Understanding the Lithium-Ion Battery Manufacturing Process
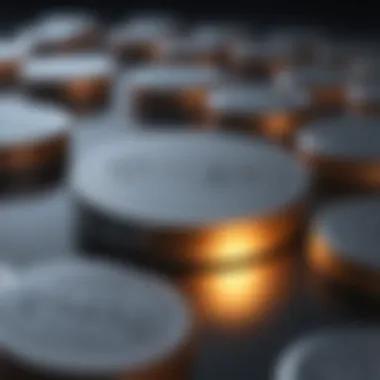
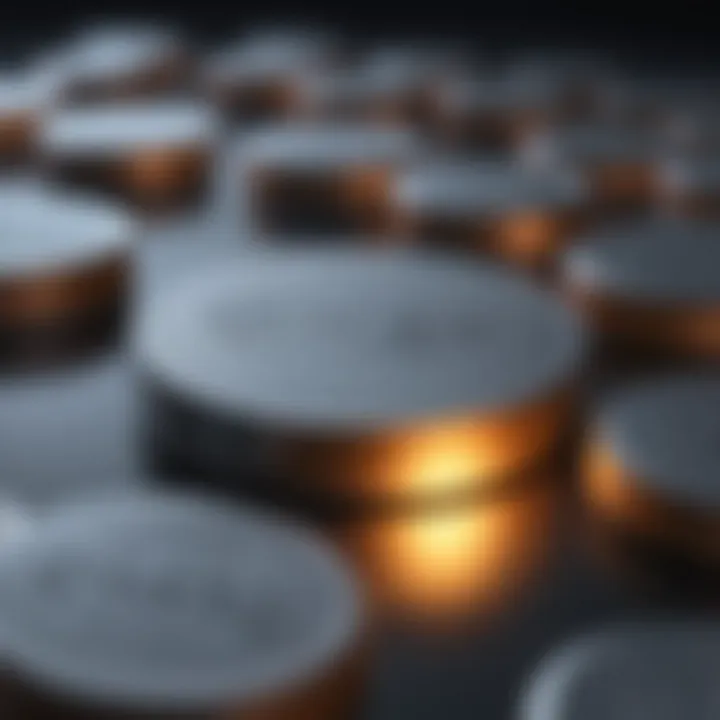
Intro
Creating a lithium-ion battery is like piecing together a complex puzzle where every part plays a crucial role in achieving the final goal. These batteries, which power everything from smartphones to electric vehicles, rely on a carefully orchestrated blend of chemistry, engineering, and quality control. In this section, we aim to peel back the layers of this intricate manufacturing process, shedding light on what makes lithium-ion batteries a backbone of modern energy storage.
Unlike the batteries of yore, which often came with many limitations, lithium-ion batteries are celebrated for their high energy density and longevity. However, the journey to their creation is not without its challenges and subtleties. Each step—from selecting the right materials to final assembly—is pivotal and demands meticulous precision.
This exploration offers valuable insights for students, researchers, and industry experts alike, focusing not just on the technicalities of production but also on the environmental implications associated with battery manufacturing. As we delve into this subject, we hope to instill a profound understanding of the battery-making process and its relevance in today’s green energy landscape.
Research Highlights
Key Findings
Lithium-ion batteries are primarily composed of four essential elements:
- Anode: Typically made up of graphite, this is where the lithium ions are stored during charging.
- Cathode: Often made from lithium metal oxides, this component is responsible for releasing lithium ions during discharging.
- Electrolyte: The medium that facilitates the ion movement between anode and cathode. Commonly, this is a lithium salt in an organic solvent.
- Separator: A critical component that keeps the anode and cathode apart while allowing ions to pass.
Understanding these components is essential, as they directly influence the battery's performance and safety.
Implications and Applications
Lithium-ion batteries are not just for everyday equipment; they have implications across various sectors:
- Renewable Energy Storage: They play a pivotal role in storing energy generated from renewable sources like solar and wind.
- Electric Vehicles: The automotive industry heavily relies on them for propulsion, driving the shift toward sustainable transportation.
- Consumer Electronics: From laptops to tablets, they have revolutionized the portable electronics landscape.
"Investing in battery technology today paves the way for a more sustainable future tomorrow."
Methodology Overview
Research Design
The research design focuses on a systematic approach to lithium-ion battery production. It includes understanding materials' selection, chemical properties, and environmental impacts. Experts often employ modeling to predict battery performance based on varied parameters.
Experimental Procedures
The manufacturing process involves several critical stages:
- Material Preparation: Sourcing high-purity materials to minimize contamination and ensure optimal performance.
- Electrode Production: Involves coating, drying, and pressing procedures that require precise temperature and humidity control.
