Exploring PDMS: Properties, Uses, and Future Trends
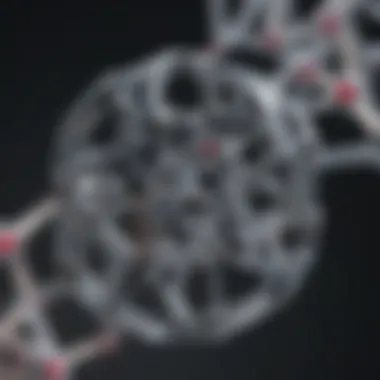
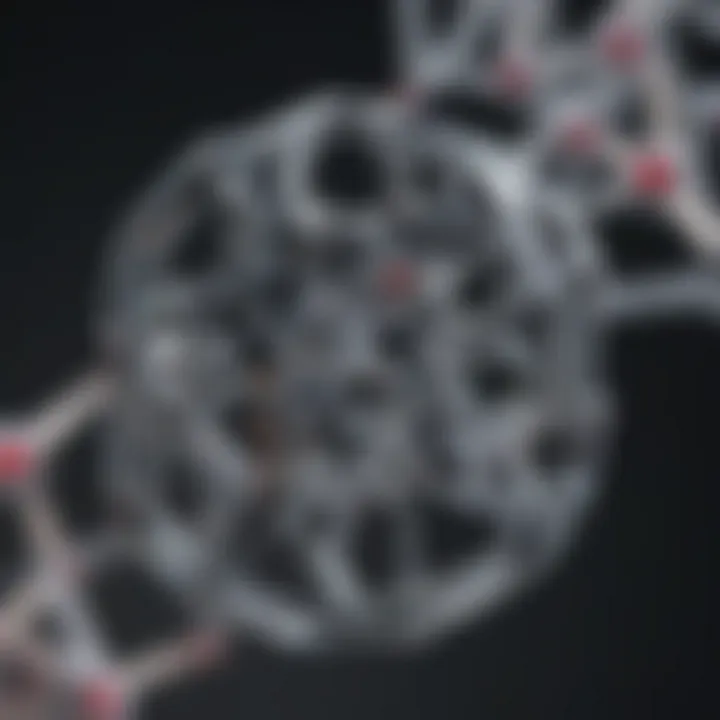
Intro
Polydimethylsiloxane (PDMS) is not just a mere silicone compound; itâs a pivotal element that interlinks numerous industries through its unique characteristics. Understanding its chemical makeup and properties can unlock a world of possibilities. Beginning with its fundamental structure, PDMS features a flexible chain of silicon-oxygen bonds, which contributes significantly to its flexibility and high thermal stability. This compound has found its way into sectors like biomedical engineering, consumer goods, and environmental technologies, owing to its versatility.
Research Highlights
Key Findings
The exploration of PDMS reveals key properties that underscore its usefulness:
- Chemical Stability: PDMS remains chemically inert under various conditions, making it reliable for long-term applications.
- Thermal Resistance: It can withstand temperatures ranging from -50°C to 200°C without significant degradation.
- Low Surface Energy: This characteristic attracts less dirt and dust, which is crucial for applications requiring cleanliness.
Even more fascinating is its biocompatibility, which has opened doors in medicine and healthcare. PDMS is often utilized in creating biomedical devices where compatibility with human tissues is non-negotiable.
"The versatility of PDMS makes it an indispensable material in todayâs technological and scientific advances."
Implications and Applications
The implications of PDMS in real-world scenarios are profound. In biomedical engineering, for instance, PDMS is used to manufacture soft and flexible implants. In electronics, PDMS serves as a vital component in microfluidics, a technology enabling precise fluid handling. Additionally, environmental science utilizes PDMS in advanced filtration systems that can tackle a variety of contaminants efficiently. Here are some of the highlights:
- Biomedical Engineering: Ideal for drug delivery systems and scaffolds in tissue engineering.
- Nanotechnology: Facilitates the creation of nanostructures, boosting research and product development.
- Environmental Science: Plays a role in remediation processes to clean chemicals from the environment.
Methodology Overview
Research Design
In order to fully appreciate PDMS, itâs essential to outline the approach taken in studies examining its capabilities. Research often emphasizes both qualitative and quantitative aspects, employing techniques from materials science and engineering.
Experimental Procedures
Experimental procedures typically include:
- Synthesis of PDMS: Various methods, including hydrosilylation, can be used to create PDMS with desired properties.
