Navigating the Shift from 3D Printing to CNC Machining
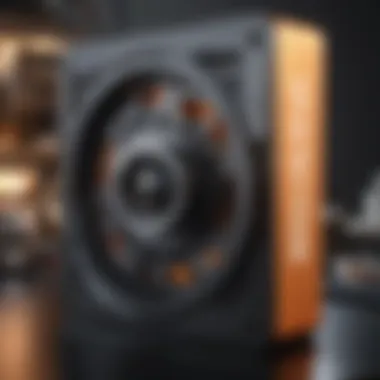
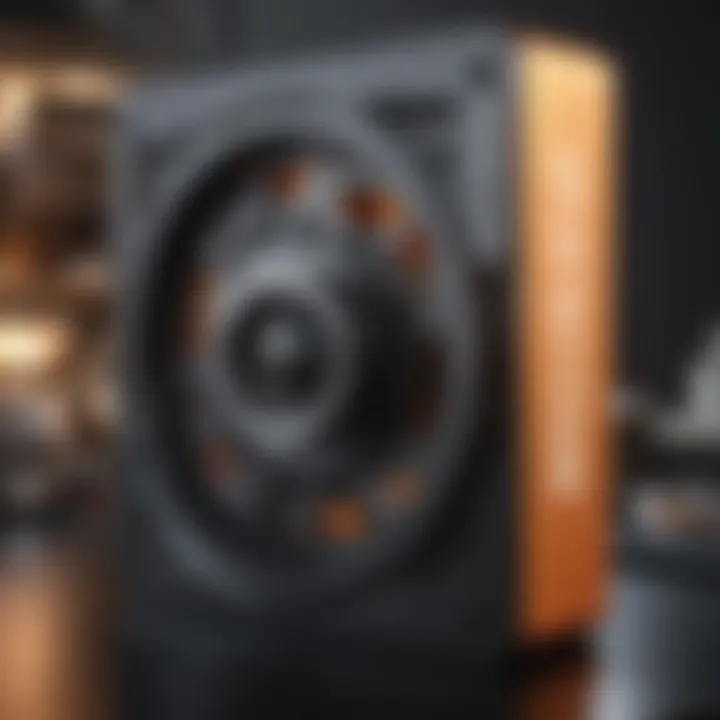
Intro
As industries increasingly seek efficiency and precision, the examination of 3D printing and CNC machining becomes paramount. Each manufacturing process has its own set of characteristics, strengths, and limitations. Understanding these can shape the future of production methodologies.
3D printing, known for its layer-by-layer construction, is ideal for rapid prototyping and intricate designs. In contrast, CNC machining relies on cutting tools to produce objects from solid blocks of material. While both techniques serve critical roles in modern manufacturing, transitioning from one to the other requires a thorough understanding of their fundamental principles and operational techniques.
This article aims to clarify the distinctions and synergies between these two technologies. Professionals in various sectors will find insights into how to harness the potential of both for improved outcomes in production quality and efficiency.
Preface to 3D Printing and CNC Machining
The exploration of 3D printing and CNC machining reveals a significant transition in manufacturing technologies. Each method presents unique advantages, considerations, and applications that reflect the evolving landscape of production. Understanding these technologies is vital for professionals, researchers, and students who aim to stay informed about modern manufacturing processes.
3D printing, also known as additive manufacturing, allows for the creation of objects layer by layer. This process enables complex geometries that are hard to achieve with traditional methods. CNC machining, or computer numerical control machining, involves the removal of material from a solid block to create parts. This subtractive method is known for its precision and ability to work with a range of materials. Both technologies have their place in todayโs manufacturing environment, each serving distinct needs.
As industries continue to innovate, the integration of these technologies becomes increasingly relevant. This article focuses on their definitions, principles, historical backgrounds, and comparative analyses. Understanding the synergy and differences between these methods can enhance decision-making in the manufacturing field.
Definition of 3D Printing
3D printing refers to a group of manufacturing techniques that create three-dimensional objects from digital files. The process involves depositing material in successive layers. It contrasts traditional manufacturing, which typically involves cutting away material from a larger block. 3D printing processes vary widely, from techniques like Fused Deposition Modeling (FDM) to Stereolithography (SLA). Interesting advantages of 3D printing include:
- Design Flexibility: It facilitates complex designs that may be impractical with other methods.
- Reduced Waste: Material is added where needed, leading to less waste during production.
