Phosphate Reactors: Mechanisms and Industrial Applications
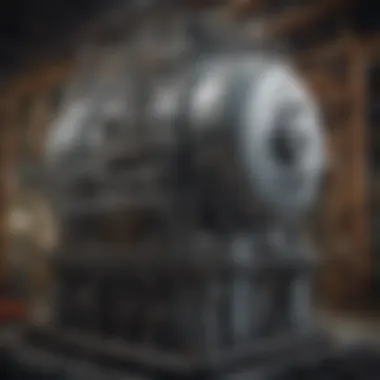
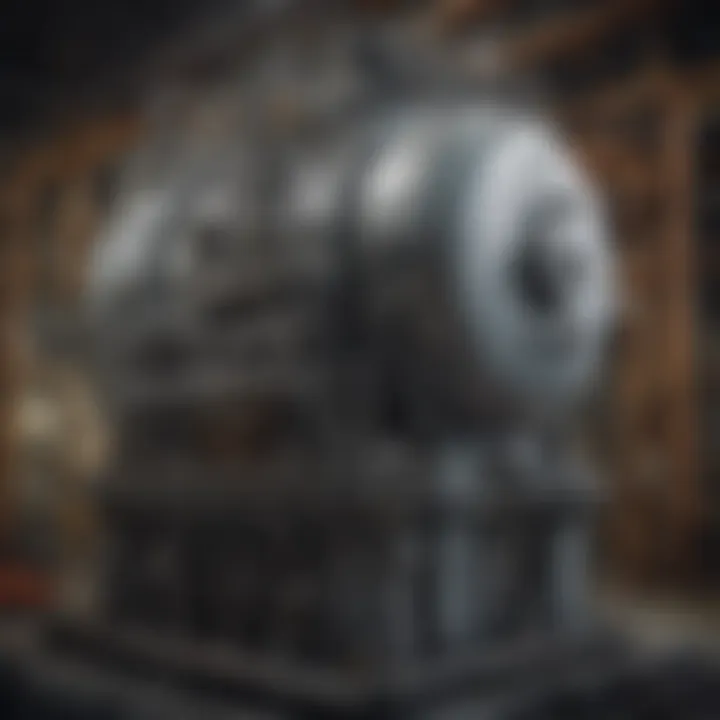
Intro
Phosphate reactors have garnered significant attention in recent years due to their pivotal role in various industrial processes. This article aims to dissect these complex systems, revealing the mechanisms that govern their operation, their design intricacies, and the diverse applications they serve across multiple sectors. The objective is to provide a thorough understanding of not only how these reactors function but also the implications they hold for sustainability and efficiency in chemical processing.
Furthermore, as technology evolves, so too does the capacity and capability of phosphate reactors. Enhanced understanding leads to optimizations that can diminish waste, lower energy consumption, and improve output quality. By doing so, these technologies align closely with current global sustainability goals. This exploration will shed light on operational principles, recent technological advancements, and environmental considerations related to phosphate reactors.
Research Highlights
Key Findings
- Mechanisms: Phosphate reactors utilize specific chemical interactions that promote reactions essential for various industrial applications. Their mechanisms include precipitation processes, adsorption, and other forms of chemical transformations.
- Design Innovations: The design of these reactors has evolved significantly. Innovations such as advanced material selections and improved reactor geometries have extended their operational lifespan and efficiency.
- Diverse Applications: Industries ranging from wastewater treatment to agriculture employ phosphate reactors, showcasing their versatility in handling phosphate compounds efficiently.
"Phosphate reactors are crucial for industries seeking to optimize resource use and mitigate environmental impacts."
Implications and Applications
The implications of utilizing phosphate reactors are vast. Industries can see lowered costs through more effective processes and reduced waste generation. Moreover, these reactors play a pivotal role in not only processing materials but also in ensuring compliance with environmental regulations. For example:
- Agricultural Sector: Enhances nutrient recovery from waste, thus promoting sustainable farming practices.