- Characterization: Techniques such as infrared spectroscopy and nuclear magnetic resonance are essential to understand chemical structure.
- Testing Applications: Evaluating PDMSâs performance through mechanical tests and environmental studies helps validate its practicality in real-world applications.
As we dissect these layers of knowledge, it becomes clearer how integral PDMS is in modern advancements across diverse industries. The continuous research and innovations surrounding PDMS are set to shape its usage in the future.
Prelims to PDMS
In an era dominated by technological advancements, understanding the materials that drive innovation is crucial. Among these, polydimethylsiloxane (PDMS) stands out as a versatile silicone compound that has cemented its place in a broad spectrum of industries. The significance of PDMS goes beyond its basic chemical composition; itâs its unique combination of properties that make it a subject of interest for students, researchers, and professionals alike. This section is vital as it sets the stage for the exploration of PDMSâs fundamental characteristics and its expanding applications.
Definition and Chemical Composition
Polydimethylsiloxane, often abbreviated as PDMS, is a polymer made up of repeating units of dimethylsiloxane. The basic chemical structure can be represented by the molecular formula [SiO(CHâ)â]n, where Si refers to silicon, O to oxygen, and CHâ represents methyl groups. At its core, PDMS is a siloxane (silicon-oxygen) polymer whose backbone consists of alternating silicon and oxygen atoms, providing it with significant stability and flexibility.
What sets PDMS apart is its chain of methly groups, which not only terminate the siloxane backbone but also contribute to its hydrophobic characteristics. This results in low surface tension and allows PDMS to resist moisture and stickiness, making it suitable for a plethora of applications from sealants in construction to lubricants in mechanical systems. Additionally, its biocompatibility and inert nature have facilitated its growing usage in the biomedical field.
Brief History of PDMS Development
The journey of PDMS began in the late 19th century, gaining traction in the 1940s due to its unique properties. Developed from raw materials sourced in the depths of the earth, PDMS was initially utilized in applications that required high thermal stability and resistance to chemical breakdown. In those formative years, it was noticeably used in products such as lubricants and emulsifying agents.
As the decades rolled on, researchers and industry professionals began to uncover more capabilities of PDMS. By the 1960s, PDMS had evolved far beyond its initial usage. Industries recognized its potential in electronic manufacturing and medical devices, significantly enhancing its market presence. Today, its applications continue to blossom, reaching into cutting-edge fields like microfluidics and nanotechnology. This historical perspective not only highlights PDMS's adaptability but also sets the groundwork for understanding its numerous applications and the advancements in research surrounding it.
Chemical Structure of PDMS
The chemical structure of polydimethylsiloxane (PDMS) plays a pivotal role in its functionality and versatility as a compound. Understanding its molecular formation not only aids in grasping how PDMS behaves under various conditions but also elucidates the reasons behind its extensive use across industries. This section will explore the foundational aspects of PDMSâs molecular makeup, focusing on both its molecular formula and siloxane bond characteristics.
Molecular Formula and Configuration
PDMS is characterized by its unique molecular formula: (C2H6OSi)n. At first glance, this straightforward breakdown might seem unremarkable, but it is crucial for understanding the properties of this material. The repeating unit in this polymer is formed by siloxane (Si-O) links, which form the backbone of PDMS.
The arrangement of the atoms within PDMS gives it a linear configuration, setting the stage for its remarkable flexibility and durability. Unlike other silicone variants, the absence of bulky side groups around the siloxane chain results in a structure that can easily deform while returning to its original shape. Thus, the molecular formula isnât just numbers; itâs the essence of what PDMS is capable of doing in various practical applications ranging from medical devices to consumer products.
- PDMS consists of segments where dimethyl siloxane units alternate with oxygen atoms in its backbone.
- The combination of its high degree of polymerization, along with the linearity of its structure, contributes to its low density and excellent thermal stability.
- Its flexible structure allows adaptability under mechanical stress, making it a prime candidate for applications needing elasticity.