- Cell Assembly: Cells are constructed in a clean room to avoid particulates that could compromise performance.
- Formation and Testing: Initial charging and discharging cycles are performed to stabilize the cell and assess its efficiency under varying conditions.
By disassembling each of these steps, one gains a more profound appreciation for the cutting-edge technology entwined in everyday devices.
Preface to Lithium-Ion Batteries
Lithium-ion batteries have become a cornerstone of modern technology, playing a critical role in our daily lives. From the smartphones we rely on to energy storage solutions for renewable sources, their impact is ubiquitous. Understanding the nuances of how these batteries are made offers insights into the science and innovation behind them. In this section, we will explore the definition and significance of lithium-ion batteries, alongside their various applications.
Definition and Importance
A lithium-ion battery is a type of rechargeable battery that uses lithium ions as the primary charge carrier. This means that during the battery's operation, lithium ions move from the anode to the cathode through an electrolyte, and then back again when charging. The efficiency of this process is what makes lithium-ion technology highly valuable in powering electronic devices and electric vehicles.
The importance of lithium-ion batteries extends beyond just their function; they are crucial for reducing reliance on fossil fuels. As the world shifts towards more sustainable energy solutions, these batteries provide a vital link in enabling cleaner alternatives. Their role in the advancement of portable electronics has revolutionized the way we communicate, work, and entertain ourselves. Essentially, lithium-ion batteries represent a significant stride towards a more energy-efficient future.
Applications in Daily Life
Lithium-ion batteries are not just confined to high-tech gadgets; they permeate various aspects of our lives. Examples include:
- Consumer Electronics: Devices like smartphones, laptops, and tablets utilize lithium-ion batteries to offer long-lasting power and quick recharge times.
- Electric Vehicles (EVs): The automotive industry has increasingly turned to lithium-ion technology for electric cars. They provide a practical solution for extending the range and efficiency of these vehicles, making them ever more appealing to consumers.
- Renewable Energy Storage: As society moves towards harnessing solar and wind energy, lithium-ion batteries are integral in storing this energy for later use. They help stabilize the grid by balancing supply and demand, ensuring that energy generation aligns with consumption patterns.
- Healthcare Devices: In medical equipment, reliability is key. Lithium-ion batteries are often used in devices like portable ventilators and insulin pumps, offering performance consistency where it is most crucial.
"Lithium-ion batteries not only power our devices but they also energize our future by promoting greener alternatives."
In summary, the significance of lithium-ion batteries cannot be overstated. They enable modern conveniences and foster advancements toward a more sustainable world. By grasping their definition and diverse applications, we gain a better understanding of why the manufacturing process of these batteries is a subject worth delving into.
Key Components of Lithium-Ion Batteries
Understanding the key components of lithium-ion batteries is essential, as these elements determine not only the performance but also the longevity and safety of the batteries we rely on today. The interplay of materials and their specific roles culminates in the efficient storage and release of electrical energy, powering our devices from smartphones to electric vehicles.
Electrolyte
The electrolyte in a lithium-ion battery is the crucial medium that facilitates the movement of lithium ions between the anode and cathode. Typically, it is a lithium salt dissolved in organic solvents. This combination allows for effective ionic transfer while maintaining good electrical insulation between the electrodes, preventing short circuits.
"The quality of the electrolyte often dictates the battery's overall capacity, efficiency, and safety."
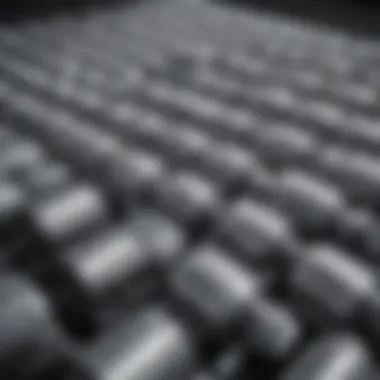
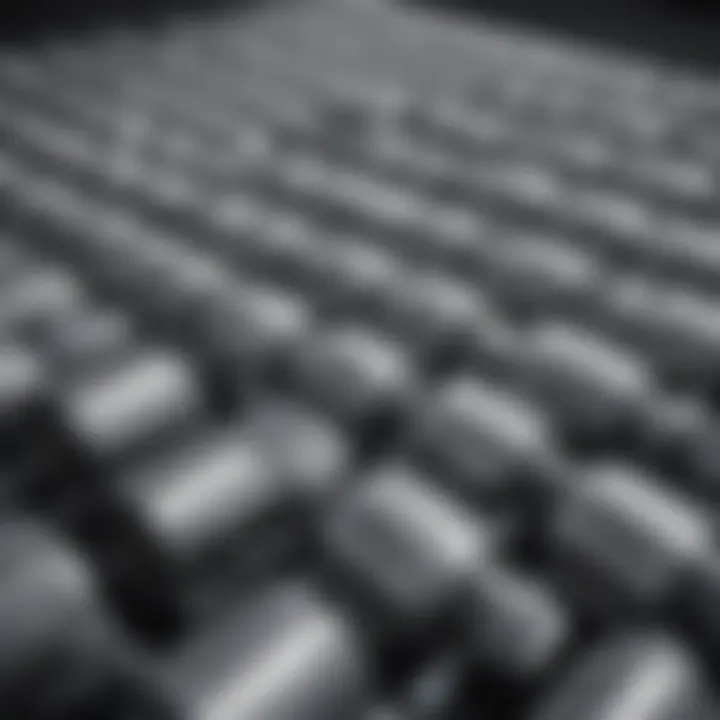
Choosing an appropriate electrolyte is not just a tick on a checklist; it profoundly influences the battery's thermal stability. Electrode materials react with the electrolyte, potentially leading to hazardous situations if the right formula isn't employed. Innovations are continuously sought in this area to enhance conductivity and stability, lessening the risks of overheating or fire.
