Exploring Ti6Al4V Alloy: Properties and Applications
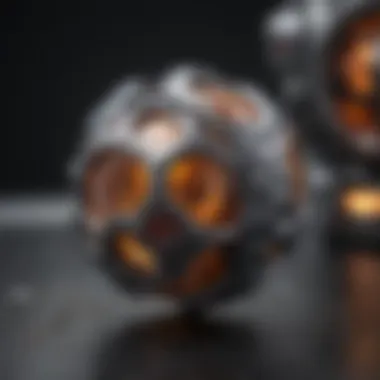
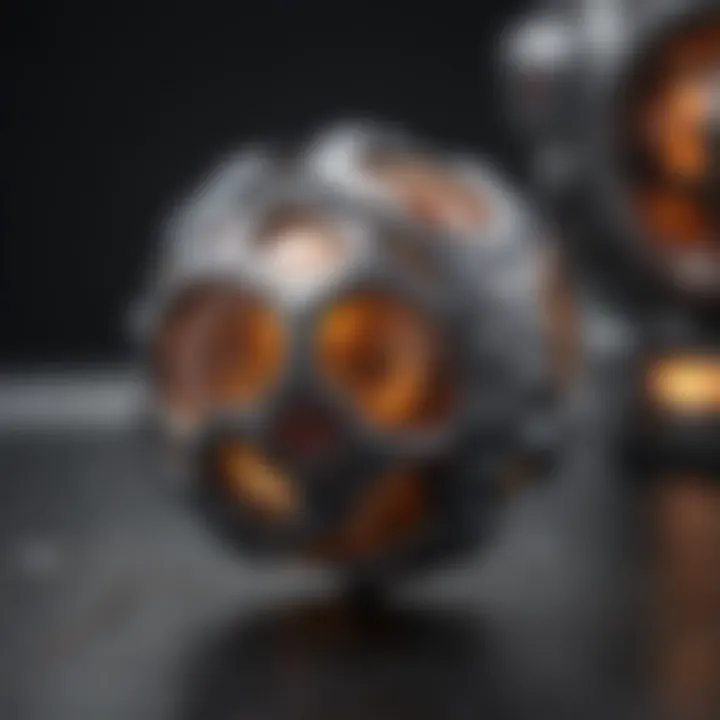
Intro
Ti6Al4V alloy, also known as titanium alloy grade 5, stands out within the realm of materials science due to its superior mechanical properties and high corrosion resistance. This alloy, comprised primarily of titanium, aluminum, and vanadium, has become a staple in various industries, particularly in aerospace and biomedical fields. As professionals and researchers seek materials that offer both strength and lightweight characteristics, Ti6Al4V has risen to the top of material selection criteria.
The importance of understanding Ti6Al4V extends beyond its basic composition. An awareness of its properties, manufacturing processes, and applications can significantly influence advancements in technology and innovation. This necessitates a thorough examination of Ti6Al4V to fully grasp its implications in the material science landscape.
Research Highlights
Key Findings
The investigation of Ti6Al4V alloy brings several key findings to the forefront:
- Mechanical Properties: The alloy demonstrates excellent fatigue resistance, tensile strength, and fracture toughness. These properties make it ideal for high-stress applications.
- Corrosion Resistance: Ti6Al4V shows remarkable resistance to both oceanic and biological environments, enhancing its suitability for maritime and medical applications.
- Manufacturing Flexibility: Through various manufacturing methods such as additive manufacturing, Ti6Al4V can be tailored for specific uses, allowing for intricate designs that meet modern engineering demands.
"Ti6Al4V alloy is increasingly recognized for its versatility and reliability, forging new paths for innovative applications across diverse fields."
Implications and Applications
The implications of Ti6Al4V’s unique properties affect numerous industries:
- Aerospace: Structural components in aircraft leverage the alloy’s lightweight nature and strength, contributing to improved fuel efficiency.
- Biomedical: In orthopedic and dental implants, the alloy's biocompatibility and corrosion resistance are critical for long-term performance.
- Automotive: Some manufacturers are exploring Ti6Al4V’s applications in performance parts, aiming to enhance vehicle efficiency.
The ongoing research and development efforts continue to reshape the landscape of material utilization, positioning Ti6Al4V as a pivotal material in future engineering projects.