Siloxane Bond Characteristics
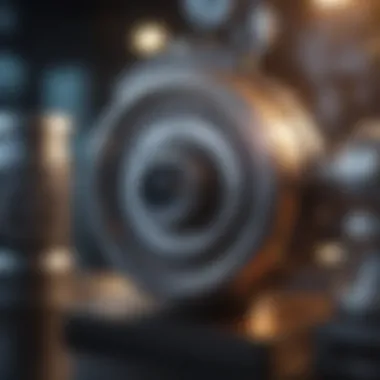
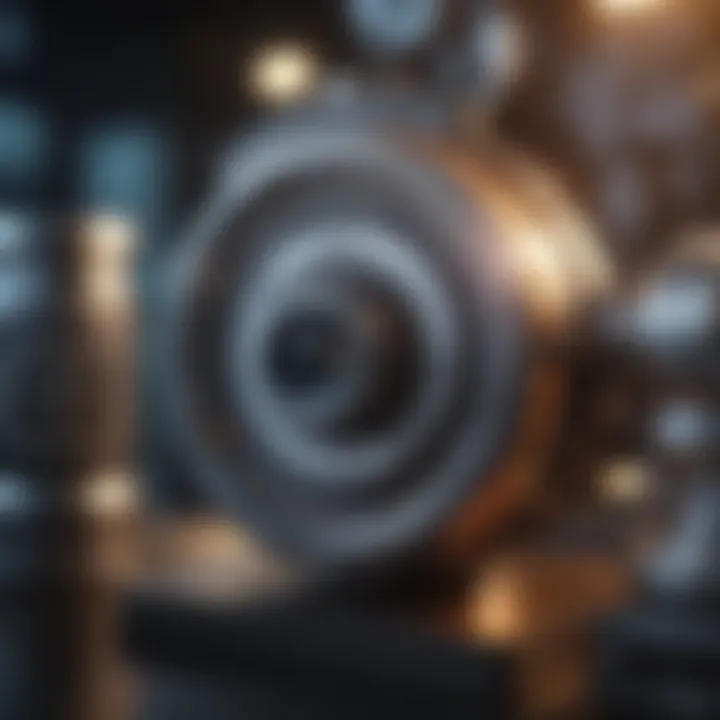
Moving from its molecular formula to the siloxane bonds, itâs critical to comprehend that these bonds impart distinctive properties to PDMS. The Si-O bonds present in PDMS are what make it unique compared to other polymers. These bonds exhibit characteristics that are not found in conventional organic compounds, and they significantly alter how PDMS interacts with its environment.
The siloxane bonds confer remarkable thermal and oxidative stability to PDMS. In practical terms, this means that PDMS can withstand high temperatures and resist degradation over timeâtraits that are mandatory in many industrial applications. Moreover, the bond length and angle in siloxane structures provide flexibility while maintaining strength.
- PDMS displays hydrophobic characteristics, meaning water droplets bead on its surface rather than spreading out. This feature makes it useful in coatings and sealants.
- The siloxane bonds enable PDMS to endure drastic temperature changes without compromising its structural integrity.
- Its unique elasticity allows it to have a lower flow rate, making it suitable in devices that require precision, such as microfluidic systems.
"The unique structural characteristics of PDMSâespecially its siloxane bondsâare the backbone of its applications in numerous fields, from biomedical to environmental science. Understanding these aspects is key for both research and industry practitioners."
Physical Properties of PDMS
Understanding the physical properties of polydimethylsiloxane (PDMS) is essential for grasping its versatility and relevance across various applications. These properties not only dictate how PDMS behaves under different conditions but also determine its suitability for specific use cases. This section dives into the individual characteristics of PDMS, including thermal stability, viscoelastic behavior, and surface properties. Each of these aspects plays a crucial role in the material's performance, affecting everything from industrial applications to biomedical uses.
Thermal Stability
PDMS exhibits an impressive thermal stability, which is a significant selling point in many industrial contexts. This ability to withstand a wide range of temperatures without degrading means it's often the go-to choice in high-heat environments, such as those found in manufacturing or even in some biomedical devices. The thermal endurance of PDMS can range from about -50°C to +200°C. This attribute enables PDMS to be used in processes that demand reliability and performance over extended periods.
Benefits:
- Wide Temperature Range: Its stability across a broad spectrum of temperatures helps maintain consistency in application performance.
- Reduced Decomposition Risk: Minimizing the risk of breakdown at elevated temperatures leads to longer functional lifespans.
- Versatility: Its thermal features allow PDMS to be suitable for diverse applications, from automotive components to electronic devices.
Despite its advantages, itâs crucial to consider that while PDMS is thermally stable, prolonged exposure to extreme conditions can still yield effects on its mechanical properties. Hence, users need to evaluate the thermal needs relative to their specific application.
Viscoelastic Behavior
Unique to PDMS is its viscoelastic behavior, a characteristic that blends both viscosity and elasticity. This trait endows PDMS with the ability to undergo deformation when stress is applied, and return to its original shape once the stress is removed. This property is particularly valuable in applications that require flexibility and resilience. For instance, in biomedical devices, PDMS can closely mimic the mechanical properties of biological tissues, providing compatibility and comfort.