Anode Materials
Anode materials serve as the entry point for lithium ions during the charging process. Graphite has been the go-to material for years due to its excellent ability to intercalate lithium ions, but it’s not the only player on the field. Silicon, for one, is emerging as a strong contender because of its high capacity for lithium, potentially increasing the energy density of the battery significantly.
However, silicon also has its drawbacks. The expansion during charging can fracture the battery structure, leading to reduced performance over time. Research is focused on using silicon composites or silicon-graphene hybrids to harness the advantages while mitigating the downsides. Striking a balance here is critical; choosing the right anode material can be the difference between a reliable device and a fleeting battery life.
Cathode Materials
Cathode materials are equally important as they hold the key to the battery's voltage and overall capacity. Lithium cobalt oxide has historically been a favorite among manufacturers for its energy density, but its inherent instability under high temperatures raises concerns. This issue has paved the way for alternatives such as lithium iron phosphate and lithium manganese oxide. Each material offers unique benefits and weaknesses, impacting everything from weight to thermal stability, and ultimately user safety.
One might wonder how these materials can influence everyday usage. The choice of cathode material ultimately decides how long you can listen to your music, play games, or drive your electric car before needing to recharge.
In summary, the components of a lithium-ion battery are not merely parts; they're the lifeblood of contemporary energy solutions. Understanding these materials allows engineers and researchers to innovate and enhance battery technology, paving the way for a future where energy storage is more efficient, safer, and longer-lasting.
Chemical Principles Governing Battery Function
Understanding the chemical principles behind lithium-ion batteries is crucial for grasping how these powerful energy sources operate. This section highlights the significance of the fundamental concepts that dictate battery functionality, specifically focusing on how lithium ions move during charge and discharge cycles, as well as the mechanisms that govern these processes.
Lithium-ion Movement
At the heart of a lithium-ion battery’s operation lies the movement of lithium ions. During the charging phase, lithium ions are released from the cathode, traversing through the electrolyte to reach the anode. This movement is driven by an external power source, which creates an electric field that facilitates this ion transfer. Once they reach the anode, lithium ions intercalate into its layered structure, forming a chemical bond that stores energy.
Conversely, when the battery discharges, these ions return from the anode to the cathode through the electrolyte. This back-and-forth shift not only illustrates the dynamic nature of ion movement but also underscores the efficiency of lithium-ion batteries in storing and releasing energy. The speed and ease of ion transport significantly influence the battery's charging and discharging rates, thereby impacting overall performance. For example, a higher ionic conductivity in the electrolyte can lead to shorter charging times, which is a sought-after quality in today’s fast-paced tech environment.
"The efficiency of lithium-ion batteries lies in the seamless movement of lithium ions, making it imperative to explore the factors that enhance this conductivity."
Charge and Discharge Mechanisms
Delving deeper, let's explore how chemical reactions are crucial during the charge and discharge processes. When charging, the external power source not only drives the ions from cathode to anode but also instigates a series of redox reactions. Electrons are pulled away from the cathode, generating an oxidation reaction, while a reduction reaction occurs at the anode as the lithium ions combine with the electrons, thereby forming lithium metal.
During discharge, the reverse takes place. Energy is released as lithium ions move back to the cathode, contributing to the generation of electric current. The chemical reactions involved are not just simple exchanges; they're critical for determining battery lifespan and performance.