- Wastewater Treatment: Facilitates the removal of phosphates from effluents, minimizing water pollution.
- Chemical Manufacturing: Develops more efficient pathways for producing phosphate-based chemicals.
In sum, the exploration into phosphate reactors underscores their importance in various industrial contexts while aligning with the broader narrative of sustainability and operational efficiency.
Methodology Overview
Research Design
This article consolidates existing literature and empirical studies on phosphate reactors. It incorporates both theoretical insights and practical applications. The research aims to provide a balanced view that is informative yet accessible to different audiences, from students to seasoned professionals in the field.
Experimental Procedures
Though experimental data is not the focus of this article, understanding the operational framework of phosphate reactors involves reviewing various experimental setups used in past research. This includes the assessment of reaction kinetics, thermodynamic calculations, and the efficiency of different reactor designs employed in practical scenarios.
From these findings, the narrative provided here not only elucidates the mechanisms behind phosphate reactors but also encourages readers to consider their future applications and improvements.
Prologue to Phosphate Reactors
Phosphate reactors play a pivotal role in the chemical industry, particularly where phosphate compounds are concerned. Understanding this topic is essential because it offers insights into various applications, from manufacturing fertilizers to treating wastewater. These reactors are specifically designed to facilitate and optimize the chemical reactions that involve phosphates. Consequently, their design and operation directly impact both the efficiency of production processes and the environmental sustainability of industries that rely on phosphate reactions.
The importance of phosphate reactors is underscored by their varied functions across multiple sectors. They contribute significantly to agricultural productivity by producing phosphate fertilizers, which are crucial for maintaining soil fertility. Additionally, phosphate reactors are integral to several processes in industrial manufacturing and wastewater treatment, highlighting their versatility and significance.
Definition and Purpose
Phosphate reactors are specialized equipment used to carry out chemical reactions involving phosphate compounds. Their primary purpose is to facilitate the conversion of raw materials into usable chemicals through controlled reactions. These reactors vary in design, including batch and continuous systems, to suit different application needs.
The main goal of a phosphate reactor is to maximize reaction efficiency while ensuring that the end products meet the required specifications. This involves careful management of factors like temperature, pressure, and reaction time, which can greatly influence the output quality and yield.
Historical Development
The historical development of phosphate reactors can be traced back to the early 20th century when the need for efficient fertilizer production became apparent. As agricultural practices advanced, the demand for phosphates increased, prompting innovations in reactor design to improve production processes.
In the decades that followed, significant technological developments helped shape modern phosphate reactors. Innovations such as enhanced catalytic processes, optimized thermal management, and advanced monitoring systems have evolved. The shift toward more sustainable practices has also marked a notable progression in reactor design, reflecting a growing awareness of environmental concerns.
As industries strive for increased efficiency and reduced ecological footprints, understanding the evolution of phosphate reactors becomes vital. It provides context for current technologies and informs future innovations in the field.
Chemical Fundamentals of Phosphate Reactions
Understanding the chemical fundamentals of phosphate reactions is crucial for the study of phosphate reactors. Phosphate reactions play a vital role in various industrial processes, impacting how materials are transformed and utilized. The reactions involved determine the efficiency and effectiveness of phosphate utilization in multiple applications, ranging from manufacturing to environmental management.