Considerations:
- Stress Relaxation: PDMS will adapt to imposed forces, making it suitable for dynamic environments, such as soft robotics.
- Damping Properties: The material's ability to absorb energy can lead to applications where cushioning or sound dampening is necessary, such as in vibration control systems.
- Customizability: Variants of PDMS with different viscoelastic properties can be synthesized for specific needsâwhether a firm or more compliant material is desired.
This viscoelastic nature allows engineers and scientists to harness PDMS effectively in fields such as soft robotics, microfluidic devices, and even wearable technology.
Surface Properties and Interactions
The surface properties of PDMS contribute significantly to its functionality. With inherently low surface energy, PDMS tends to be hydrophobic in nature, making it less prone to water adsorption. This feature is exceptionally beneficial in a variety of applications, particularly in those that require minimal fouling or adhesion to liquids. Understanding these properties reveals why PDMS is often utilized in microfluidic systems or protective coatings.
Key Points:
- Hydrophobic Surface: This aspect leads to self-cleaning properties in certain contexts, making PDMS suitable for use in environments where cleanliness is paramount.
- Functionalization Possibilities: Through various chemical treatments, the surface properties can be modified to enhance adhesion or compatibility with other materials.
- Interaction with Biological Systems: In biomedical settings, the low protein adsorption of PDMS can be altered to improve biocompatibility, essential for applications in tissue engineering or implants.
Ultimately, the interplay of surface properties with other external factors can dictate the effectiveness of PDMS in real-world applications.
The physical properties of PDMS form a robust foundation for its diverse uses, and understanding these characteristics helps bring its potential fully into focus. In this light, PDMS stands out as a commendable material that meets various demands, propelling innovations across multiple fields and applications.
Synthesis of PDMS
The synthesis of polydimethylsiloxane (PDMS) is not just a technicality but a cornerstone of its vast utility across industries. Understanding how this silicone compound is produced can unlock insights into its properties and performance. By diving into the polymerization techniques and factors influencing synthesis, we can grasp the nuances that contribute to PDMS's versatility, making it a staple in countless applications.
Polymerization Techniques
PDMS is synthesized through various polymerization methods, with the most prevalent being step-growth polymerization. This technique benefits from its simplicity and effectiveness, allowing for a high degree of control over the resultant polymer's length and molecular weight.
- Condensation Polymerization: This method typically involves the reaction between silanes with hydroxyl end groups. The process generates siloxane bonds while releasing small molecules like water or methanol as byproducts.
- Anionic Polymerization: In this approach, initiating agents, often an alkaline catalyst, react with siloxanes. This method allows for more precise control over the polymer's properties.
- Cationic Polymerization: While less common, this technique involves using a cationic initiator to start the reaction. It is generally more specialized, typically reserved for applications requiring tailored properties.
These techniques can dramatically alter the characteristics of PDMS, such as viscosity and thermal stability, thereby impacting its functionality in various applications.
Factors Influencing Synthesis
Multiple factors play a pivotal role in synthesizing PDMS, significantly determining the final product's characteristics.
- Temperature: The temperature during polymerization directly affects the molecular weight and the degree of polymerization. Higher temperatures can accelerate the reaction but may also lead to side reactions that compromise the quality of the compound.
- Catalyst Type: The choice and amount of catalyst can dictate the reaction kinetics. For instance, a platinum catalyst is often preferred for its efficiency, albeit at a higher cost.
- Concentration of Reactants: The ratio of silane components influences the polymer structure. Too much of one component may lead to unevenly branched polymers, affecting the material's properties.
- Reaction Time: Allowing the reaction to proceed for an extended duration without interruption can result in higher molecular weight and enhanced product stability, but this must be balanced against the potential for degradation.
Ultimately, the synthesis of PDMS is a delicate dance of chemistry where slight adjustments can yield significant changes in performance. Understanding and refining these parameters not only enhances product quality but also opens new doors for innovative applications.
"The synthesis of PDMS is an art and science, where precision and creativity combine to form versatile materials that adapt across industries."