Different cathode and anode materials can lead to variations in chemical behavior, altering energy density and cycle stability. Therefore, understanding these mechanisms provides valuable insight into battery design, facilitating enhancements that benefit applications across various industries.
To sum up, the interplay of lithium-ion movement and the charge-discharge mechanisms forms the backbone of lithium-ion battery functionality. Recognizing these chemical principles is essential for advancements in technology and paving the way for the next generation of energy storage solutions.
Materials Sourcing and Its Significance
Materials sourcing plays a pivotal role in the production of lithium-ion batteries. The significance of this process extends beyond merely gathering ingredients; it encompasses the entire spectrum of supply chain management, ensuring that every component is functional, sustainable, and conducive to battery performance. As the demand for lithium-ion batteries surges, primarily driven by the electric vehicle market and renewable energy storage solutions, the importance of responsible sourcing has never been more pronounced. This is where the careful selection and evaluation of raw materials come into play, impacting not only the efficiency and longevity of the batteries but also addressing broader environmental concerns.
Extraction of Raw Materials
The extraction of raw materials is the first step and arguably one of the most critical phases in the lithium-ion battery manufacturing process. Lithium, cobalt, nickel, and graphite are the cornerstones of these energy storage systems. These materials are not easily obtainable, and their retrieval can involve intricate and environmentally taxing mining operations.
- Lithium is typically harvested from brine pools or mined from hard rock sources. The former method involves pumping brine to the surface and allowing it to evaporate, a process which can take months.
- Cobalt, often sourced from the Democratic Republic of Congo, presents significant ethical concerns due to the labor practices involved in its mining. Addressing these issues is essential for manufacturers looking to meet ethical sourcing standards.
- Nickel can be derived from laterite or sulfide ores, and the extraction method can dramatically influence the carbon footprint of the battery, affecting sustainability.
- Graphite, used as the anode material, can be obtained through natural or synthetic processes, each having its own implications for battery performance and environmental impact.
The extraction methods not only impact the quality and availability of these materials but also contribute to the overall environmental footprint of battery production. An increasing number of companies are now seeking innovative solutions like recycling and utilizing less harmful extraction techniques to minimize their ecological impact.
Impact of Material Choice on Performance
The materials chosen during the sourcing phase have a profound influence on the performance of lithium-ion batteries. Each component contributes to the battery's energy density, cycle life, thermal stability, and overall efficiency. Choosing the right materials can mean the difference between a battery that lasts a few years and one that can endure for a decade or more.
- Energy Density: Higher quality materials result in batteries with greater energy density, allowing them to store more power for a given size. For instance, lithium iron phosphate (LiFePO4) offers good thermal stability and long life, thus often being preferred for applications requiring safety.
- Cycle Life: The performance of the battery can also be assessed based on how well it retains charge over numerous cycles of charge and discharge. Cobalt in the cathode improves cycle life but comes at a higher ethical and environmental cost.
- Thermal Stability: Advanced materials are also essential for ensuring that the batteries operate safely and do not overheat. The choice of electrolyte and separator materials plays a key role in maintaining thermal management and, consequently, battery safety.
An inappropriate choice of materials not only compromises the efficiency of a battery but can raise safety concerns, leading to catastrophic failures in extreme cases. Therefore, the strategic selection of materials not only serves performance needs but must also be evaluated against environmental and ethical considerations.
"The sourcing of materials is a delicate dance between performance, sustainability, and ethics. Each choice ripples across the battery's lifecycle, influencing everything from efficiency to environmental impact."
As the battery technology landscape evolves, there is an increasing movement toward circular economies where materials are reused or repurposed, further enhancing the importance of responsible sourcing. A forward-thinking approach to materials sourcing is fundamental for both current innovations and future advancements in lithium-ion battery technology.
The Manufacturing Process
The manufacturing process of lithium-ion batteries is more than just a collection of steps; it’s a dance between precision engineering and innovative chemistry. This segment of our exploration unveils crucial stages wherein the raw materials transform into the powerhouses powering our gadgets and electric vehicles. It's important to bear in mind that even the minutest deviation in this process can affect a battery's performance, lifespan, and safety. Hence, understanding this segment provides invaluable insights into the current and future prospects of battery technology.
Mixing and Coating Processes
In the creation of lithium-ion batteries, mixing and coating processes are pivotal. This is where the various active materials come together in a specific formulation. At this stage, manufacturers mix the active materials—typically lithium compounds—with conductive additives and binders to create a slurry. This slurry is the backbone for both the anode and cathode.