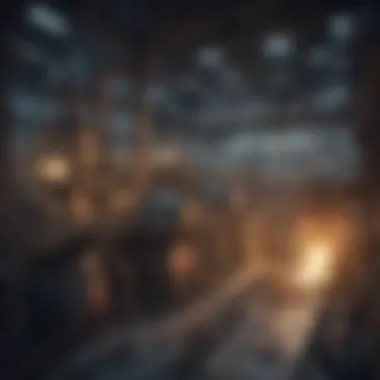
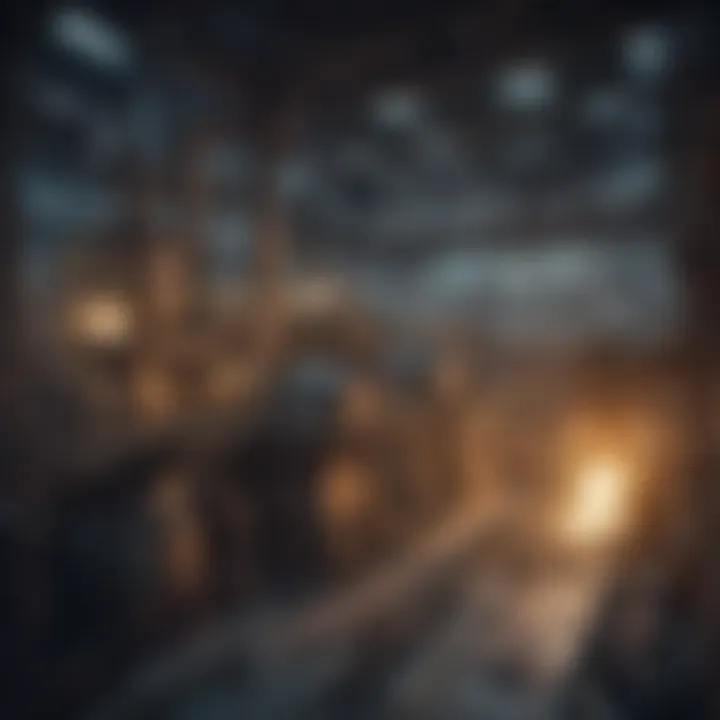
Key Chemical Reactions
Key reactions in phosphate chemistry include the interaction between phosphoric acid and various bases, forming phosphate salts. These reactions are essential in producing fertilizers, which are crucial for agriculture. Another significant reaction is the interaction of phosphates with metals, which can lead to complex compounds. The stability and solubility of these compounds are critical parameters that affect their utility in different processes.
Furthermore, reactions such as hydrolysis and esterification are also relevant when discussing phosphate chemistry. Hydrolysis, for instance, involves the breakdown of phosphoric esters in aqueous solutions, leading to the release of essential nutrients. The understanding of these reactions allows for better control over processes, optimizing them for desired outcomes.
Role of Catalysts
Catalysts play an important role in the phosphate reaction chemistry. They can significantly speed up reactions without being consumed in the process. In phosphate reactors, catalysts enhance the rate of reactions, allowing for more efficient production. Transition metals like nickel and palladium have been studied for their effectiveness in catalyzing phosphate ester reactions.
Using catalysts can reduce energy requirements, making processes more sustainable. Moreover, they can shift equilibrium positions favorably in reactions, leading to higher yields. Thus, selecting an appropriate catalyst is a key consideration in the design and operation of phosphate reactors.
In summary, understanding the chemical fundamentals of phosphate reactions not only aids in the optimization of current phosphate reactor technologies but also fosters innovations for future industrial applications. The mastery of these concepts is essential for researchers and professionals in the field.
Types of Phosphate Reactors
Phosphate reactors play a crucial role in various chemical processes. Understanding the different types enhances the comprehension of their applications and efficiencies. These reactors can be broadly classified into three categories: batch reactors, continuous flow reactors, and plug flow reactors. Each type has its unique characteristics and benefits that cater to specific operational needs.
Batch Reactors
Batch reactors are one of the most common setups in the phosphate processing industry. In this system, all reactants are added to the reactor at the beginning and allowed to react for a set period. After the reaction is complete, the products are removed before the next batch begins. This setup is advantageous for several reasons:
- Flexibility: They allow for easy changes in formulations and production quantities, making them suitable for small-scale operations or research purposes.
- Control: Reaction conditions such as temperature, pressure, and time are easily controlled, beneficial when handling sensitive phosphate reactions.
- Cost-effective: Initial investment and operational costs might be lower compared to continuous systems, especially for smaller facilities.
However, batch reactors also come with challenges. They generally have lower production rates and can require more time to switch between batches. This may limit their efficiency in large-scale applications, but their versatility makes them a staple in certain scenarios.