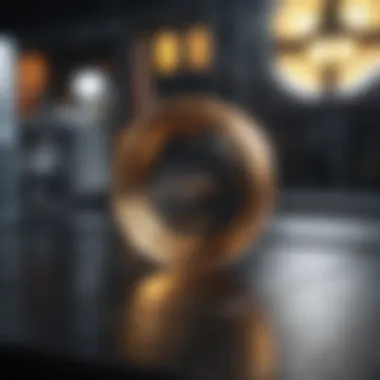
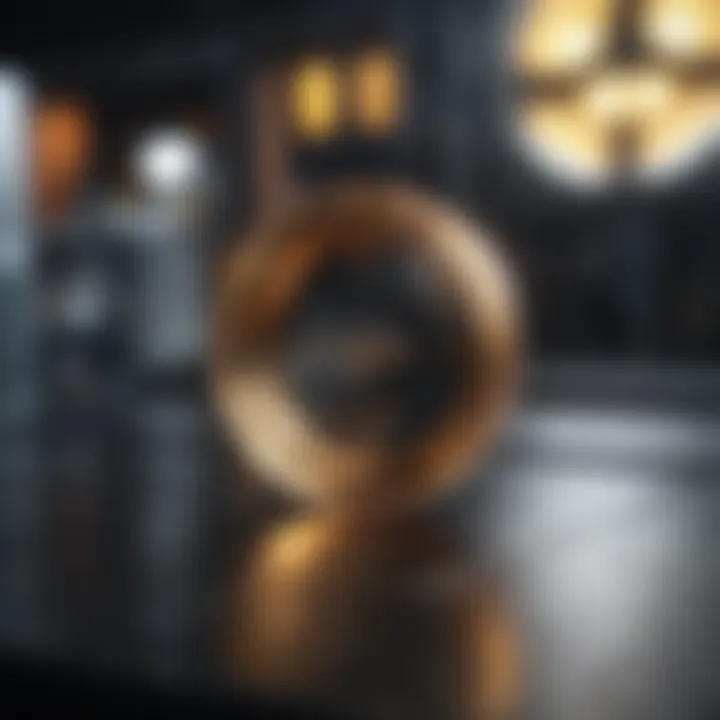
In summary, mastering the synthesis of PDMS is essential for optimizing its performance and expanding its applications in fields ranging from biomedical engineering to environmental science.
Applications in Industry
The utilities of polydimethylsiloxane (PDMS) stretch wide across various sectors, showcasing its truly versatile nature. From biomedical applications to electronic manufacturing and environmental science, the presence of PDMS in these fields highlights its significance. Itâs important to understand how specific characteristics and properties of PDMS propel its use in industry.
Biomedical Applications
Use in Drug Delivery Systems
PDMS has made significant strides in drug delivery systems, primarily due to its unique characteristics such as biocompatibility and flexibility. In general terms, drug delivery systems often aim to increase therapeutic effect while minimizing side effects. PDMS serves as an ideal medium for encapsulating drugs, providing controlled release, and protecting sensitive compounds from degradation. The permeability of PDMS can be adjusted, giving researchers the power to calibrate release rates effectively, which is quite beneficial in maintaining therapeutic levels over time.
One of its standout features in this context is its capacity to be tailored for specific drug properties, thus enhancing its effectiveness. The drawback, however, can lie in its limitations under certain biological conditions where it may not release the drug as efficiently as hoped.
Impacts on Tissue Engineering
In the realm of tissue engineering, PDMS plays a crucial role due to its outstanding structural integrity and biocompatible nature. When constructing scaffolds for tissue regeneration, the unique elastic properties of PDMS allow for good mechanical support and adaptability to dynamic movements. Its surface can also be modified to enhance cell attachment and growth, making it a popular material for creating three-dimensional tissue constructs.
Yet, while PDMS offers these benefits, a potential downside is its hydrophobicity, which may hinder certain cell types from adhering effectively. Engineers need to overcome this hurdle to maximize PDMSâs application in tissue engineering, exploring potential coatings or treatments to optimize performance.
Electronic Manufacturing
Use in Microfluidics
Microfluidics is another area where PDMS shines, owing to its ease of fabrication and moldability. Microfluidic devices require materials that can be processed with high precision, and PDMS fits the bill perfectly. Its fabricability enables the design of intricate channels that can manipulate tiny volumes of liquid, which is critical for various applications like diagnostics and bioassays. The robust nature of PDMS also means it can withstand temperature fluctuations, making it suitable for repetitive use.
However, one must take care while working with PDMS, as its soft nature can lead to swelling when in contact with certain organic solvents. This limitation requires thorough testing to ensure compatibility with the specific fluids used in microfluidic setups.
