prototyping methods. Imagine an engineer crafting a prototype for a complex gear; with laser sintering, they can print multiple iterations in a matter of hours. This allows for swift design modifications, facilitating a more agile development process.
Moreover, the precision offered by laser sintering ensures that prototypes are not just visually accurate but functionally reliable. The use of a variety of materials, including plastics and metals, further enhances the applicability, making it a go-to choice for industries ranging from consumer goods to machinery.
Aerospace Components
In the aerospace sector, the demand for lightweight yet durable materials is relentless. Laser sintering has emerged as a game-changer in producing components that meet these stringent requirements. Parts created through this technique are often lighter than their traditionally manufactured counterparts, contributing to fuel efficiency in aircraft.
Take the example of a complex lattice structure used in structural components; laser sintering allows for intricate designs that are simply not achievable through conventional methods. Furthermore, the inherent strength of sintered parts enables them to withstand extreme conditions, crucial for aerospace applications.
The ability to manufacture components on-demand also leads to reduced inventory costs and shorter lead times, which is pivotal for the fast-paced aerospace industry.
Biomedical Implants
In the realm of biomedicine, laser sintering holds significant promise. The customization potential it offers is perhaps its most critical advantage. Each patient's anatomy is unique; hence, the ability to produce bespoke implants tailored to individual needs can improve outcomes significantly.
For instance, dental implants and orthopedic components can be manufactured with a perfect fit. The biocompatibility of the materials used further adds to its appeal, fostering better integration with human tissues and reducing the risk of rejection.
This bespoke manufacturing also extends to prosthetics, where laser sintering facilitates the creation of lightweight and durable solutions for patients. Alternatives to traditional manufacturing processes like molding or machining can often lead to waste and inefficiencies; laser sintering mitigates such issues effectively.
Automotive Industry
The automotive industry is another domain where laser sintering has made impressive inroads. One of the standout applications here is the production of complex parts that are often too challenging to produce using conventional methods.
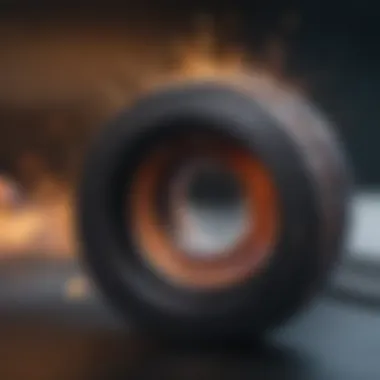
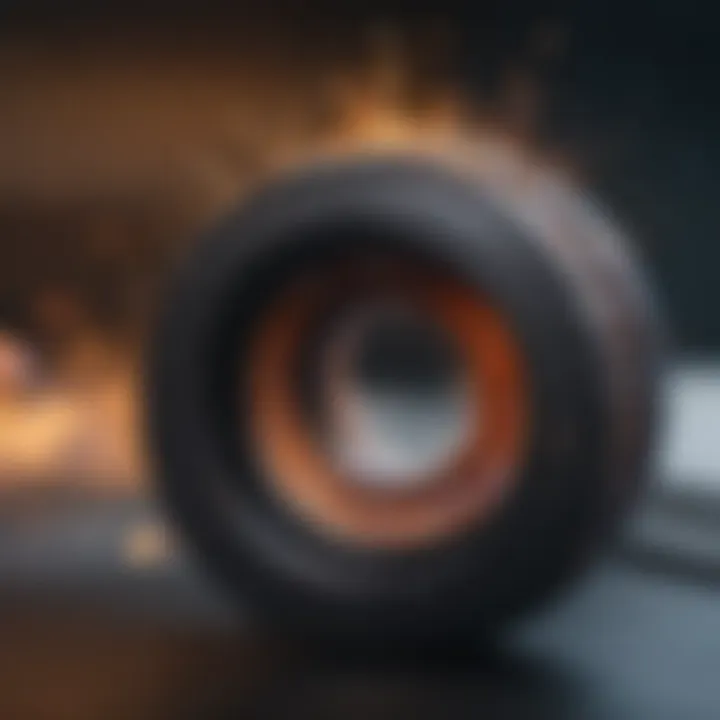
For example, components such as air intake ducts or interior elements can be designed with elaborate geometries while maintaining structural integrity.
This method also aids in reducing the overall weight of vehicles, a key factor in enhancing fuel efficiency. By shortening production cycles and minimizing offcuts, laser sintering improves sustainability, aligning with the industry's increasing focus on eco-friendly practices.