- Rapid Prototyping: It can quickly produce prototypes for testing and validation.
Definition of CNC Machining
CNC machining is a manufacturing process that uses computer-controlled machines to cut and shape materials. It primarily works with metals, plastics, and wood. The process starts with a digital design, which is then translated into machine language that directs the tool movements. Advantages of CNC machining include:
- Precision: CNC machines can achieve high tolerances, making them suitable for intricate designs.
- Scalability: Once programmed, machines can produce large quantities of identical parts efficiently.
- Material Versatility: It can work with various materials including metals, plastics, and composites.
Historical Context of Both Technologies
The origins of 3D printing can be traced back to the 1980s. Charles Hull developed the first stereolithography machine, paving the way for the additive manufacturing industry. Initially used for prototyping, 3D printing has evolved into a process suitable for final product manufacturing in various sectors, including healthcare and aerospace. On the other hand, CNC machining has a more extended history. Its roots reach back to the 1940s and 1950s when pioneers began using punched tape to control machine tools. Over the decades, advancements in computer technology have revolutionized the capabilities of CNC systems. Today, they are ubiquitous in manufacturing, offering increased accuracy and efficiency compared to manual machining.
The historical development of both technologies reflects the ongoing advances in manufacturing methods. As industries evolve, understanding these origins provides insight into current practices and future potential.
Principles of 3D Printing Technology
The principles of 3D printing technology form the foundation of this innovative manufacturing method. Understanding these principles enables users to appreciate the advantages and limitations of additive manufacturing. This section discusses the core processes involved in creating 3D printed objects, with a focus on the prevalent additive manufacturing methods and techniques. These details are crucial for the transition to CNC machining, as they outline how 3D printed models can be adapted for further processing.
Additive Manufacturing Process
The additive manufacturing process represents the core of 3D printing technology. This process involves creating objects layer by layer from a digital model. Unlike traditional subtractive methods, which remove material, additive manufacturing adds material to build the final product. This approach allows for complex geometries and intricate designs that would be difficult or impossible with traditional techniques.
One significant benefit of this process is the reduction of waste. Since material is added where needed, the inefficiencies associated with cutting or machining materials away are minimized. Furthermore, this process enables rapid prototyping, allowing designers and engineers to produce models quickly for testing and iterations.
Types of 3D Printing Techniques
3D printing encompasses a variety of techniques, each with unique capabilities and applications. Understanding the different types is essential for selecting the appropriate method based on specific project needs. Below are some of the most common 3D printing techniques used in the industry.
Fused Deposition Modeling (FDM)
Fused Deposition Modeling (FDM) is one of the most popular and accessible 3D printing technologies. This method works by extruding thermoplastic filament through a heated nozzle, which moves in precise patterns to build layers.
The key characteristic of FDM is its affordability and ease of use, making it a prevalent choice for hobbyists and small businesses. It allows for quick prototyping with many materials, such as PLA and ABS, which are readily available. However, it has some limitations, such as resolution and layer adhesion, which might not meet the standards for certain applications.
Advantages of FDM include:
- Cost-effectiveness
- A large variety of material options
- Simplicity in operation
Disadvantages consist of:
- Limited part strength compared to other methods
- Inconsistency in surface finish
Stereolithography (SLA)
Stereolithography (SLA) utilizes a laser to cure liquid resin into solid layers. This method provides high resolution and is capable of achieving intricate details, making it suitable for applications requiring precision.
A significant feature of SLA is its ability to produce smooth and fine finishes, which is appealing for visual prototypes and intricate designs. However, the process is more complex and can be more expensive than FDM, with the need for specialized equipment and materials.