Continuous Flow Reactors
Continuous flow reactors offer a different operational paradigm. In this design, reactants are continuously fed into the reactor while products are simultaneously removed. This setup is particularly relevant for large-scale phosphate production. The advantages include:
- Efficiency: Higher production rates are achievable as the system operates non-stop, minimizing downtime.
- Steady State Operation: This leads to more consistent product quality, as conditions remain stable.
- Scalability: It is easier to scale operations up as demands increase, making this type favored in industrial contexts.
However, the design complexity and the need for careful monitoring can pose challenges. Continuous flow reactors require precise control systems to handle fluctuations in flow rates and reaction conditions to ensure product quality is not compromised.
Plug Flow Reactors
Plug flow reactors represent a specialized case of continuous reactors. In this system, fluid moves through the reactor in a uniform “plug” and does not mix with surrounding fluid. This distinct flow pattern provides some notable benefits:
- Predictable Flow Characteristics: The uniformity in flow leads to well-defined residence times, which can enhance product consistency.
- Increased Reaction Efficiency: Reactants have a greater opportunity to react thoroughly as they are not subjected to back-mixing.
- Process Intensification: Plug flow reactors can achieve higher conversions per unit volume compared to other reactor types.
Despite their advantages, they require careful design, particularly in terms of size and configuration to ensure that the required flow dynamics are achieved. These reactors are ideal for specific applications, particularly in the production of high-purity phosphates.
In summary, the choice among batch, continuous flow, and plug flow reactors is critical for optimizing phosphate processing efficiency.
Design and Engineering of Phosphate Reactors
The design and engineering of phosphate reactors are critical elements in ensuring effective chemical processes. A well-thought-out design enhances the efficiency, safety, and sustainability of phosphate reactions. These reactors must accommodate specific chemical interactions while minimizing operational challenges. Understanding the principles of reactor design allows engineers and researchers to optimize production rates and manage energy consumption. This section explores three fundamental aspects of design and engineering—design parameters, material selection, and thermal management.
Design Parameters
Design parameters of phosphate reactors shape their operational efficiency. Factors such as size, shape, and configuration impact the flow dynamics within the reactor. A reactor's geometry influences the mixing of reactants, residence time, and overall reaction kinetics. Key design parameters include:
- Reactor Volume: Determines how much reactant can be processed within a specific timeframe.
- Internal Geometry: Affects turbulence and mixing functionalities, promoting a uniform reaction environment.
- Inlet and Outlet Positions: Influences how materials circulate and flow through the reactor, impacting performance.
The selection of design parameters requires careful analysis. Engineers often utilize computational fluid dynamics (CFD) simulations to predict behavior within the reactor. Such simulations provide insights into how altering parameters can lead to improved reaction efficiencies.