In summary, the applications of laser sintering showcase its versatility and effectiveness across various fields. As industries continue to evolve and demand more from manufacturing technologies, laser sintering stands poised to add value and innovation, making it an essential consideration for future developments.
Future Trends in Laser Sintering
The evolution of laser sintering is poised on the brink of transformation, driven by technological progress and an increasing focus on sustainability. This section not only captures the essence of existing advancements but also explores the prospects that lay ahead for this innovative manufacturing technique. Understanding these future trends is crucial for students, researchers, educators, and industry professionals alike, as they signal what lies in store for the broader field of additive manufacturing. With an eye on integration and efficiency, we can anticipate a landscape that offers deeper insights and opportunities for innovation.
Technological Innovations
As we venture into the next era of laser sintering, technological advancements are lighting the way. We witness rapid innovations that enhance both the capabilities and efficiency of the process:
- Improved Laser Systems: Recent breakthroughs have led to the development of high-powered, precision laser systems that provide sharper focus and greater power, resulting in finer printing details and broader material compatibility.
- Multi-Laser Technologies: The introduction of systems with multiple lasers operating simultaneously is a game-changer. Such configurations reduce production times significantly, enhancing the throughput of sintered parts without compromising quality.
- Smart Manufacturing Integrations: Data-driven approaches are transforming how laser sintering operates. With the integration of IoT and AI, manufacturers can now monitor equipment performance in real-time, leading to predictive maintenance, which reduces downtime and optimizes production efficiency.
"The sky is the limit when it comes to integrating advanced technologies into laser sintering processes, promising a future where production is not just quicker but also smarter."
Sustainability in Operations
In a world increasingly aware of environmental impact, the path to sustainable laser sintering is another crucial aspect to consider:
- Recycling of Materials: New methods are being developed to recycle unused powder material, which not only reduces waste generation but also cuts costs, making the overall process more economical and environmentally friendly.
- Energy Efficiency: Advances in laser technology are making systems more energy efficient. This is not only reducing operational costs but also lowering the carbon footprint associated with manufacturing activities.
- Eco-friendly Materials: There is a growing trend in developing eco-friendly materials that maintain high-performance levels while offering a reduced environmental impact. Biodegradable polymers, for example, are becoming more prevalent in the industry.
Integration with Other Technologies
The interplay between laser sintering and other cutting-edge technologies will define its future landscape:
- Hybrid Manufacturing: Combining laser sintering with traditional manufacturing techniques can optimize the production process. For instance, incorporating post-processing capabilities can enhance the functionality and aesthetics of parts, expanding application areas.
- Enhanced Software Solutions: Software platforms are being increasingly utilized for seamless integration across various manufacturing processes. Enhanced simulation capabilities allow manufacturers to predict outcomes more accurately and optimize designs before actual printing, leading to efficient resource usage.
- Collaboration with Robotics: Robotic systems are being employed to automate certain aspects of the sintering process, from material handling to post-processing, pushing the limits of productivity and precision even further.
The future of laser sintering is not just a continuation of current trends but a complex tapestry woven with advancements that touch on multiple aspects of manufacturing. As professionals and researchers in the field pursue a deeper understanding of these dynamics, they must remain alert to the nuances that drive innovation in laser sintering technology.
Case Studies in Laser Sintering
In the realm of laser sintering, understanding the theoretical frameworks is vital, but nothing quite captures the essence of its capabilities like real-world applications. Case studies in laser sintering serve as illustrative narratives that provide invaluable insights into how this technology functions within various sectors. By examining specific instances of its application, one can discern not only the mechanics behind the process but also the implications of those applications on efficiency, quality, and innovation in the industry.
The importance of case studies in this context lies in their ability to bridge the gap between theory and practice. They reveal the successes and pitfalls experienced by leaders in the field, offering a practical lens through which stakeholders can gauge viability and make informed decisions. This discussion can lead to better understanding and inspire future advancements in laser sintering technology.
Industry leaders' Adoption
When it comes to laser sintering, some industry giants have fully embraced this technology to rethink production methods. For instance, companies like General Electric have successfully integrated laser sintering into their manufacturing processes, particularly for aerospace components. By adopting this technique, they have drastically reduced production times while simultaneously enhancing the performance characteristics of their parts.