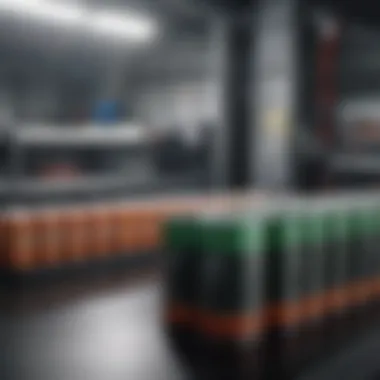
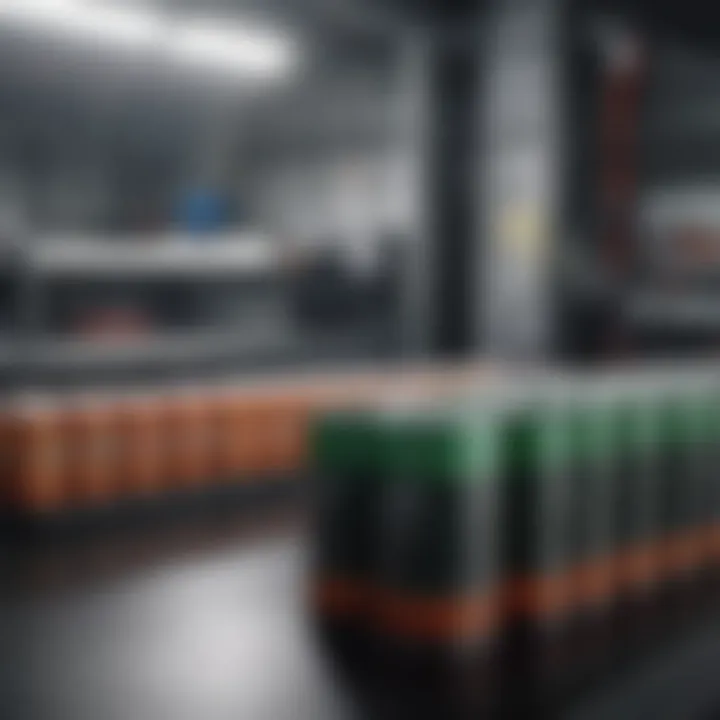
Why is this mixing process vital? The consistency and uniformity in mixing directly influence the performance of the battery. Any lumps or inconsistencies can lead to hot spots; this is where charging can become inefficient or worse, perilous.
Once mixed, the slurry is applied to a substrate, usually copper for the anode and aluminum for the cathode. This application relies on a coating technique that ensures an even layer. An even coat is paramount; otherwise, it could lead to uneven charging and discharging of the battery, which in turn affects its efficiency and longevity.
Here’s a quick overview:
- Material Prep: Active materials, binders, and conductive additives are blended.
- Slurry Creation: Ingredients mixed to form a viscous fluid.
- Coating Layer: Slurry coated onto substrates ensuring uniform thickness.
- Drying Stage: The coated substrates are dried to remove excess solvents.
In this process, the final drying is crucial. This not only solidifies the coated layers but also ensures that the binder effectively holds the materials together. Too much moisture can ruin the electrode, leading to poor performance down the line.
Cell Construction Techniques
After the mixing and coating processes, attention turns to constructing the cells. This is a specialized technique involving multiple layers of the coated substrates, which are combined into a cell structure capable of storing and transmitting energy.
First, the coated anode and cathode films are cut into appropriate sizes. The next step is stacking or winding these layers, which can take different forms. For example:
- Stacking: Layers are placed directly atop each other to form a flat cell.
- Winding: Materials are rolled into a cylindrical shape for more compact cells.
An interesting aspect is that the stacking or rolling techniques can significantly affect the battery pack's overall energy density. By maximizing the surface area between these layers, manufacturers can increase the total voltage and capacity of the finished battery.
Once stacked or rolled, the cells undergo several pressing processes to ensure a seamless and tight assembly. This step eliminates any air pockets that could compromise battery performance, causing localized heating or material fragmentation during operation.
Finally, after achieving the desired structural integrity, the cells are interconnected and placed into battery packs. This is where the true synergy of previous steps becomes apparent. Each layering, adhering, and construction technique is a cog in the well-oiled machine of battery production.
This meticulous construction phase ensures the battery not only meets safety standards but also provides optimal performance.
Assembling Lithium-Ion Cells
Assembling lithium-ion cells is a crucial step in the manufacture of lithium-ion batteries. Without proper assembly, the efficiency, safety, and lifespan of the battery can be compromised. The assembly process integrates various components that have been prepared in earlier stages, emphasizing precision and quality at every turn. It's not just about placing parts together; it’s a meticulous orchestration of techniques that ensures the final product is reliable and performs maximally.