Role in Semiconductor Production
PDMS also finds a unique niche in semiconductor production as a photoresist material. Its ability to replicate fine details makes it a beneficial tool for creating molds used in the fabrication of electronic components. Besides its replication qualities, the thermal stability of PDMS is noteworthy, enabling processors to function effectively under heated conditions.
Despite these advantages, there are considerations regarding its chemical resistance to other substances involved in semiconductor manufacturing. A careful selection process is essential to avoid potential compatibility issues.
Environmental Science Applications
Role in Water Treatment
In the field of environmental science, PDMS has emerged as a crucial player in water treatment processes. Its hydrophobic properties enable it to efficiently separate oils from water. What makes it particularly effective is its ability to form a stable interface with contaminants, allowing for efficient extraction processes. This capability aids in the removal of unwanted materials, thereby purifying water resources.
The drawback, however, lies in the very property that makes it effectiveâits hydrophobicity might limit its interaction with water, leading to inefficiencies when treating certain types of pollution. Finding a balance is key in applying PDMS effectively for water treatment.
Use in Pollution Control
PDMS's utility in pollution control is mainly anchored in its ability to adsorb organic pollutants, playing an essential role in environmental cleanup. Its vast surface areaâwhen structured in membrane formsâfacilitates the capture of a wide range of surface contaminants. Furthermore, this flexibility allows it to be integrated into existing environmental systems seamlessly.
While PDMS proves incredibly effective at trapping pollutants, its disposal poses environmental concerns. There's ongoing research to explore ways to recycle or safely dispose of PDMS after its functional life cycle is over. Ensuring sustainable use while maintaining high performance is a challenge that deserves close attention.
In summary, the applications of PDMS across various industries are numerous and impactful. Its benefits are significant, but itâs crucial to acknowledge the challenges as well. Each fragement of PDMS's journey from laboratory to real-world application tells a story of innovation, consideration, and potential improvements.
Recent Advances in PDMS Research
The recent strides in PDMS research highlight not only the adaptability of this material but also its potential for future innovation. As industries evolve and seek more efficient, cost-effective, and sustainable solutions, PDMS stands out as a candidate for advancement. The exploration of PDMSâs properties, particularly in novel applications, marks an exciting frontier for researchers and practitioners alike.
Innovations in Material Properties
Innovations in the material properties of PDMS have broadened its applicability in various fields. Recent developments focus on enhancing mechanical stability, thermal resistance, and chemical durability. For instance, some researchers have been able to modify PDMS through crosslinking techniques, resulting in materials that maintain their desirable properties while exhibiting greater strength and resilience.
This flexibility opens doors in sectors ranging from biomedical engineering to electronics, where precision and reliability are paramount. Moreover, this adaptability allows for a tailored approachâscientists can create custom formulations of PDMS that meet specific performance criteria. Thus, the continued refinement of PDMS properties keeps it relevant in a fast-paced technological landscape.
Emerging Technologies
Smart Materials
Smart materials, known for their ability to respond to environmental stimuli, are a significant area of interest in PDMS research. The use of PDMS as a base in smart materials leverages its unique characteristics such as flexibility and low viscosity. One of the key traits of smart materials is their responsiveness to changes in temperature, pressure, or electric fields, making them especially useful in sensors and actuators.
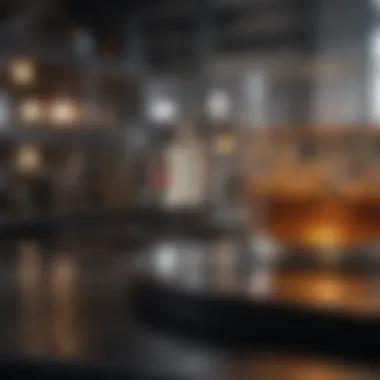
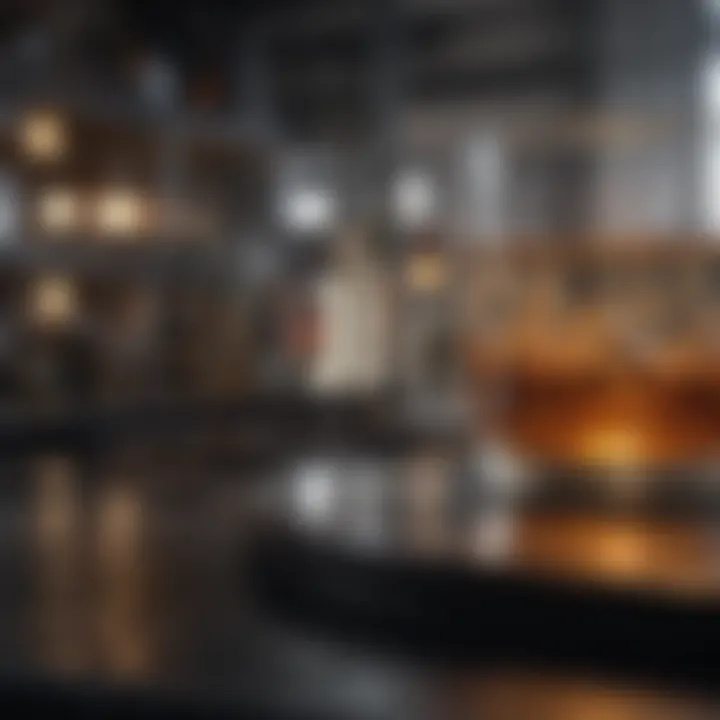
The incorporation of PDMS into smart materials has led to remarkable functionalities. For example, these materials can change shape or flow in reaction to thermal stimuli, offering exciting possibilities in adaptive technology. However, one must consider the trade-off; while PDMS offers many benefits, their temperature-sensitive nature can sometimes limit application scenarios in extreme conditions.