Methodology Overview
Research Design
The research conducted on Ti6Al4V incorporates a multifaceted approach, combining experimental studies with theoretical analysis. This comprehensive design allows for an in-depth understanding of the alloy's performance across various conditions and applications.
Experimental Procedures
Experimental procedures typically involve:
- Characterization of microstructure using methods such as scanning electron microscopy (SEM) and X-ray diffraction (XRD).
- Mechanical testing to analyze tensile strength, fatigue properties, and elongation at break.
- Corrosion tests in different environments to determine the alloy's durability.
Such methodologies serve to solidify the understanding of Ti6Al4V's capabilities and limitations, positioning it effectively within the materials domain.
Prelims to Ti6Al4V Alloy
Ti6Al4V alloy is a titanium alloy that has garnered significant attention in various industries. Its remarkable properties such as high strength-to-weight ratio, excellent corrosion resistance, and biocompatibility make it a preferred material in aerospace, biomedical, and other engineering applications. This introduction outlines the importance of Ti6Al4V, setting the stage for deeper discussions on its composition, mechanical properties, and real-world applications.
Historical Background
The history of Ti6Al4V alloy dates back to the 1950s when titanium began to be recognized for its superior physical properties. This alloy specifically was developed to enhance the mechanical capabilities of titanium by alloying it with aluminum and vanadium. The addition of aluminum increases the strength without sacrificing too much weight, which is crucial in aerospace applications. Vanadium further contributes to the stability of the alloy at elevated temperatures. Over the decades, Ti6Al4V has become a standard titanium alloy, utilized widely in airframe structures and aircraft engines due to its robust performance under stress.
Overview of Titanium Alloys
Titanium alloys can be generally categorised into two main groups: alpha alloys and beta alloys. Ti6Al4V falls into the category of alpha-beta alloys, which exhibit a blend of properties from both types. Alpha alloys provide excellent high-temperature strength and stability, while beta alloys are known for their superior machinability and formability. The combination of aluminum and vanadium in Ti6Al4V enhances its elastic modulus and overall performance. This dual-phase structure results in a material capable of withstanding harsh environments, making it ideal not only in aerospace but also in medical devices.
In summary, Ti6Al4V represents a significant advancement in titanium alloy technology, which not only pushes the boundaries of engineering but also supports innovations in various sectors.
Chemical Composition of Ti6Al4V
The chemical composition of Ti6Al4V is central to understanding its properties and applications. This titanium alloy contains specific elements that contribute to its strength, weight, and resistance to corrosion and extreme conditions. By exploring its composition, we can appreciate why Ti6Al4V is a favored material in industries like aerospace and biomedical engineering. The careful balance of key elements not only enhances its mechanical traits but also influences processing techniques and overall performance in real-world applications.
Primary Elements
Ti6Al4V consists primarily of titanium, aluminum, and vanadium. Each of these elements plays a crucial role:
- Titanium: Makes up about 90% of the alloy. It provides excellent strength-to-weight ratio and resistance to corrosion.
- Aluminum: Constitutes approximately 6%. It acts as a stabilizer for the alloy's alpha phase at high temperatures, leading to improved ductility and workability.
- Vanadium: Comprising about 4%. This element adds strength and enhances the alloy's overall mechanical properties.