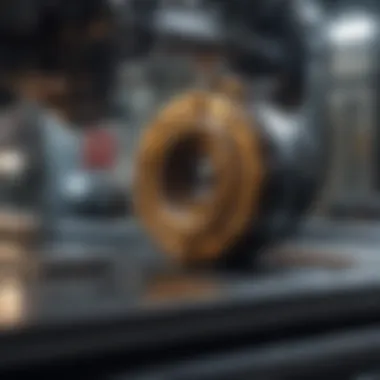
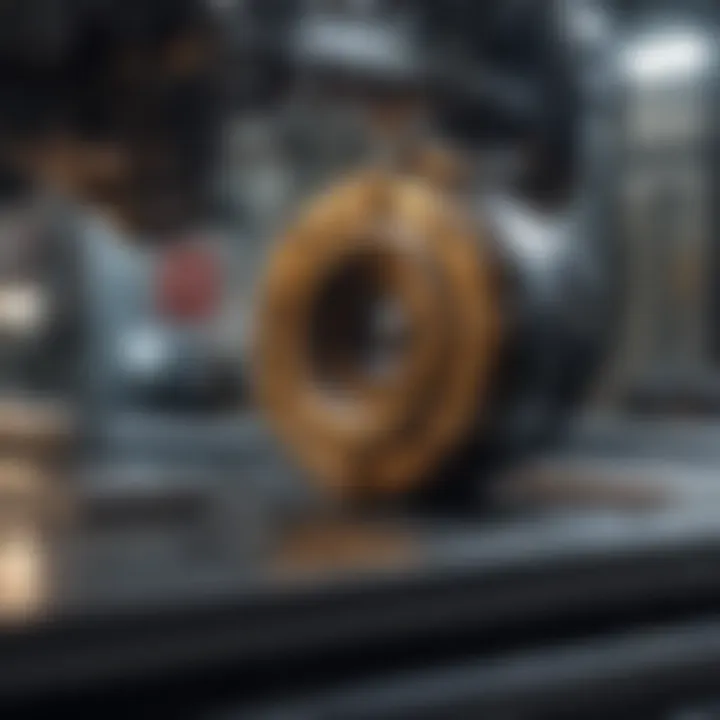
Advantages include:
- High detail and resolution capacity
- Smooth finish suitable for display models
On the downside, SLA has:
- Longer print times
- The need for post-processing to remove excess resin
Selective Laser Sintering (SLS)
Selective Laser Sintering (SLS) is a robust technique that uses a laser to sinter powdered material, typically nylon or other polymers, into solid structures. This method allows for creating functional prototypes and low-volume production runs with excellent mechanical properties.
The defining characteristic of SLS is that it does not require support structures because the powder serves as a support material. This freedom offers design flexibility and reduces material waste. Nevertheless, SLS equipment tends to be more costly and complex, which may deter smaller operations.
The advantages of SLS include:
- High strength and durability of printed parts
- Greater design freedom without the need for supports
However, some downsides are:
- Higher initial investment cost
- Limited material options compared to FDM
Understanding these various 3D printing techniques is vital for making informed decisions in product development and for preparing models for additional processes, such as CNC machining. By knowing the strengths and weaknesses of each technique, professionals can optimize their workflow to leverage the best aspects of both 3D printing and CNC machining.
Principles of CNC Machining Technology
CNC machining stands as a critical component in modern manufacturing. Understanding its principles is necessary for anyone transitioning from 3D printing to CNC machining. This section outlines essential aspects of the technology, discussing its processes, advantages, and significance.
Subtractive Manufacturing Process
The subtractive manufacturing process in CNC machining involves removing material from a solid block to achieve a desired shape. This stands in contrast to 3D printing, where material is added layer by layer. The significance of this process lies in its precision and versatility. It can produce parts with tight tolerances, which is vital in industries like aerospace and medical devices.
Mistakes in the initial model can lead to significant material loss, if not addressed properly. Hence, careful planning and design are imperative. Understanding the dynamics of the subtractive process aids in optimizing manufacturing workflows, leading to more efficient production.
Types of CNC Machining Processes
There are various CNC machining processes, each catering to specific needs. Here are some of the main types:
CNC Milling
CNC milling is a widely-used technique that involves rotating cutting tools to remove material from a stationary workpiece. One key characteristic of CNC milling is its ability to create complex geometries with high accuracy. This process is popular for producing intricate shapes and features.
The unique feature of CNC milling is its multi-axis capability. This allows for machining on different sides of a part without needing to reposition it manually. However, it can be time-consuming for larger parts, and setup costs can be high.
CNC Turning
CNC turning is another significant process that focuses on rotating the workpiece against a fixed cutting tool. This technique primarily produces cylindrical parts. Its key advantage is the efficiency in creating round shapes, such as shafts or tubes.
CNC turning machines can also handle various materials, making them a beneficial choice in production runs requiring different types of blanks. A disadvantage of CNC turning is limited to specific shapes, often necessitating additional processes to achieve complex designs.
CNC Routing
CNC routing is distinct from milling as it primarily targets softer materials like wood, plastics, and softer metals. The key characteristic here is the tool's path optimization, which greatly enhances speed and efficiency. This method is particularly beneficial for large-scale production, such as signs and furniture.