Moreover, Boeing has ventured into laser sintering for the development of lightweight components aimed at fuel efficiency. Their case is a testament to how legacy industries are pivoting to modern solutions for traditional problems. The choice to adopt laser sintering reflects a larger trend where organizations are not merely keeping up with advancements but actively leading the charge toward innovative manufacturing processes.
The benefits observed by these industry leaders include:
- Reduction in Material Waste: Laser sintering utilizes materials more effectively than traditional subtractive methods.
- Customization: Manufacturers can rapidly prototype and produce custom parts that fit specific needs.
- Supply Chain Efficiency: By producing components in-house, companies can mitigate supply chain disruptions—a critical factor in today's volatile market.
These real-life examples underscore the growing recognition and acceptance of laser sintering as a viable manufacturing solution.
Innovative Applications
The scope of laser sintering goes beyond conventional applications, stretching into realms that showcase its versatility and equipped potential. One particular instance is in the biomedical field, where this technology has been adopted for creating complex implants tailored specifically to a patient's unique anatomy. For example, Amedica Corporation has utilized laser sintering to produce spinal implants that are not only tailored to fit individual patients but also infused with materials promoting bone growth—something traditional methods struggled to achieve.
In addition to biomedical applications, the fashion industry has also taken a fancy to laser sintering. Designers are crafting intricate fashion accessories that could previously only be dreamed of. 3D printing through laser sintering allows for the creation of unique, geometrically complex pieces that can elevate a fashion line. This ability to innovate not only stands out but also allows designers to tap into those elusive niche markets.
Beyond these fields, supply chains in the electronics sector are experiencing a renaissance, with firms employing laser sintering to create lightweight, high-conductivity electronic components. Some examples include light-weight cases or even custom circuit boards, showcasing the limitlessness of what laser sintering technology can achieve.
To encapsulate, the analysis of case studies in laser sintering not only confirms the technological prowess and adaptability of this manufacturing technique, but it also highlights its ongoing evolution and the significant impact it has across numerous innovative applications. By looking into how industry leaders adopt these methods and the innovative outcomes that result, one gains a multi-faceted perspective of laser sintering's potential.
Environmental Impact of Laser Sintering
The environmental implications of laser sintering are significant and worthy of examination. As industries push for innovation while maintaining sustainability, understanding how laser sintering affects our planet becomes paramount. The process of laser sintering, fundamentally a method of additive manufacturing, utilizes energy and materials that can have varying degrees of environmental impact. Thus, it's essential to scrutinize specific elements like energy consumption and waste generation to evaluate the overall sustainability of the technology.
Energy Consumption
Energy consumption in laser sintering is a critical factor affecting its environmental footprint. Unlike traditional manufacturing methods, which often involve high-speed production runs and elaborate tooling, laser sintering operates differently. The process ensures that energy is applied precisely where it's needed, resulting in a more optimized use of resources. However, one must consider the source of this energy.
- Renewable vs. Non-renewable Energy Sources:
If a facility powering its laser sintering machines uses electricity from fossil fuels, this could exacerbate its carbon footprint. Conversely, embracing renewable energy sources—like solar or wind—can sharply reduce emissions. Choosing energy-efficient systems and machinery also plays a vital role in minimizing overall consumption. - Operational Considerations:
The operational efficiency of laser sintering machines varies. Some newer models are designed with energy-saving features, allowing them to operate at reduced power levels without compromising performance. This shift not only lowers energy consumption but can help companies save on operational costs.
Ultimately, the choice of energy sources and the efficiency of laser sintering technology must be examined holistically to assess its environmental impact.
Waste Generation
Waste generation in laser sintering is another crucial aspect that merits attention. The additive nature of the process typically suggests a cleaner alternative to subtractive manufacturing techniques, which often waste significant amounts of material. However, waste is still an issue worth addressing, encompassing both unused materials and by-products.
- Powder Reusability:
One of the significant advantages of laser sintering is the ability to reclaim and reuse unfused powder, which can make a considerable dent in waste generation. Often, up to 70% of unused powder can be recycled in subsequent prints, thereby minimizing unnecessary waste and saving materials. - By-products and Emissions:
Even with efficient powder usage, there are other by-products to consider. For instance, some materials used in laser sintering may release fumes during the heating process. Therefore, ensuring proper ventilation and filtration systems can aid in minimizing any harmful emissions released into the environment.