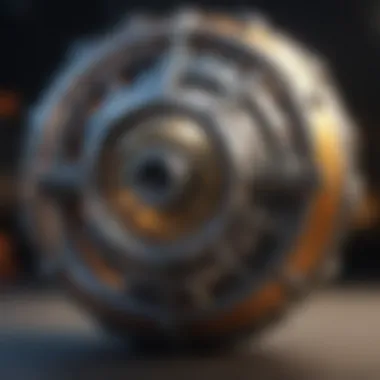
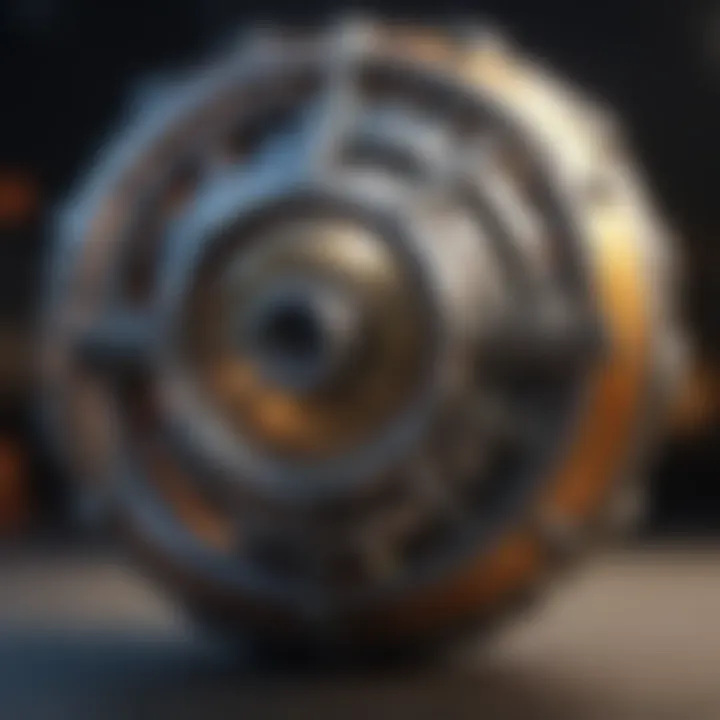
Together, these primary components create a unique material that can withstand harsh environments, hence its extensive use in demanding applications. The specific percentages can vary depending on the manufacturer, but this standard composition is widely accepted.
Proprietary Additives
In addition to its primary elements, Ti6Al4V may incorporate proprietary additives to improve its properties further. These additives are often tailored to meet the requirements of specific applications:
- Iron: Sometimes included to enhance toughness and yield strength.
- Carbon: Can be added in minor quantities to increase hardness but must be controlled to avoid embrittlement.
- Oxygen: Present in trace amounts can significantly affect strength; while it can improve strength, higher levels can lead to brittleness.
The use of proprietary additives reflects the ongoing research and development in materials science, where engineers aim to optimize Ti6Al4V for particular applications.
"Understanding the chemical composition of Ti6Al4V is key to unlocking its full potential in high-performance environments."
These elements and additives indeed extend the functionality of Ti6Al4V, making it a versatile choice across various industries. As research in alloy development progresses, the exploration of new elements and combinations continues to pave the way for even more advanced applications.
Mechanical Properties
The mechanical properties of Ti6Al4V alloy are critical for its applications in various industries, particularly aerospace and biomedical sectors. This alloy is renowned for its unique balance between strength, durability, and lightweight characteristics. Understanding its mechanical properties helps in evaluating its performance in demanding environments.
Tensile Strength
Tensile strength is a measure of how much force a material can withstand while being pulled or stretched before breaking. Ti6Al4V demonstrates remarkable tensile strength, typically ranging from 830 to 900 megapascals. This high tensile strength allows it to be used in applications where resistance to deformation is crucial. The combination of titanium and the alloying elements, such as aluminum and vanadium, provides this strength. This property supports the deployment of Ti6Al4V in aircraft components as well as orthopedic implants, where reliability under load is essential.
Fatigue Resistance
Fatigue resistance refers to a material's ability to resist failure under repeated loading and unloading cycles. Ti6Al4V has excellent fatigue resistance, making it suitable for high-stress applications. Tests show that components made from this alloy can endure many cycles of loading without succumbing to fatigue failure. This is particularly important in the aerospace sector, where components are subject to varying loads during flight. Engineers favor Ti6Al4V when designing parts that require longevity and fail-safe operation. Its resilience against fatigue can significantly reduce maintenance costs and enhance safety.
Corrosion Resistance
Corrosion resistance is another significant mechanical property of Ti6Al4V. Titanium naturally forms a protective oxide layer when exposed to air, offering excellent resistance to corrosive environments. This makes Ti6Al4V particularly useful in marine applications and chemical processing industries. The alloy's resistance to pitting, crevice corrosion, and stress-corrosion cracking allows it to maintain structural integrity even in hostile conditions. This longevity in service can lead to lower replacement costs and overall higher performance in projects where material degradation is a concern.