Material Selection
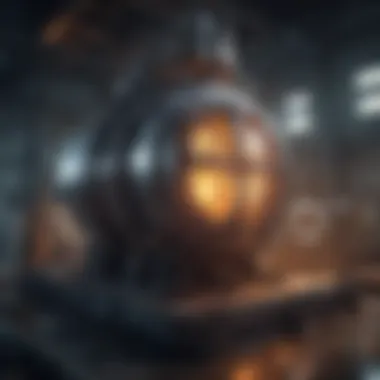
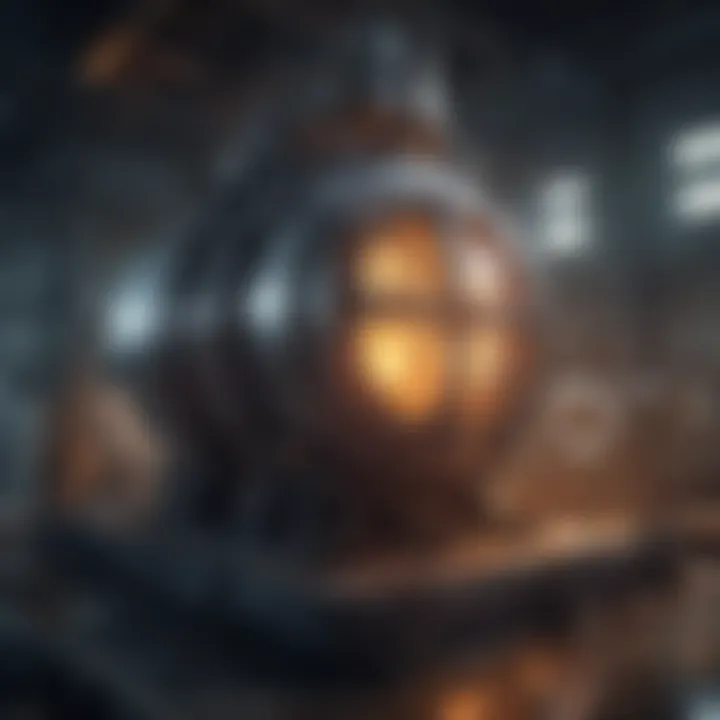
Material selection is another crucial aspect of phosphate reactor design. The materials used must withstand the corrosive nature of phosphate compounds and the elevated temperatures involved in many phosphate reactions. Durability and compatibility with reactants are essential considerations. Common materials include:
- Stainless Steel: Offers good corrosion resistance and can handle moderate temperatures.
- Carbon Steel: More economical but may require coating to protect against corrosion.
- High-Nickel Alloys: Provide excellent durability for harsher conditions, but at a higher cost.
The interactions between materials and phosphate compounds can lead to degradation over time. Therefore, selecting the right materials not only contributes to reactor longevity but also impacts maintenance and operational costs.
Thermal Management
Effective thermal management enhances the performance and safety of phosphate reactors. During phosphate reactions, temperature fluctuations can drastically affect reaction rates and product quality. Engineers must ensure that the reactor can maintain optimal temperature ranges consistently. Key strategies for thermal management include:
- Insulation: Proper insulation minimizes heat loss, promoting energy efficiency.
- Heating and Cooling Systems: Effective systems are necessary for regulating temperatures during exothermic or endothermic reactions.
- Monitoring Sensors: Regular monitoring can help detect temperature deviations, ensuring immediate corrective actions if needed.
In summary, the design and engineering of phosphate reactors encompass a variety of factors. By focusing on design parameters, material selection, and thermal management, engineers can create systems that optimize chemical production while addressing environmental considerations.
Operational Considerations
Operational considerations are paramount to the effective use and efficiency of phosphate reactors. Their design and management directly influence not only the quality of the output but also the safety and longevity of the reactor systems. For companies adopting phosphate reactors, understanding these considerations ensures that processes remain on schedule, minimizing unexpected downtimes and enhancing productivity.
Temperature and Pressure Control
Temperature and pressure are critical factors in the operation of phosphate reactors. Maintaining optimal conditions is essential for the success of chemical reactions occurring within the reactor. Deviating from these optimal ranges may lead to incomplete reactions or unwanted byproducts, jeopardizing the entire process.
Temperature influences reaction rates and equilibrium. For instance, increasing the temperature can increase reaction speed, but it may also alter the equilibrium position, potentially favoring undesirable products. Correctly monitoring and regulating the temperature helps meet reaction requirements while also ensuring safety. Too high of a temperature can escalate the risk of safety hazards, including thermal runaway or equipment failure.
Pressure control is equally vital. Reactions under pressure can enhance reaction rates and, in some cases, improve yield. However, excessive pressure could lead to mechanical failures or safety incidents. Operators must use reliable pressure gauges and automatic controls to adjust pressure levels as necessary, ensuring they remain within safe bounds.
By integrating sophisticated temperature and pressure monitoring technology, operators can greatly reduce the risks and improve overall efficiency in phosphate reactors, leading to a more steady and productive operation.