In summary, while laser sintering presents a modern approach to manufacturing with potential eco-friendly advantages, careful management of energy consumption and waste generation is paramount. Industry stakeholders must weigh these factors diligently as they strive for technological advancement while being stewards of the environment.
Comparative Analysis with Other Additive Manufacturing Techniques
A comparative analysis is vital for understanding the specific strengths and weaknesses of laser sintering in relation to other additive manufacturing techniques. By distinguishing the characteristics of these methods, professionals from varied industries can make informed decisions regarding their applications. Laser sintering stands out not only for its precision but also for the types of materials it effectively processes. In contrast, examining other techniques offers insights into different operational functionalities, efficiencies, and potential drawbacks. Such an analysis can benefit sectors from aerospace to healthcare, clearly showcasing how laser sintering aligns or diverges from other manufacturng processes.
Fused Deposition Modeling
Fused Deposition Modeling (FDM) is one of the most recognized additive manufacturing methods, particularly popular among hobbyists and small businesses. This technique involves extruding a thermoplastic filament through a heated nozzle, layer by layer, to create a 3D object. The ease of use and affordability of FDM machines contribute to its widespread adoption. However, while it offers good dimensional accuracy, the resolution may not be on par with that of laser sintering.
- Advantages of FDM include:
- Conversely, FDM tends to exhibit some limitations:
- Cost-effectiveness, especially for small runs.
- A wide range of materials can be used such as PLA and ABS.
- Relatively accessible technology helps beginners get started easily.
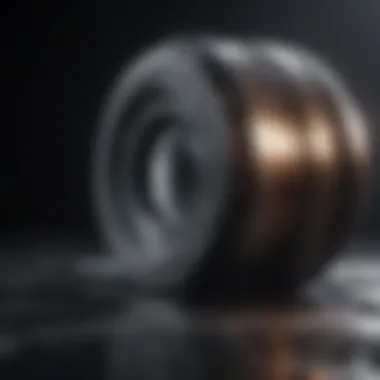
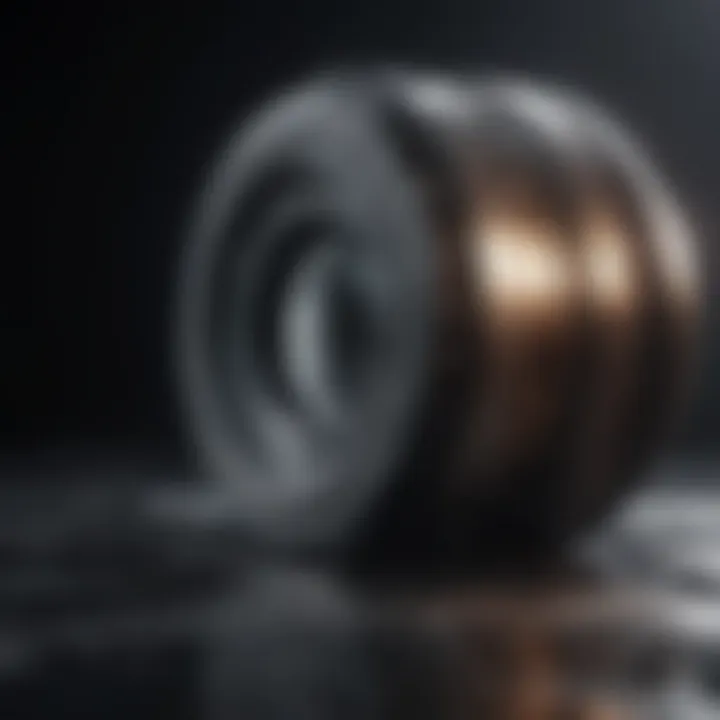
- Reduced strength and surface detail compared to laser-sintered parts.
- Layer adhesion issues can lead to weaker structures.
The choice between FDM and laser sintering often comes down to the specific application requirements. For example, while FDM may be adequate for prototypes, industries requiring engineering-grade components may lean towards laser sintering for its superior mechanical properties.
Stereolithography
Stereolithography (SLA), another prominent additive manufacturing technique, employs a different approach altogether. This method uses a UV laser to polymerize a liquid resin, solidifying it layer by layer into a defined shape. SLA is known for its ability to produce highly detailed and smooth parts. This resolution can render intricate designs with extraordinary subtlety. Therefore, it's often the go-to option for applications necessitating impeccable finish and aesthetics, such as in the jewelry and dental industries.