"The mechanical properties of Ti6Al4V are essential in ensuring the reliability and efficiency of critical components in high-performance applications."
Understanding these mechanical properties of Ti6Al4V alloy allows for informed decisions in its application. From designing aircraft parts to creating medical implants, its unique blend of strength, fatigue resistance, and corrosion defense enhances both safety and performance in various fields.
Manufacturing Techniques
The manufacturing techniques of Ti6Al4V alloy are crucial for its application across various industrial fields. The methods employed greatly influence the alloy's performance characteristics, mechanical properties, and overall usability. Understanding these techniques allows engineers and manufacturers to optimize production processes while enhancing the material's efficacy in real-world applications. This section focuses on three primary manufacturing techniques: casting, additive manufacturing, and machining processes.
Casting Methods
Casting methods play a vital role in producing Ti6Al4V alloy components, especially in large-scale applications. The process generally involves melting the alloy and pouring it into a mold, where it solidifies into the desired shape. Common casting techniques for Ti6Al4V include investment casting and sand casting.
Investment casting is particularly advantageous due to its ability to produce complex geometries with high precision. This method minimizes waste material and allows for tight tolerances, which are essential for aerospace components. On the other hand, sand casting is more economical for larger parts, though it offers less control over surface finish and dimensional accuracy.
Despite its benefits, casting Ti6Al4V can present challenges such as gas porosity and a need for post-processing to correct imperfections. These factors must be carefully managed to maintain the integrity of the alloy in its applications.
Additive Manufacturing
Additive manufacturing, or 3D printing, has become an increasingly popular method for producing Ti6Al4V components. This technique allows for the creation of complex shapes that are challenging or impossible to achieve through traditional manufacturing methods. Techniques like Selective Laser Melting (SLM) and Electron Beam Melting (EBM) are commonly used.
The primary benefit of additive manufacturing is its ability to minimize material waste, enhancing the sustainability of production. Additionally, this method allows for rapid prototyping and customization, which is particularly beneficial in the aerospace and biomedical industries. For instance, customized implants can be created to precisely fit a patient’s anatomy, improving surgical outcomes.
However, additive manufacturing does come with cons, such as longer production times compared to traditional methods and potential issues with part strength due to the layer-by-layer construction. Thus, ongoing research aims to optimize these processes for better quality and reliability.
Machining Processes
Machining processes, including milling and turning, provide another means to shape Ti6Al4V after initial forming or casting. These processes are essential for achieving high precision and smooth surface finishes necessary for components in critical applications.
Managing the machining of Ti6Al4V requires specific considerations, such as tool selection and cutting parameters. It tends to generate high heat and can cause tool wear at an accelerated rate due to the alloy's hardness. Hence, using appropriate cooling methods and tools with advanced coatings can significantly improve efficiency and tool life.
Moreover, machining has the benefit of creating very tight tolerances, which is a key requirement for aerospace and medical implants. The ability to achieve precise dimensions enhances the compatibility and functionality of parts, reinforcing the importance of this technique in the manufacturing spectrum.
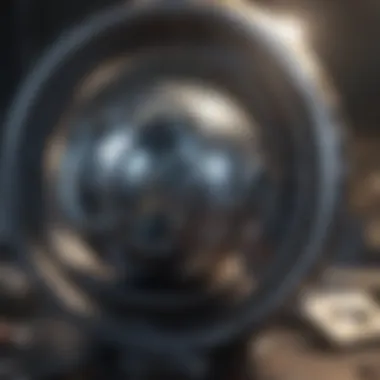
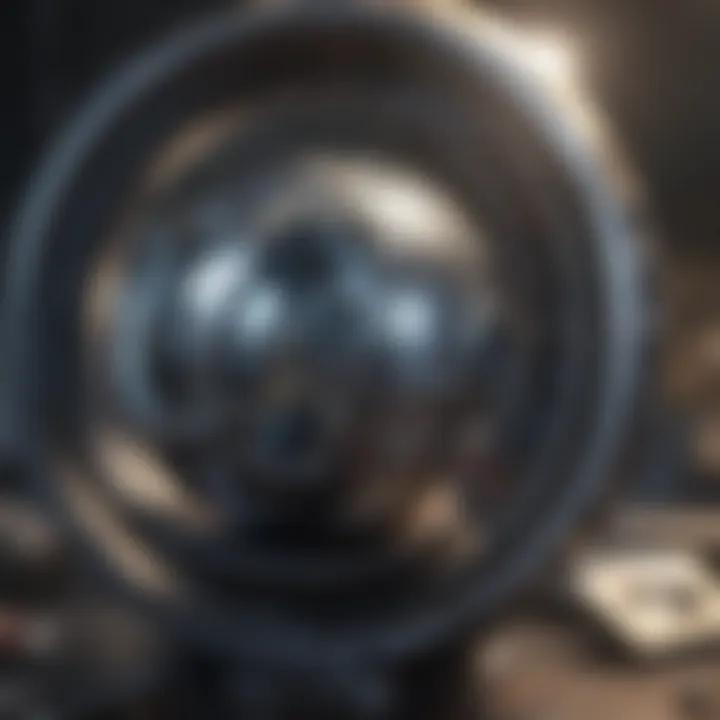
Manufacturing techniques for Ti6Al4V alloy are a blend of tradition and innovation, each method offering unique benefits and challenges depending on the intended application.