Its unique feature lies in its ability to create large, flat surfaces quickly. However, one disadvantage is the limited precision compared to milling or turning, making it less suitable for intricate details or tight tolerances.
"Understanding the principles of CNC machining allows manufacturers to leverage its capabilities effectively, bridging the gap from 3D printing to more traditional methods."
By grasping these various types of CNC machining processes, a clear picture of how they contribute to the overall goal of precision manufacturing emerges. Each method brings its strengths and weaknesses, facilitating informed decisions during the transition from 3D printing.
Comparative Analysis of 3D Printing and CNC Machining
The comparative analysis of 3D printing and CNC machining is crucial in understanding their roles in modern manufacturing. These two technologies serve distinct purposes, yet they hold potential for synergy in various applications. By analyzing their differences and similarities, one can make informed decisions about which process to adopt depending on the specific manufacturing needs.
Material Utilization and Waste Generation
Material utilization is a significant factor when comparing 3D printing and CNC machining. 3D printing, being an additive manufacturing process, primarily uses only the material necessary for building the part. This limits waste generation considerably. For instance, a part made through Fused Deposition Modeling (FDM) only uses filament that constructs the shape. In contrast, CNC machining is subtractive, which means it starts with a solid block of material. The cutaway parts are the scraps, which could account for significant waste depending on the design and material process.
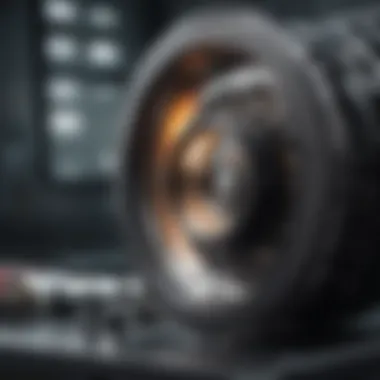
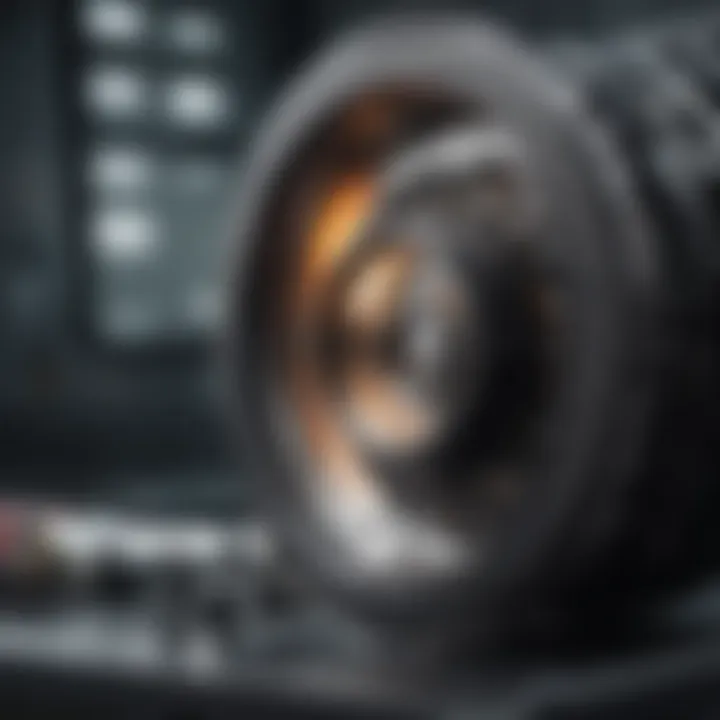
Moreover, the choice of materials varies greatly between the two technologies. 3D printing often utilizes thermoplastics such as PLA and ABS, while CNC machining can work with metals, woods, and plastics. The impact of these material choices extends beyond just waste; it also influences recycling and sustainability efforts. As manufacturers strive for eco-friendliness, the comparative benefits in material usage are essential.
Production Speed and Efficiency
When evaluating production speed and efficiency, both methods display distinct advantages under various circumstances. 3D printing usually excels in prototyping and low-volume production. The ability to quickly modify designs in the digital file and print them out almost instantaneously is a major advantage. Certain processes can produce complex geometries that would be difficult or impossible to achieve with CNC.