Stacking Procedures
The stacking procedure is a critical part of assembling lithium-ion cells. It involves arranging the layers of the cell’s architecture, which typically comprises the positive electrode, negative electrode, and the separator. The electrodes are coated on thin metal foils, and these must be stacked carefully to maintain integrity and performance.
One common technique is the "jelly roll" method, where the electrodes and separator materials are rolled up into a cylinder, ensuring a compact design that favors efficient ion transfer. Moreover, the alignment of these layers can significantly impact performance. Misalignment could lead to short circuits or reduced efficiency, pushing manufacturers towards advanced automation systems for precision.
It’s also worth noting how the stacking process affects energy density. By ensuring tighter stacking without compromising the material's integrity or thermal properties, the energy storage capacity can be enhanced significantly. Additionally, the choice of stacking procedure could also influence how well the battery can handle rapid charge and discharge cycles, making it a vital element of design.
"The precision in stacking procedures can determine the battery's overall longevity and ability to perform under various conditions."
Sealing Techniques
Once the cells are stacked, sealing them properly becomes the next vital step. This prevents any leakage of electrolytes and protects the internal materials from environmental factors. The sealing process must ensure that no air or moisture can penetrate, as doing so can lead to significant safety hazards, including thermal runaway.
Various techniques are employed in sealing, including laser welding and ultrasonics. Laser welding offershigh precision and is non-intrusive, allowing for minimum physical alteration to the components, while ultrasonics rely on high-frequency sound waves to bond materials together. Both methods have their benefits and challenges, with factors like cost, time, and desired durability being key considerations.
These seals are impactful on not just the immediate safety of the cell, but also its long-term performance. A poorly sealed battery can develop gas pressure within, leading to swelling and possible rupture. Therefore, thorough testing of the sealing is also conducted post-assembly to ensure that it meets safety standards.
Ultimately, assembling lithium-ion cells—through stacking and sealing techniques—plays a pivotal role in the effectiveness of the battery. By maintaining high standards of quality through careful assembly processes, manufacturers can enhance battery safety and performance, paving the way for innovations in energy storage.
Quality Control in Battery Manufacturing
In the realm of lithium-ion battery production, quality control is the linchpin that ensures performance and safety. It’s not just about checking a few boxes; it’s a meticulous process that safeguards the end-user experience and the longevity of the product. Each stage of battery manufacturing is rife with opportunities for error - be it in sourcing raw materials, chemical processing, or cell assembly. Quality control helps catch these errors early, preventing potential failures that can have dire consequences.
The emphasis on quality control also dates back to the rapidly evolving technology and user expectations. As devices continue to demand more power and efficiency, the batteries themselves must keep pace. A comprehensive quality management approach isn’t merely advantageous; it becomes essential. Whether it's maintaining charge capacity or ensuring thermal safety, effective quality control directly impacts the performance metrics and overall reliability of lithium-ion batteries.
Testing Methods for Efficiency
One of the primary pathways to achieving quality in battery production lies in robust testing methods. These techniques focus on assessing efficiency across various stages, from raw material assessment to finished product evaluation. Here are some of the key testing methods:
- Cycle Life Testing: Determining how many charge-discharge cycles a battery can undergo before performance significant degradation. This metric is crucial as it directly correlates to the battery’s durability in practical applications.
- Capacity Testing: This method measures the battery’s ability to hold voltage and deliver current over time. A battery must be able to consistently fulfill its rated capacity to be considered efficient.
- Internal Resistance Testing: Internal resistance can adversely affect charge acceptance and the efficiency of energy delivery. Low resistance is a hallmark of a well-manufactured battery, ensuring maximum performance.
- Thermal Stability Tests: Given that overheating is a major risk for lithium-ion batteries, assessing thermal stability through controlled heat exposure predicts how well the battery can handle extreme conditions.
These methods allow manufacturers to evaluate not only individual cells but also the entire battery systems. In turn, it fosters a culture of transparency and accountability, leading to a product that safely meets the buyer's specific needs.
Safety Standards and Compliance
Battery safety is non-negotiable in manufacturing. Adhering to established standards and regulations is what separates dependable battery manufacturers from those who might cut corners. The consequences of lapses in safety protocols can be catastrophic, leading to fires, explosions, or, worse, endangering lives.