In summary, the manufacturing techniques of Ti6Al4V alloy, such as casting, additive manufacturing, and machining processes, each contribute distinct advantages. The selection of an appropriate method hinges on the specific applications, the desired properties of the final product, and the economic considerations of production.
Applications in Aerospace
The aerospace industry significantly relies on materials that combine strength, lightweight properties, and corrosion resistance. Ti6Al4V alloy exemplifies an advanced material that fulfills these requirements. Its unique blend of mechanical properties enhances the performance and reliability of aerospace components, making it an ideal choice for various applications. In the following subsections, we will discuss two primary areas: aircraft components and spacecraft engineering.
Aircraft Components
Aircraft components must endure rigorous stress and strain during operation. Ti6Al4V is particularly favored for structural parts such as wings, landing gear, and engine components. Its high tensile strength maintains durability while minimizing weight, ultimately enhancing fuel efficiency and performance.
In addition to strength, Ti6Al4V displays excellent fatigue resistance. This characteristic is crucial as aircraft undergo repetitive loading cycles. Components made from this alloy demonstrate a longer lifespan, leading to reduced maintenance costs and increased safety for aircraft operators.
Moreover, the corrosion resistance of Ti6Al4V provides added benefits, especially in harsh environmental conditions. The alloy resists degradation from factors like moisture and saltwater, which are common in aviation. This resilience contributes to the longevity of components and reduces the frequency of replacements or repairs.
Spacecraft Engineering
The demands of space exploration and travel pose unique challenges, necessitating materials that can withstand extreme conditions. Ti6Al4V meets these requirements for various spacecraft components. Its lightweight nature eases the burden on launch vehicles, crucial for cost-effective space missions.
In spacecraft, structural components such as frames and supports benefit from Ti6Al4V’s mechanical properties. When subjected to the high stresses of launch and the vacuum of space, the alloy maintains its integrity, ensuring safety and performance during missions.
Additionally, Ti6Al4V is finding usage in components like propulsion systems and heat shields. The alloy's resistance to high temperatures and thermal fatigue makes it suitable for environments where traditional materials might fail. This capability is vital for sustaining health and safety during space travel.
"Ti6Al4V's exceptional performance characteristics make it indispensable in the advancement of aerospace technologies, pushing the boundaries of both aircraft and spacecraft design."
Biomedical Applications
The significance of Ti6Al4V alloy in biomedical applications stems from its unique properties that cater specifically to medical needs. This alloy's strength-to-weight ratio, biocompatibility, and corrosion resistance make it a prime choice for various medical implementations. As the field of biomedical engineering evolves, Ti6Al4V continues to advance, influencing outcomes in surgery and patient recovery.
Implants and Prosthetics
Ti6Al4V plays a critical role in the design and manufacture of implants and prosthetics. The importance of this alloy lies in its ability to integrate well with human tissue. As compared to alternative materials like stainless steel or cobalt-chromium alloys, Ti6Al4V is less likely to provoke adverse biological reactions. This property is essential for long-term acceptance in the body.