CNC machining, however, can dominate in large-scale production due to its ability to maintain tight tolerances and produce uniform parts in higher quantities. For example, once a CNC program is established, it can run continuously, producing consistent parts at a fast rate. This capability is invaluable for companies that require large batches of identical components.
Cost Considerations
Cost is another area where these technologies diverge. 3D printing tends to be more economical for lower production volumes, especially when considering setup costs. The initial investment in a 3D printer can be lower than that for a CNC machine. However, per-unit costs might rise if the production volume is high, due to slower speeds compared to CNC machining.
Conversely, although CNC machining may have higher initial costs associated with setup and machinery, it becomes cost-effective for larger production runs. The automation and efficiency of CNC processes can lower the cost per unit significantly when produced in bulk.
Transitioning from 3D Printing to CNC Machining
The shift from 3D printing to CNC machining is a crucial subject in the context of modern manufacturing. This transition signifies not just a change in technology but also an evolution in production capabilities. Both 3D printing and CNC machining have their unique strengths and weaknesses. As industries continue to develop, understanding this transition becomes increasingly important. It highlights the need for flexibility, precision, and material efficiency.
Professionals involved in manufacturing must often evaluate which technology best suits their needs. Several factors influence the decision to move from one method to another. These include considerations of production volume, material properties, and cost-effectiveness. Knowing the reasons behind such transitions can guide companies in making informed decisions that optimize operations and improve product quality.
Reasons for Transition
There are multiple reasons why a manufacturer might consider moving from 3D printing to CNC machining.
- Precision and Finish: CNC machining generally offers superior precision and surface finish compared to 3D printing. This is particularly critical in applications where tight tolerances are necessary.
- Material Variety: CNC machines can work with a wider range of materials, including metals, plastics, and composites. In contrast, 3D printing is often limited by the types of materials that can be used for printing.
- Production Scale: While 3D printing is excellent for prototypes and small production runs, CNC machining can be more efficient for larger quantities. Transitioning allows businesses to scale up production without compromising quality.
- Cost Efficiency: In certain scenarios, CNC machining can be more cost-effective, particularly for larger orders. Reduced material waste also contributes to overall savings.
Preparing 3D Printed Models for CNC
Prepping a 3D printed model for CNC machining entails several steps to ensure a smooth transition. This process is crucial to achieve the desired output while minimizing errors or adjustments during machining.
- Model Evaluation: Assess the current 3D printed model. Check for any design flaws or weaknesses that might not be noticeable during the early stages of 3D printing.
- Conversion to CAD: 3D printed models often need to be converted to a CAD (Computer-Aided Design) format suitable for CNC machining. This may involve remodeling or modifying the existing design.
- Toolpath Generation: Generate the toolpaths using CNC software, ensuring that the appropriate cutting tools and speeds are selected based on the material.
- Prototyping: Before final production, it might be beneficial to create a small batch or a prototype using CNC machining to test the design and machining parameters.
Challenges in Transitioning
While transitioning has benefits, it also comes with a set of challenges. They must be clearly understood to navigate them effectively.
- Initial Setup Costs: Transitioning to CNC machining may involve significant upfront costs. This includes acquiring the necessary equipment and software.
- Learning Curve: There is often a steep learning curve associated with CNC machining. Staff may require training to operate machinery effectively and safely.
- Material Compatibility: Not all 3D printed materials are suitable for CNC machining. This necessitates careful consideration to ensure that the material can withstand the machining processes.
- Tool Wear: CNC machining tools are subject to wear and may require regular replacement, impacting the overall operational costs.
Understanding the reasons, preparations, and challenges of transitioning from 3D printing to CNC machining is essential for professionals aiming for operational excellence in manufacturing.
Material Considerations for CNC Machining
Understanding materials is critical when transitioning from 3D printing to CNC machining. Each method utilizes different materials, leading to varied mechanical properties, performance characteristics, and final product quality. The choice of material impacts not only the machining process but also the product lifespan and functionality. Thus, fabricating high-quality CNC machined items requires a strategic approach to selecting the right materials.
Common Materials Used in CNC
CNC machining can accommodate a wide array of materials, including:
- Metals: Common materials include aluminum, steel, brass, and titanium. Each metal offers unique attributes, such as strength versus weight. For instance, aluminum is lightweight and resistant to corrosion, making it suitable for many applications.
- Plastics: Materials like acrylic, polycarbonate, and nylon are widely used. They offer versatility and can be both strong and lightweight, suitable for diverse applications.