Some noteworthy aspects of SLA include:
- Benefits of Stereolithography:
- However, challenges persist with SLA as well:
- Exceptional surface quality and detail.
- Capable of creating complex geometries not easily achievable with other methods.
- The materials used can sometimes be more expensive.
- Parts may require post-processing to remove supports and improve strength.
Ultimately, comparing SLA and laser sintering highlights the particular applications each technique might better serve. While SLA might excel in detail, laser sintering could be more appropriate for the production of durable and functional prototypes.
"Choosing the right additive manufacturing technique truly depends on the specific needs of the project, highlighting the myriad of options available within modern manufacturing."
In summary, reviewing these additive manufacturing techniques uncovers clear differentiation in processes, resulting in important implications for their application in industry. By analyzing the specific capabilities and limitations of each method, it becomes evident that laser sintering holds a unique position, ideally suited for high-precision components where durability and material diversity are paramount.
Regulatory and Safety Considerations
In the ever-evolving landscape of laser sintering, regulatory and safety considerations stand as cornerstones that uphold the integrity of the process. Understanding these aspects is vital not just for compliance but also for enhancing operational efficiencies and ensuring the safety of personnel involved in the manufacturing process. Proper adherence to these guidelines can mitigate risks and foster innovation within the field.
Standards and Guidelines
Standards in laser sintering dictate how processes are developed, implemented, and regulated across various industries. Organizations such as ASTM International and ISO have established standards that are critically important:
- ASTM F2921-13: This standard addresses the requirements for additive manufacturing technology, specifically regarding laser sintering. It ensures that processes meet minimum quality and safety benchmarks.
- ISO/ASTM 52900: This provides a fundamental classification scheme for additive manufacturing processes, setting the stage for specific standards to follow.
The development and implementation of such standards minimize the chances of inconsistencies in the manufacturing process and help stakeholders engage with an effective framework. As industries that utilize laser sintering—such as aerospace, automotive, and medical—are heavily regulated, strict adherence to these guidelines can significantly influence market acceptance and technological adoption.
Benefits of Compliance
Compliance with regulations not only helps in avoiding legal ramifications but also promotes a transparent environment where stakeholders can trust the quality of produced goods. Some benefits include:
- Risk Reduction: Comprehensive adherence to safety standards lowers incidences of accidents and product failures.
- Market Access: Being compliant with widely recognized standards opens up new markets and enhances competitiveness.
- Enhanced Reputation: Companies that prioritize regulatory compliance earn a reputation for quality and reliability, leading to consumer trust and repeated business.
Safety Protocols
Safety protocols in laser sintering address the operational hazards that may arise during the fabrication process. These protocols ensure that personnel minimize exposure to potentially harmful factors:
- Laser Safety: These protocols require specific safety measures, such as protective eyewear and appropriate laser enclosures, to safeguard workers from exposure to laser light, which can cause severe eye injuries.
- Material Handling: Precautions must be taken when handling powders, ensuring that employees are well-versed in recognizing and managing dust-related health risks.
- Emergency Procedures: Establishing clear emergency procedures can be lifesaving. This includes training personnel on how to respond to accidents or hazardous material spills effectively.
By embedding these protocols within the corporate culture, firms can create an environment that prioritizes worker health and safety, thus reducing absenteeism and increasing productivity.
Ultimately, maintaining a strong focus on regulatory compliance and safety protocols propels the laser sintering technology forward while safeguarding its human resources and fostering innovation in practices.
User Experience in Laser Sintering
The importance of user experience in laser sintering cannot be overstated. With the rapid advancements in additive manufacturing, the intersection of technology and human interaction becomes a pivotal focal point. A quality user experience directly influences a user's capability to operate the machinery effectively and efficiently. When operators are comfortable and confident in their environment, it enhances the overall productivity of the workflow.
Key elements that contribute to a positive user experience include intuitive interface design and comprehensive training. Each element plays an essential role in harmonizing the interaction between humans and the sophisticated systems inherent in laser sintering. Let's delve deeper into these specifics, focusing particularly on how they can streamline the process and mitigate common operational hiccups.
Interface Design for Operators
A well-crafted interface serves as the bridge between the complex functionalities of laser sintering machines and the operators who manage them. The goal of interface design goes beyond mere aesthetics; it aims for clarity, ease of use, and functionality. Operators need to access vital information promptly in a language that resonates with their knowledge and experience.