- Durability: The alloy has excellent fatigue resistance, which is vital for load-bearing applications such as hip and knee implants.
- Bone In-growth: Ti6Al4V has a favorable surface roughness that promotes osteointegration, enabling bone to grow directly onto the implant, ensuring greater stability.
- Customization: The ease of fabrication allows for customization in shape and size to ensure proper fit for individual patients, enhancing comfort and functionality.
In recent years, the advancements in manufacturing techniques, especially in 3D printing, have opened new avenues for creating patient-specific implants using Ti6Al4V. This not only improves the success rates of procedures but also reduces the time needed for rehabilitation.
Surgical Instruments
In surgical settings, Ti6Al4V is utilized in various instruments due to its favorable mechanical properties. The strength of Ti6Al4V makes it suitable for tools designed to withstand the rigorous demands of surgical environments. This includes scalpels, forceps, and other precision instruments.
- Corrosion Resistance: The alloy’s resistance to corrosion ensures that surgical instruments remain sterile and durable over extended use, a critical consideration in operating rooms.
- Lightweight Design: The low density of Ti6Al4V reduces surgeon fatigue, facilitating greater precision during surgical procedures.
- Non-Magnetic Properties: This feature is particularly beneficial for electromagnetically sensitive environments, ensuring safety in various medical imaging contexts.
In summary, the contribution of Ti6Al4V alloy to biomedical applications is profound and multifaceted. Its properties allow for enhanced healing and improved surgical outcomes, making it an indispensable material in modern medicine. The ongoing research will further solidify its role, addressing emerging challenges in healthcare and technology.
Research Trends
The field of material science continually evolves, driven by advances in technology and a better understanding of materials at the atomic level. Research trends focused on Ti6Al4V alloy are vital in addressing its limitations and enhancing its applications across various industries. These trends offer insight into emerging methodologies and technologies, which can potentially revolutionize the usage and performance of this alloy. The implications of ongoing research are profound, affecting not just the alloy itself but also the industries it serves.
Innovations in Alloying
Alloying innovations play a central role in improving the properties of Ti6Al4V. The focus has shifted to optimizing the balance of titanium, aluminum, and vanadium, while introducing new elements that can enhance specific characteristics. Research examines how different alloying elements interact at the microstructural level. By exploring these interactions, scientists aim to create Ti6Al4V variants with superior performance metrics.
Recent studies suggest adding elements like tantalum or niobium can improve mechanical properties and biocompatibility. This is particularly crucial in fields such as biomedicine, where the success of implants often depends on their ability to integrate with human tissue without causing adverse reactions. Such a focus could drive the development of specialized alloys tailored to unique application demands.
Nanotechnology in Ti6Al4V
Nanotechnology is another forefront of research, introducing new possibilities for Ti6Al4V. It involves manipulating materials on a molecular scale to develop enhanced properties. Nanostructured Ti6Al4V can exhibit improved strength, ductility, and even antimicrobial properties. Such advancements hold tremendous potential, particularly in the biomedical sector where implant longevity and integration are critical.
Research initiatives have shown that processing Ti6Al4V at the nanoscale can lead to a finer microstructure, which significantly enhances mechanical properties. For example, the incorporation of carbon nanotubes within the alloy matrix has been shown to improve not just strength but also flexibility. The attraction of nanotechnology lies in its ability to bridge gaps in traditional manufacturing methods, potentially leading to the next generation of Ti6Al4V products.