Nano-enhanced PDMS
The introduction of nanotechnology into PDMS research has emerged as a game-changer. Nano-enhanced PDMS involves integrating nanoparticles into the PDMS matrix, which significantly enhances its mechanical and thermal properties. The primary characteristic here is the improved strength and thermal conductivity without compromising flexibility, making it an attractive avenue for applications in electronics and energy storage.
A unique feature of nano-enhanced PDMS is its compatibility with various nanoparticles, including silica and carbon nanotubes, enabling targeted improvements. This versatility brings advantages like better electrical performance in electronic devices. However, the challenge remains in ensuring uniform distribution of nanoparticles within the PDMS, which can affect the consistency of the material's performance.
In summary, the recent advances in PDMS research not only push the boundaries of its applications but also pave the way for innovative solutions in various sectors. Understanding these advancements is crucial for students, researchers, and professionals eager to explore the future landscape of material science. The interplay between smart materials and nano-enhanced PDMS reveals the path ahead, full of possibilities for enhanced functionality and efficiency in real-world applications.
Challenges and Limitations
In the broader scope of analyzing polydimethylsiloxane (PDMS), understanding its challenges and limitations becomes crucial. While PDMS boasts remarkable properties and a wide range of applications, it is not without its drawbacks. Addressing these factors is essential for advancing its use in diverse fields.
Environmental Concerns
As we push forward in the quest for innovative materials, the environmental impact of PDMS cannot be ignored. This silicone compound is known for its high chemical stability and longevity, which, while advantageous in many applications, poses significant environmental challenges.
PDMS is resistant to biodegradation, which means that it can persist in the environment for extended periods. In landfills or aquatic environments, the accumulation of PDMS materials can lead to ecological concerns. The leaching of silicone oils into ecosystems can disrupt local fauna and flora. Moreover, as industrial applications expand, the potential for PDMS pollution increases, necessitating stringent environmental regulations.
In response to these concerns, researchers are exploring biodegradable alternatives and methods to enhance the environmentally friendly properties of PDMS. For instance, incorporating natural fillers or modifying the polymer structure could lead to materials that are both functional and less harmful to the environment.
Performance Limitations in Some Applications
Despite its versatility, PDMS does have performance limitations that can impede its effectiveness in certain applications. One notable limitation is its relatively low tensile strength compared to other materials like thermoplastics. For applications requiring significant mechanical strength or durability, relying solely on PDMS might not be feasible.
Additionally, PDMS's susceptibility to swelling upon exposure to various solvents, such as certain oils or fuels, can limit its use in some electronic and industrial contexts. This characteristic compromises the structural integrity of devices or materials that employ PDMS in environments where such substances are present.
Finally, while PDMS excels in heat resistance, it has a limited operational temperature range. At extremely high temperatures, there is a risk of degradation, affecting its long-term stability in applications that involve high thermal exposure.
"Understanding these limitations allows engineers and researchers to tailor applications of PDMS more effectively, thereby optimizing its performance while addressing environmental concerns and application specifications."
Balancing these challenges with the potential benefits requires continuous research and innovation, promoting the development of modified PDMS formulations that can navigate these hurdles more effectively.