Monitoring and Control Systems
The implementation of monitoring and control systems in phosphate reactors is essential for maintaining desired operational parameters. These systems provide real-time data to operators, allowing for quick adjustments when necessary. They often include sensors for temperature, pressure, and reactive concentration, all of which are crucial for optimizing reactor performance.
Effective monitoring systems enable early detection of deviations from established parameters, facilitating corrective actions before they escalate into significant problems. Automated control systems can adjust various operational variables, reducing the chance for human error and enhancing safety.
In addition to physical measurements, software solutions can analyze data trends, helping operators predict potential issues before they occur. This proactive approach to management helps maintain high levels of productivity and minimizes waste.
"An effective control system leads to increased safety, reduced operational costs, and improved overall process integrity."
When selecting a monitoring and control system, it is vital to consider compatibility with existing equipment and the specific requirements of phosphate operations. The integration of these systems is not merely an option but a necessity for modern phosphate reactor operations.
Applications of Phosphate Reactors
Phosphate reactors hold significant importance across various industries. Their versatile applications showcase their essential role in optimizing processes and addressing environmental challenges. Exploring these applications can offer insights into how phosphate reactors contribute to efficiency, sustainability, and innovation in chemical processing.
Industrial Manufacturing
In industrial manufacturing, phosphate reactors are crucial for synthesizing phosphorus-containing compounds. These compounds serve as important intermediates in producing fertilizers, detergents, and flame retardants. The control over chemical reactions within these reactors enables manufacturers to achieve high yields and superior product purity.
Moreover, these reactors allow for the efficient use of raw materials, leading to lower production costs. Efficient mixing and temperature control within phosphate reactors are essential. This efficiency reduces waste and enhances productivity, benefiting both the environment and the bottom line of companies. Additionally, innovations in reactor design improve safety and reduce risks associated with the handling of hazardous materials.
Wastewater Treatment
Wastewater treatment is another critical application of phosphate reactors. Phosphorus is a key nutrient that can contribute to eutrophication in water bodies if not managed properly. Phosphate reactors are employed in biological nutrient removal processes. These reactors help in effectively removing excess phosphates from wastewater streams before they are released into the environment.
By treating wastewater through these reactors, facilities can meet environmental regulations and minimize freshwater pollution. The integration of phosphate reactors in wastewater systems enhances overall treatment efficiency. Other benefits include lower operational costs and improved nutrient recovery methods. Therefore, it plays a vital part in maintaining sustainable water resources.
Agricultural Applications
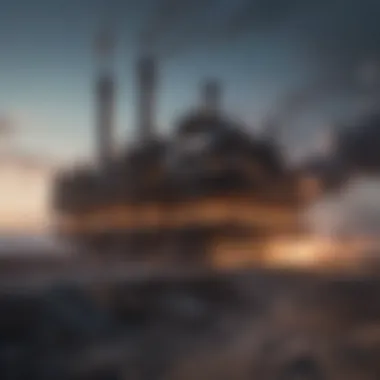
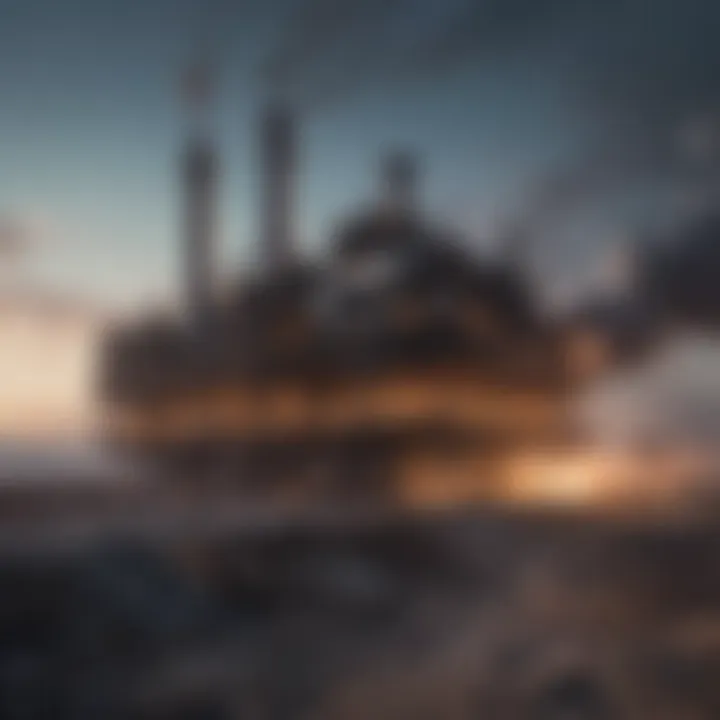
Phosphate reactors also find significant use in agriculture. They play an essential role in producing phosphate fertilizers that are vital for crop growth. Notably, phosphate fertilizers enhance soil fertility and boost agricultural productivity. The design of phosphate reactors allows for the synthesis of fertilizers with specific nutrient profiles tailored to meet the needs of various crops.