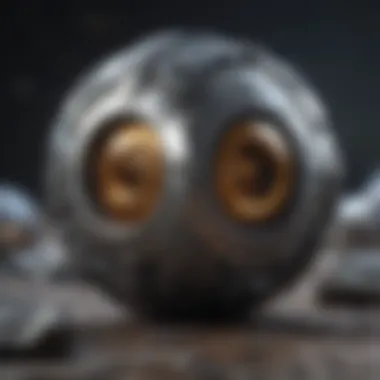
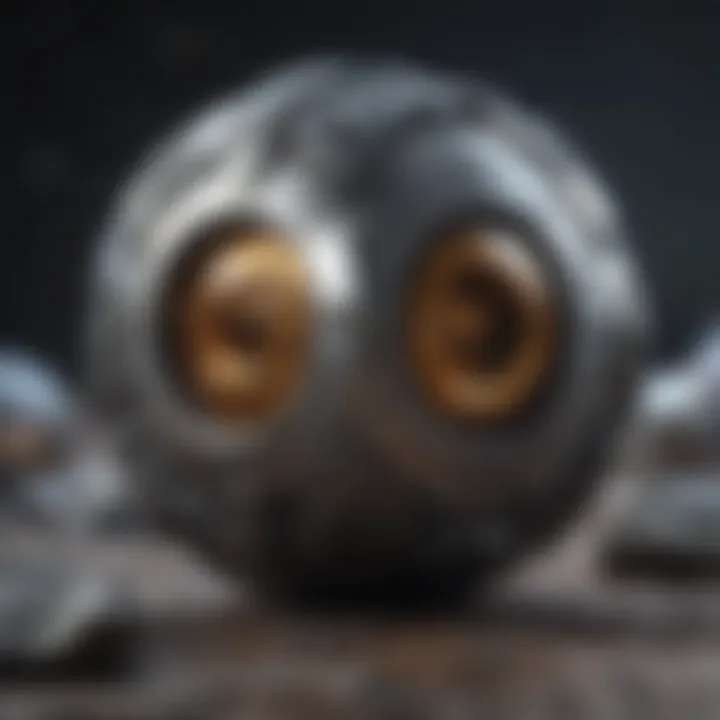
"Exploring nanotechnology applications in Ti6Al4V may redefine standards of performance in aerospace and biomedical industries, unlocking opportunities previously thought unattainable."
In summary, keeping abreast of research trends in alloying and nanotechnology enables a comprehensive understanding of Ti6Al4V's evolution. Such knowledge is instrumental for professionals and researchers to recognize openings for innovation and improvement in various fields.
Environmental Impact
Understanding the environmental impact of Ti6Al4V alloy is crucial for modern material science. The alloy's benefits in various applications often come with significant environmental considerations. As the world increasingly focuses on sustainability, the role of materials like Ti6Al4V must be evaluated not only for their performance but also for their ecological footprint. This discussion highlights sustainability factors and recycling challenges, both of which are vital for responsible usage and production.
Sustainability Considerations
Sustainability is a key element when discussing any material's impact on the environment. Ti6Al4V alloy is favored in industries like aerospace and biomedical due to its durability, lightweight properties, and high corrosion resistance. These characteristics can lead to more efficient operations, resulting in lower energy costs and emissions over a product's life cycle. Additionally, using titanium alloys can facilitate designs that reduce overall material consumption, thus minimizing waste.
Furthermore, the extraction and processing of titanium need scrutiny. The process often involves the mining of titanium ores, which can contribute to habitat destruction and resource depletion. Thus, leveraging sustainable practices in mining and production is essential. For instance, companies are encouraged to adopt more eco-friendly methods that reduce water and energy consumption during alloy processing.
Recycling Challenges
The recycling of Ti6Al4V presents unique challenges that must be addressed to maximize environmental benefits. Although titanium is recyclable, the process can be complicated due to its alloying elements. The presence of aluminum and vanadium in Ti6Al4V complicates recycling and can affect the quality of recycled materials.
- Separation issues: Different alloys may require specific recycling processes. When mixed, the properties of the recycled titanium may not meet industry standards.
- Economic factors: Recycling processes can be costly. The expense of segregating and purifying used materials often outweighs the benefits, leading to less recycling activity.
However, as the industry acknowledges these obstacles, research is ongoing into more efficient recycling technologies. Solutions may include improved separation techniques and adapting existing processing routes to handle mixed alloys more effectively.
"The progress in recycling technology for titanium alloys holds promise but requires significant investment and innovation."
Future Prospects of Ti6Al4V Alloy
The Ti6Al4V alloy, with its remarkable properties, holds great potential for various industries in the future. Its significance in areas such as aerospace and biomedical engineering cannot be overstated. As we explore the prospects of Ti6Al4V, we will consider emerging technologies and current market trends shaping its development. This examination leads to a greater understanding of new opportunities and challenges for this versatile material.