Future Perspectives on PDMS Research
The field of polydimethylsiloxane (PDMS) is ever-evolving, with an array of possibilities that could significantly reshape its applications and influence various industries. With the increasing demand for more sophisticated and functional materials, the future perspectives on PDMS research present numerous considerations and angles for exploration. In this section, we will cover potential areas for further investigation as well as predictions for its industry impact.
Potential Areas of Exploration
As researchers dive deeper into the characteristics of PDMS, several potential avenues emerge:
- Hybrid Materials Development: Combining PDMS with other polymers or inorganic materials could lead to the creation of hybrid materials that offer enhanced properties, such as improved strength or thermal resistance. This could broaden PDMS usage in construction or automotive industries.
- Responsive and Self-healing Materials: Exploring PDMS's ability to integrate with stimuli-responsive components could pave the way for self-healing materials. Imagine coatings that can repair themselves after damage, adhering well to a range of surfaces and extending the lifespan of products.
- Bio-compatible Forms: The increased focus on medical applications calls for bio-compatible variations of PDMS. This would facilitate advancements in implant technology and regenerative medicine, significantly improving outcomes for patients.
- Nanotechnology Integration: Exploring the intersection of PDMS and nanotechnology, including nano-composites, might unlock new performance levels in microfluidics and sensors. This could enhance functionalities in environmental monitoring and diagnostics.
- Sustainability Efforts: Given the environmental concerns surrounding many synthetic materials, researching eco-friendly alternatives and recycling techniques for PDMS could have a profound impact. A shift towards sustainable practices in the production and disposal of PDMS materials could transform industry standards.
Predictions for Industry Impact
As we peek into the crystal ball, itâs crucial to consider how advancements in PDMS research may influence various industries:
- Biomedical Sector: With ongoing innovations, PDMS could become a staple in advanced drug delivery systems and tissue scaffolding. This could enhance treatment efficacy and patient care, changing the landscape of healthcare.
- Electronics: As devices become smaller and more powerful, the electronics industry may lean more heavily on PDMS for chips and flexible electronics. Its dielectric properties and ease of processing could streamline manufacturing processes, making them faster and more cost-effective.
- Environmental Solutions: PDMSâs role in addressing pollution, via advancements in filtration systems or degradation techniques, may provide critical solutions to combat environmental challenges. The material could allow for more efficient separation processes, benefitting water treatment facilities.
"The future of PDMS is not just about enhancing existing applications but also exploring uncharted territories where its unique properties can provide groundbreaking solutions across industries."
- Consumer Products: As innovation pushes toward customization, PDMS might find its way into consumer goods, enhancing qualities such as durability and comfort. From smart textiles to advanced kitchenware, the potential for growth in this sector is immense.
As we advance, these potential areas for research and predictions for industry impact not only highlight the versatility of PDMS but also establish it as a significant player in providing solutions to modern challenges.
Epilogue
In concluding this examination of polydimethylsiloxane, or PDMS, itâs crucial to underscore the multifaceted importance of this silicone compound within various industries. PDMS stands as a cornerstone in modern material science and engineering due to its unique properties and vast applications. The discussions conducted throughout this article highlight several key elements regarding the composition, applications, and the future trajectory of this substance.
Summary of Key Points
- Chemical Versatility: The unique siloxane backbone of PDMS contributes to its excellent thermal stability, viscoelasticity, and surface properties.
- Diverse Applications: Ranging from biomedical engineering to environmental management, PDMS fulfills critical roles in multiple sectors. Its adaptability allows for innovative uses, particularly in drug delivery systems and semiconductor production.
- Recent Advances: Emphasis was placed on new material properties and technologies that could redefine how PDMS is utilized. Emerging fields like smart materials and nano-enhanced variants present exciting research trajectories, where PDMS can lead the charge in innovation.
- Challenges Ahead: While PDMS is groundbreaking, potential environmental concerns and application limitations were explored. It is important to remain aware of these factors as they can affect its future in both industry and academia.
Final Thoughts on PDMS Significance
Ultimately, the relevance of PDMS in todayâs scientific pursuits cannot be overstated. As we dive into the details of its structure and properties, it becomes clear that PDMS offers not just functional advantages, but provokes thought about sustainable methods in material development. The future seems bright, with ongoing research expected to push the boundaries of what is possible with this remarkable silicone compound.
"With each advancement in PDMS technology, we step closer to innovative solutions that not only address current challenges but also anticipate future needs in diverse fields."
Thus, just as PDMS reshaped many industries, it is likely to continue to inspire new applications and breakthroughs across science and technology.