- Clarity and Intuitiveness: An effective interface is intuitive enough that operators can understand its workings with minimal guidance. This element reduces the learning curve and boosts confidence in the machine’s operation. For example, straightforward labeling of buttons or indicators can prevent misinterpretations that could lead to operational errors.
- Feedback Mechanisms: Implementing immediate feedback systems can help operators gauge the success or issues during the sintering process. A simple alert system informing operators of issues such as overheating or material shortages could facilitate timely interventions.
- Customization Options: Tailoring the interface to suit specific user needs can significantly improve the experience. Whether it’s adjusting display settings or shortcut functionalities, providing customizability can empower users, making them feel more in control of the process.
Training Requirements
In conjunction with interface design, a robust training program is a cornerstone of a positive user experience. Training empowers operators with the knowledge and skills required for effective laser sintering operation. Without appropriate training, even the most user-friendly interface might remain underutilized.
- Comprehensive Orientation: New operators should undergo extensive orientation that not only covers the basic operational procedures but also includes an understanding of troubleshooting common challenges.
- Continuous Education: The technology used in laser sintering is continually evolving. Regular training sessions can help staff remain updated on new features, functions, or best practices that may emerge.
- Mentorship Programs: Encouraging a mentorship structure within an organization can also bridge knowledge gaps. Experienced operators can provide insights and shortcuts to newcomers, fostering an environment of shared learning.
- Consider providing hands-on training sessions, enabling operators to familiarize themselves with real-world scenarios.
"Investing in user experience is not just an operational necessity; it is creating an ecosystem where technological advancements can flourish alongside human capability."
Creating a seamless user experience in laser sintering is about more than satisfying the end-users; it’s about fundamentally addressing how technology augments their workflows. In an environment where precision and efficiency are paramount, prioritizing interface design and training is not just beneficial but essential.
The End and Outlook
In the realm of additive manufacturing, laser sintering stands out as a powerful technology with significant implications for various industries. The evolving landscape of laser sintering not only points to its increasing sophistication but also highlights a growing necessity to adopt these advancements in practical applications. By focusing on both the achievements and the hurdles encountered, this article emphasizes how understanding these facets can lead to better decision-making in the deployment of laser sintering.
The essence of the discussion here is the potential of laser sintering to bridge the gap between design and practical application. As industries move towards more customized solutions, the ability to produce complex geometries with a high degree of precision becomes critically important. This technology minimizes waste, allowing for more sustainable practices amidst increasing regulatory scrutiny on environmental impacts.
Investors and researchers alike can glean benefits from the analytical insights provided in this article. Recognizing both the merits and limitations equips stakeholders to make informed decisions, encouraging thorough evaluations before the adoption of laser sintering technologies in production environments.
"As we step further into the future of manufacturing, embracing innovations like laser sintering will be pivotal for competitive advantage and sustainability."
Summary of Key Insights
In reviewing the key insights from the article, a few notable points stand out that enrich the reader's understanding of laser sintering:
- Adoption Across Industries: Laser sintering is widely accepted among diverse fields, namely aerospace, automotive, and biomedical, showcasing its versatility and adaptability.
- Material Diversity: The variety of materials that can be sintered underscores the technology's flexibility, allowing manufacturers to tailor products for specific uses and performance characteristics.
- Efficiency and Waste Reduction: By minimizing material waste and enabling rapid prototyping, laser sintering offers economic advantages alongside environmental benefits, making it an economically viable option for manufacturers.
- Collaborative Development: Shifts in technology development necessitate collaboration among engineers, designers, and material scientists to foster growth in laser sintering capabilities.
This summary serves as a launching pad for further exploration and study, urging professionals to delve deeper into the intricacies of the sintering process and its broader applications.
Implications for Future Research
As laser sintering technology continues to advance, the implications for future research are profound. Researchers should consider the following areas of focus:
- Optimization of Materials: There is considerable scope to explore new materials and their behavior under laser sintering conditions. Investigating the properties of alternative materials could yield products that perform better or are more sustainable.
- Process Efficiency: Future work should look into improving the efficiency of the sintering process itself, potentially reducing energy consumption and time without sacrificing quality.
- Hybrid Technologies: The integration of laser sintering with other manufacturing technologies, such as digital printing or traditional machining, could lead to enhanced capabilities and new product lines.
- Standardization and Regulation: On a regulatory front, establishing industry standards for laser sintering processes will be crucial in ensuring consistency and safety across applications.