- Composites: These materials combine multiple materials to produce enhanced properties, such as high strength-to-weight ratios. Carbon fiber and fiberglass are examples often machined to produce aircraft components.
- Wood: CNC machines can also work with wood, allowing for the precise creation of intricate designs, often seen in furniture making.
Each material choice comes with specific machining requirements. For instance, harder materials may require advanced tooling which ultimately affects production speed.
Impact of Material Choice on Product Quality
The selection of material plays a significant role in the quality of the final product. Here are several factors to consider:
- Strength and Durability: Materials like titanium provide superior strength, ideal for applications requiring high durability, such as aerospace components.
- Surface Finish: The type of material affects the finish quality. Metals generally need polishing for aesthetic appeal, while plastics can achieve a satisfactory finish from the machining process alone.
- Dimensional Accuracy: The chosen material can influence how well it tolerates machining operations. Some metals hold tight tolerances, while softer materials might yield more easily, leading to inaccuracies.
- Cost: The price of raw materials can significantly impact project budgets. Metallurgical costs can vary greatly, prompting a careful evaluation of necessary investments.
"Choosing the right material is not just about performance; it can redefine the economics and feasibility of the project."
Ultimately, a thorough understanding of material options can lead to informed decisions, resulting in high-quality, functional products that efficiently meet design specifications.
Practical Applications of 3D Printing and CNC Machining
The practical applications of 3D printing and CNC machining are pivotal in understanding how these technologies are reshaping industries. Their significance extends beyond mere production processes; they enable companies to innovate, reduce costs, and optimize performance. Each technology offers unique advantages that cater to specific needs across various sectors.
Benefits of 3D Printing
3D printing is known for its flexibility and ability to produce complex geometries with relative ease. Industries utilize it to create prototypes, small batch productions, and customized products. One of the compelling aspects is its design freedom, allowing for intricate designs that may not be feasible with traditional methods.
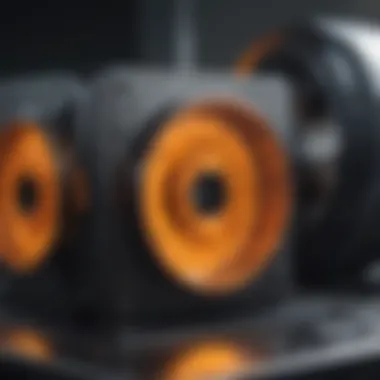

Applications include:
- Medical devices: Tailored implants and prosthetics made from biocompatible materials.
- Aerospace parts: Lightweight components that adhere to strict standards for performance and efficiency.
- Consumer goods: Customized products tailored to individual customer needs, significantly shortening the path from design to market.
Benefits of CNC Machining
CNC machining excels in precision and repeatability. It has been a cornerstone in manufacturing for industries requiring stringent tolerances and consistent quality. The ability to work with a wide range of materials gives CNC machining a broad appeal.
Applications include:
- Automotive components: High-accuracy parts that must withstand rigorous testing and performance requirements.
- Industrial equipment: Durable components with precise dimensions critical for machinery functionality.
- Jewelry making: Detailed and high-quality designs that demand exact specifications.
Both technologies play crucial roles in modern manufacturing, enhancing speed, efficiency, and customization capabilities in production. Moving forward, professionals must keep an eye on the integration of these methods to leverage their strengths effectively.
Industry Use Cases for 3D Printing
3D printing has transformed various industries by allowing rapid prototyping and low-volume production. Some significant case studies highlight its impact:
"The growth of 3D printing is fundamentally altering product development and manufacturing cycles."
- Healthcare: Companies like Stratasys are utilizing 3D printing to create custom surgical models, enabling surgeons to perform complex procedures with better preparation.
- Fashion Industry: Brands such as Adidas employ 3D knitting techniques that enable faster production of bespoke footwear designs, catering to shifting consumer preferences.
- Architecture: Firms like ICON are exploring 3D printing for constructing affordable housing structures quickly and sustainably.
These examples illustrate that 3D printing is not only about creating objects but about enhancing workflows and customer satisfaction.
Industry Use Cases for CNC Machining
CNC machining remains a critical asset in sectors demanding precision and reliability. By examining its use cases, one can grasp its importance deeply:
- Electronics Manufacturing: Companies such as Apple require precise machining for the components that make up electronic devices. The accuracy of CNC machining ensures each part fits perfectly in the complex assembly processes.