Furthermore, the efficiency and effectiveness of phosphate reactors contribute to the optimization of fertilizer application, minimizing chemical runoff into water sources. This enhancement leads to better yield while also supporting sustainable farming practices. The judicious use of phosphate-based fertilizers facilitated by these reactors contributes to global food security by ensuring consistent crop production.
"Phosphate reactors not only improve industrial processes but also contribute directly to sustainable practices in agriculture and wastewater treatment."
In summary, the applications of phosphate reactors span crucial sectors such as industrial manufacturing, wastewater treatment, and agriculture. Their impact is profound, influencing production efficiency, resource management, and environmental sustainability.
Environmental Impacts
The role of phosphate reactors in contemporary industrial processes cannot be overlooked, especially regarding their environmental impacts. As industries push for innovation, they must also address the ecological footprint of their operations. Phosphate reactors are at the forefront of this challenge, ensuring that while they meet production demands, they also adhere to increasingly stringent environmental regulations. The implications of their use impact various aspects, including pollution control and broader sustainability practices.
Pollution Control Measures
Phosphate reactors contribute significantly to pollution control. Their operational design incorporates mechanisms that minimize the release of harmful byproducts into the environment. Here are a few specific elements that illustrate the importance of pollution control in these systems:
- Reduction of Phosphates in Effluents: Phosphate reactors often feature advanced filtration systems that reduce phosphate concentration in wastewater. This not only helps in compliance with environmental standards but also protects aquatic ecosystems from eutrophication, a harmful algal bloom induced by excess nutrients.
- Emissions Reduction Technologies: Many modern reactors utilize scrubbers and other emission control technologies that capture volatile organic compounds and other harmful gases. As a result, the local air quality may improve, further protecting public health.
- Waste Minimization Techniques: By optimizing the chemical processes within reactors, industries can reduce waste generation. This can include recycling unreacted phosphates back into the process or finding ways to repurpose byproducts as raw materials in other applications.
"Efficiency increases in phosphate reactors are vital for minimizing environmental footprints while still meeting industrial outputs."
Sustainability Practices
Sustainability is a key focus in the design and operation of phosphate reactors. The following practices underscore their contributions to sustainable industrial processes:
- Resource Efficiency: Phosphate reactors are designed to utilize raw materials efficiently. This not only reduces input costs but also decreases the extraction of natural resources, promoting a more sustainable approach to phosphate utilization.
- Energy Efficiency Initiatives: Advances in reactor design have led to improved energy use. Implementing energy recovery systems within reactors can turn waste heat back into productive energy, thus enhancing overall system efficiency.
- Life Cycle Assessment (LCA): Many companies are adopting LCA to evaluate the complete environmental impact of phosphate reactors. This includes assessing raw material sourcing, operational energy needs, and final disposal of materials, ensuring that each phase aligns with sustainability goals.