Emerging Technologies
Emerging technologies are crucial in driving innovation for Ti6Al4V alloy. As techniques in material science advance, the alloy's applications expand. New methods in additive manufacturing significantly enhance production efficiency and material optimization. For instance, powder bed fusion technology allows for detailed customization of component structures, directly influencing the mechanical performance of the alloy.
Additive manufacturing also enables the creation of complex geometries that are not possible with traditional methods. This capability is particularly beneficial in industries like aerospace, where weight reduction is critical. Therefore, incorporating Ti6Al4V into these advanced manufacturing processes is essential for achieving lightweight and high-strength components.
Another interesting area is the research into new alloying elements that can enhance the properties of Ti6Al4V. Innovations in nanotechnology are paving the way for the development of novel coatings and treatments that improve corrosion resistance and biocompatibility, further broadening the application scope.
Market Trends
Understanding market trends is vital for any alloy's future, and Ti6Al4V is no exception. The demand for this material has seen steady growth, particularly in aerospace and medical sectors. Reports indicate a continuous rise in investment in aerospace projects, which correlates with an increased need for high-performance alloys. Furthermore, the ongoing expansion of the global healthcare industry creates demand for biomedical applications, such as implants and surgical instruments made from Ti6Al4V.
Several factors affect market trends:
- Technological Advancement: Continuous improvements in manufacturing methods, such as advanced welding techniques, enhance the applicability of Ti6Al4V in diverse fields.
- Sustainability Goals: The move towards sustainable practices drives the need for recyclability in materials, making Ti6Al4V's inherent recyclability an attractive factor for manufacturers.
- Investment in Research: Governments and private sectors are increasingly funding research into new applications of Ti6Al4V, ensuring its relevance in future technologies.
The trajectory of Ti6Al4V alloy reflects broader trends in material science, highlighting its adaptability to market needs and technological advancements.
In summary, the future prospects of Ti6Al4V alloy are bright, with emerging technologies paving the way for new applications and ongoing market growth. Keeping abreast of these developments will be essential for anyone involved in the fields of aviation, medical technology, or material science. The capacity of Ti6Al4V to evolve with technological trends signifies its potential to remain at the forefront of innovation.
The End
The conclusion section serves as a critical component of this article, encapsulating the extensive examination of Ti6Al4V alloy. This alloy, with its unique properties and diverse applications, stands as a testament to modern material science. Understanding Ti6Al4V is not merely an academic exercise but a necessity for ongoing innovation across multiple industries. Its mechanical strength, lightweight nature, and resistance to corrosion highlight its importance in both aerospace and biomedical applications.
Several key elements emerge from the discussion:
- Significant Impact: Ti6Al4V plays a pivotal role in the manufacture of essential components in aerospace and medical fields. These sectors heavily depend on materials that can withstand extreme conditions and provide longevity.
- Research and Development: There is ongoing research geared towards enhancing the properties of Ti6Al4V through various innovative techniques. This could lead to breakthroughs in performance and new applications.
- Sustainability Considerations: The article addressed the environmental implications of Ti6Al4V production and its recycling challenges. As industries strive for more sustainable practices, understanding these impacts is crucial.
In summarizing the importance of Ti6Al4V, it becomes clear that this alloy is not simply a material; it is a foundation for future advancements in technology and engineering. The insights provided within this article pave the way for further exploration and understanding.
Key Takeaways
- Versatile Applications: Ti6Al4V is used in various sectors, notably aerospace and biomedicine, thanks to its unique properties.
- Ongoing Innovations: Continuous research is pushing the boundaries of what Ti6Al4V can achieve, integrating nanotechnology and new alloying methods.
- Environmental Awareness: Acknowledging the environmental impact of Ti6Al4V production prepares industries for better practices in sustainability and recycling.
Implications for Future Research
Future research into Ti6Al4V alloy holds substantial promise for advancing both material science and engineering. Several avenues warrant further exploration:
- Enhancing Material Properties: Ongoing studies to improve strength-to-weight ratios could lead to more efficient designs in aerospace engineering.
- Applications in Emerging Fields: As technology evolves, identifying new uses for Ti6Al4V in fields like energy storage and nanotechnology will be vital.
- Sustainability Innovations: Research focused on improving recycling methods and reducing the environmental footprint of Ti6Al4V production will contribute to a more sustainable approach within the industry.