Key standards in lithium-ion battery manufacturing include:
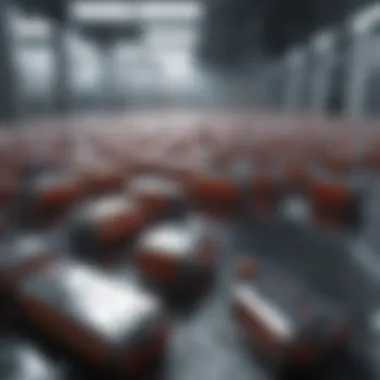
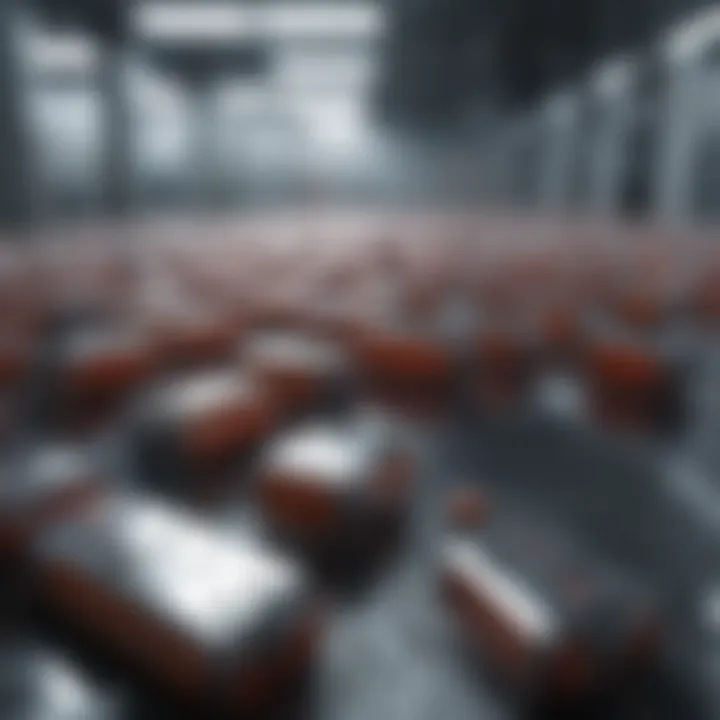
- UL Certification: Underwriters Laboratories provides independent safety testing and proposes safety guidelines. Compliance assures consumers that the batteries meet stringent safety criteria.
- ISO Standards: The International Organization for Standardization outlines quality benchmarks that manufacturers should follow. ISO certification can be a testimony to a company’s commitment to maintaining high-quality practices.
- UN 38.3: This guideline dictates stringent transport safety requirements to ensure batteries can withstand conditions during transport without risk of failure.
Ensuring compliance with codes like these involves regular audits and rigorous documentation. With global supply chains now common, it often requires manufacturers to navigate diverse regulatory landscapes. But at the end of the day, the cost of cutting corners pales in comparison to the potential liabilities faced when safety is compromised.
In summary, ensuring quality control throughout the entire battery manufacturing process is not a merely optional component; it is an obligation. In a world where technology is advancing rapidly, consumers expect nothing less than safe, reliable, and efficient power sources. As the stakes get higher, so too does the need for rigorous quality standards and practices.
Challenges in Battery Production
The journey of creating lithium-ion batteries is marked not only by intricate processes and innovative materials but also by a range of challenges that can impact both efficiency and sustainability. Addressing these challenges is vital for those who are engaged in battery production, whether they are researchers, engineers, or manufacturers. Understanding the elements at play helps to create solutions that don't merely circumvent issues but foster a more resilient and responsible sector.
Environmental Concerns
Lithium-ion batteries do provide a pathway to renewable energy applications, but they also carry hefty environmental baggage. The mining of lithium, cobalt, and nickel has raised alarms due to its potential ecological footprints. For example, lithium extraction in places like the Lithium Triangle of South America can deplete freshwater sources, critically affecting local communities and ecosystems. This is not just a matter of local geography; it speaks to a larger narrative of how technological advancements can lead to detrimental outcomes if overlooked.
Moreover, the disposal of spent batteries poses serious environmental threats. Many current recycling processes are inadequate, leading to improper disposal methods which can leach toxic materials into the soil and water. Implementing more robust recycling protocols and sustainable mining practices is essential to mitigate these concerns. Strategies such as:
- Development of closed-loop recycling systems
- Research into alternative, less harmful materials
- Stronger regulatory frameworks for material extraction
can help pave the way toward minimizing environmental degradation.
"The true cost of a battery isn't just in manufacturing; it’s in how we manage its lifecycle."
Resource Scarcity
As demand for lithium-ion batteries surges—fueled by electric vehicles and renewable energy storage solutions—the scarcity of essential raw materials like lithium and cobalt is becoming more pronounced. Estimates suggest that current extraction rates may not satisfy future needs, especially as markets expand. The heavy reliance on cobalt, primarily sourced from the Democratic Republic of Congo, underscores geopolitical risks that can disrupt supply chains, creating a ripple effect throughout the industry.