- Aerospace Industry: Organizations like Boeing depend on CNC for producing highly specialized components that must adhere to strict safety and performance standards.
- Defense Sector: Firms manufacturing military equipment rely on CNC machining for creating components that require rigorous testing and exact specifications, like those for missiles and vehicles.
CNC machining has proven essential in delivering high-quality products that meet industry standards, reaffirming its place in modern manufacturing landscapes.
In summation, both 3D printing and CNC machining showcase distinct advantages tailored for different needs. Understanding their practical applications helps businesses select the right technology, ensuring they remain competitive and adaptive in an ever-evolving market.
Future Prospects and Innovations
Future prospects and innovations in manufacturing technologies have garnered significant interest due to the evolving needs of industries. This section delves into the advancements that shape the roadmap for 3D printing and CNC machining. These innovations play a critical role in enhancing production methods, making operations more efficient, and responding to the specific demands of the market.
Emerging Technologies in Additive Manufacturing
Additive manufacturing, primarily driven by 3D printing, is undergoing rapid technological changes. Some noteworthy developments include:
- Metal 3D Printing: Traditional 3D printing mainly focused on plastics. Now, technologies like Direct Energy Deposition (DED) and Metal Binder Jetting open new avenues for production in industries like aerospace and automotive. These methods provide strong, lightweight components that are critical for high-performance applications.
- Bioprinting: This niche application involves printing tissues and organs. With progress in biomaterials and ink formulations, it holds potential for medical advancements, aiming to address organ shortages and improve tissue regeneration methodologies.
- Multi-Material Printing: Systems that allow the printing of multiple materials in a single process facilitate the creation of complex geometries and functional parts. This technology enables customization and improved performance for specific applications, catering to diverse industry needs.
As these technologies mature, they offer manufacturers enhanced accuracy, increased material options, and new opportunities for innovation.
Advancements in CNC Machining
CNC machining is also evolving through various advancements that help businesses meet modern challenges. The following trends are noteworthy:
- Smart CNC CNC Machining: The integration of IoT into CNC machines enhances operational efficiency. Smart machines can collect data, monitor performance, and predict maintenance, reducing downtime and operational costs.
- 5-Axis Machining: Unlike traditional 3-axis systems, 5-axis machines allow for more complex shaping and machining of parts. This level of precision is ideal for industries requiring intricate designs, such as automotive and aerospace.
- Enhanced Materials and Coatings: The use of advanced materials and coatings increases performance and durability. For instance, the application of ceramic coatings can extend the lifespan of tools, optimizing machining processes and reducing waste.
"The future of manufacturing lies in technologies that not only advance production but also integrate seamlessly into the existing frameworks and supply chains."
Overall, the innovations in both additive manufacturing and CNC machining promise a future where efficiency is maximized, while the capabilities of these technologies soar to meet the ever-growing demands of industry. As these advancements continue, they will likely redefine how products are conceptualized, designed, and produced, driving further explorations into their applications.
Ending
The conclusion of this article echoes the significant role that the transition from 3D printing to CNC machining plays in the realm of manufacturing. This transition is not merely a change in technology; it represents a shift in approach to design, production, and innovation. Understanding the factors that influence this shift can immensely benefit professionals in the industry, educators, and students alike.
Summary of Key Findings
Throughout this exploration, we determined several key findings:
- Complementary Nature: 3D printing and CNC machining serve as complementary processes in manufacturing. Each has distinct strengths that can address specific production needs.
- Material Efficiency: Methods of CNC machining lead to less material waste compared to traditional subtractive processes and can be tailored for high precision.
- Market Trends: Industries are increasingly recognizing the potential of integrating both technologies. This integration can enhance productivity and optimize product quality.
Understanding these insights is crucial for stakeholders looking to optimize their manufacturing processes.
Final Thoughts on the Future of Manufacturing
Looking ahead, the future of manufacturing is likely to be characterized by further innovations in both 3D printing and CNC machining. There is great potential for advancements that merge these technologies. As automation becomes more prevalent and materials science progresses, the manufacturing landscape will only continue to evolve.
Investment in research and development will be critical. Companies that adapt swiftly to these changes and leverage both 3D printing and CNC technologies will find themselves ahead in a competitive market.
In closing, the exploration of these technologies reveals a dynamic pathway for industries seeking efficiency and innovation. Engaging with both paradigms not only enriches the manufacturing process but also prepares practitioners to face the future head-on.