Future Prospects in Phosphate Reactor Technology
The future of phosphate reactor technology is not only important but also essential for the advancement of chemical processes across various industries. As the global demand for phosphate continues to rise due to its critical role in agriculture, energy, and environmental management, researchers and engineers are focusing on innovative approaches to enhance these systems. The transparency in this field often leads to significant breakthroughs that could resolve several pressing industrial challenges.
Innovation and Research Trends
Current trends in innovation focus on improving the design and functioning of phosphate reactors through cutting-edge technologies. Machine learning and artificial intelligence are being integrated into modeling efforts, which allows for more accurate predictions on reaction behaviors. Such advancements enable optimization of feedstock usage and improve catalyst performance, ultimately leading to lower operational costs and improved yields.
Moreover, the incorporation of advanced materials in reactor design is another key trend. Researchers are experimenting with novel alloys and coatings that can improve corrosion resistance and withstand high temperatures and pressures. Each of these innovations carries the potential to enhance reliability and longevity of phosphate reactors in varying operational environments.
"Innovative advancements in phosphate reactor technology are pivotal for achieving efficiency and sustainability in production processes."
Potential Improvements in Efficiency
Enhancing the efficiency of phosphate reactors encompasses a multi-faceted approach. One of the primary avenues for this improvement is to focus on maximizing reaction kinetics. By understanding and controlling the reaction pathways more effectively, manufacturers can reduce waste and maximize the output. This includes fine-tuning variables such as temperature, pressure, and reactant concentrations.
Another significant improvement can stem from better heat integration strategies. Employing waste heat recovery systems could potentially lead to significant energy savings. This not only results in cost benefits but also decreases the environmental footprint of phosphate production.
A full assessment of energy consumption and material flow within the reactors reveals further avenues for optimization. Continuous monitoring technologies, such as real-time analytics and advanced sensors, can play a critical role by providing necessary data for immediate adjustments during operations. As conditions inside reactors are continuously monitored, operational adjustments can be made promptly to maintain optimal efficiency.
The End
Phosphate reactors are critical in various industrial environments, showcasing a blend of chemical engineering and environmental considerations. Their ability to transform feedstocks into valuable products while managing waste is essential for modern processing techniques. Understanding phosphate reactors allows for better application of technology in sectors such as manufacturing, agriculture, and wastewater treatment.
Summary of Key Points
In this article, we explored several crucial aspects of phosphate reactors:
- Definition and Purpose: We discussed what phosphate reactors are and their primary roles within the industry.
- Chemical Reactions: The key chemical processes that occur in phosphate reactors were outlined, highlighting the significance of catalysts in enhancing these reactions.
- Types of Reactors: Different reactor types were examined, including batch, continuous flow, and plug flow reactors, each with unique operational characteristics.
- Engineering Design: We explored the critical design parameters necessary for effective reactor performance, such as material selection and thermal management.
- Operational Considerations: The importance of temperature, pressure control, and monitoring systems was emphasized for efficient reactor operation.
- Industrial Applications: We detailed various applications of phosphate reactors across different sectors and their relevance to sustainability.
- Environmental Impacts: A discussion on pollution control measures and sustainability practices underscored the importance of maximizing environmental benefits.
- Future Prospects: Potential innovations and improvements were highlighted, suggesting a promising future for phosphate reactor technology.
Closing Thoughts
Phosphate reactors represent a vital component of modern chemical processes. Their efficient design and varied applications demonstrate their importance in addressing both industrial needs and sustainability challenges. As technology advances, the potential for phosphate reactors to contribute positively to environmental goals becomes increasingly significant. It is essential for researchers, engineers, and industry professionals to remain engaged with ongoing developments in this field. Continued study of phosphate reactors will not only ensure enhanced efficiency but also foster innovative solutions for upcoming challenges in chemical manufacturing and beyond.
"The future of phosphate reactors lies in integrating advanced technologies to minimize environmental impact and maximize efficiency, leading the way in sustainable industrial practices."
Such a focus will cement phosphate reactors as indispensable tools in a world where sustainability is a growing priority.