It's alarming to think that without adequate measures, the very backbone of modern technology might be at risk. To address this issue, battery manufacturers are exploring alternatives such as:
- Increased use of sodium-ion technologies
- Enhancement of lithium recycling techniques
- Investments in synthetic substitutes
Each of these strategies has its pros and cons, and further research is needed to ascertain their long-term viability. In the face of these challenges, a proactive approach in resource management becomes paramount for ensuring a sustainable future in battery technology.
Future Trends in Lithium-Ion Battery Technology
As we progress deeper into the 21st century, the reliance on lithium-ion batteries escalates alongside our appetite for energy storage solutions. Not only do these batteries power our everyday electronics, but they also play pivotal roles in the expansion of electric vehicles and renewable energy sectors. It’s imperative to stay updated on the latest innovations and production techniques that will shape the future of lithium-ion batteries.
Innovations in Materials
The materials selected for lithium-ion batteries are fundamental to their performance and longevity. Recent research has sparked a flurry of innovations aimed at enhancing energy density, efficiency, and overall battery sustainability. One notable advancement involves the exploration of silicon-based anode materials, which can hold several times more lithium ions than conventional graphite. This shift to silicon could result in batteries that last longer and charge faster, delighting tech enthusiasts and eco-conscious consumers alike.
Another area garnering attention is the development of solid-state electrolytes. Unlike traditional liquid electrolytes, solid variants can minimize risks of leakage and flammability. They hold the promise for increased safety and improved ionic conductivity, ultimately leading to higher performance batteries.
Why does this matter? A fuel-efficient future depends heavily on innovations in materials; they can bring down the cost while extending battery life. Considering the growing demand for energy storage solutions, this is not something to overlook.
"The evolution of materials used in lithium-ion batteries could redefine the landscape of energy technology, enhancing efficiency and sustainability across various applications."
Advancements in Production Techniques
The methods employed to manufacture lithium-ion batteries are also evolving rapidly. Traditionally, battery assembly was a cumbersome process that often left room for human error and increased production costs. However, automated technologies are beginning to take the reins in production lines, ensuring consistency and precision. This streamlining not only boosts manufacturing efficiency but potentially reduces the prices for end consumers.
Moreover, 3D printing technologies are paving a new avenue in battery design. This innovative technique allows for intricate geometries that can optimize space and potentially lead to lighter batteries. More than that, it fosters customization of battery shapes and sizes to fit specific applications or devices, enhancing usability.
To further improve sustainability, recycling processes for lithium-ion batteries are becoming more advanced too. Innovators are finding ways to recover precious materials from spent batteries, minimizing waste and reducing the need for new raw materials.
As techniques like these come to the forefront, we can expect to see not only improvements in production efficiency but also a significant reduction in the environmental impact of battery production.
In summary, keeping an eye on these trends isn't just a good idea; it's crucial. The future of lithium-ion technology is intertwined with both material science innovations and production breakthroughs. Better materials and improved production processes could mean a future that harmonizes with our growing need for power, without putting undue strain on the environment.
Ending
In reflecting upon the intricate tapestry of lithium-ion battery manufacturing, one cannot understate its significance in today’s tech-driven world. These batteries are not merely components; they are lifeblood for an array of devices—from smartphones to electric vehicles. The production journey is filled with multiple hurdles and considerations, each pivotal in shaping the end product's efficiency and durability.
To wrap things up, we’ve journeyed through the key points of the topic:
Recap of Key Points
- Key Components: We delved into essential materials like the electrolyte, anode, and cathode, explaining their unique roles in the battery's operation.
- Chemical Principles: The movement of lithium ions and the mechanisms of charging and discharging were outlined, showcasing their direct influence on energy storage.
- Manufacturing Process: A step-by-step breakdown of mixing, coating, and assembly techniques provided insight into what it takes to create these powerhouses.
- Quality Control: At various stages, rigorous testing methods and safety standards were highlighted, emphasizing how important these checks are to ensure reliable products.
- Challenges: The environmental implications and resource scarcity issues painted a fuller picture of the uphill battles faced in the industry.
- Future Perspectives: By looking at innovations in materials and production, we discerned potential developments that could shape the future landscape of battery technology.
The Importance of Continued Research
The importance of ongoing research in lithium-ion technology cannot be overstated. As the acceleration of technology continues—think smart grids or renewable energy storage—the demand for superior battery performance escalates. Continued exploration can yield breakthroughs that might open doors to achieving greater energy densities, decreasing production costs, or developing more sustainable manufacturing practices.
Ultimately, the marriage of research and development with practical applications ensures that the next generations of lithium-ion batteries are not only more efficient but also environmentally responsible.
"The future of lithium-ion technology hinges not just on making better batteries, but making them in wiser, greener ways."