The Science of Heat Fins: Design and Functionality
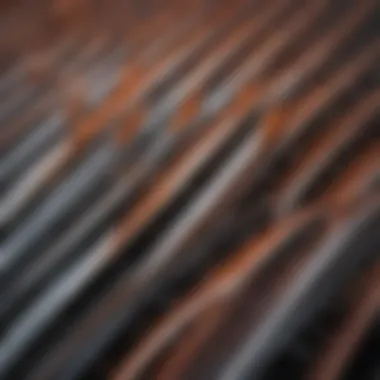
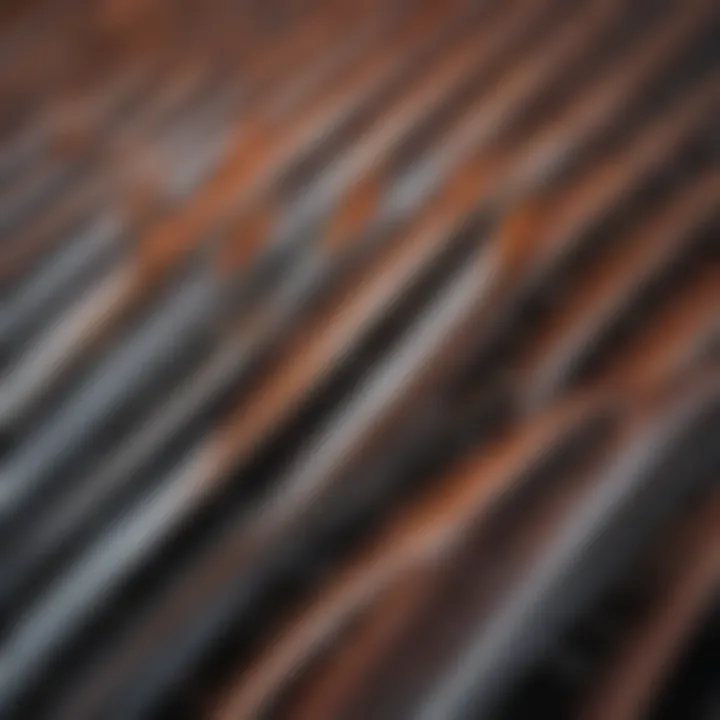
Intro
Heat fins are critical components in thermal management systems, designed to enhance heat dissipation. They serve various applications, ranging from cooling in electronic devices to industrial heat exchangers. Understanding the design and functionality of heat fins is paramount for engineers and researchers seeking to improve efficiency in thermal systems.
This article will explore the principles underlying heat fins, discussing their materials, design considerations, and effectiveness in various applications. It will provide insight into key findings from recent studies, the methodologies used to evaluate heat fins, and their implications in real-world scenarios. The goal is to equip readers with a comprehensive understanding of heat fins and their significance in modern technology.
Research Highlights
Key Findings
Research has revealed several critical points regarding heat fins:
- Materials: The choice of materials greatly influences thermal conductivity and durability. Common choices include aluminum and copper due to their excellent heat-conducting properties.
- Surface Area: Increasing the surface area of fins enhances heat dissipation. This can be achieved through elaborate designs, such as fractal shapes.
- Thermal Conductivity: The efficiency of heat fins is directly proportional to the thermal conductivity of the materials used. Higher conductivity leads to better heat transfer.
Implications and Applications
The advancements in heat fin technology have meaningful implications for various industries:
- Electronics: As devices become more compact, effective heat fins are critical for maintaining performance and longevity.
- Automotive: Heat fins are essential in radiators and cooling systems to manage engine temperatures effectively.
- Renewable Energy: In solar power systems, heat fins can enhance efficiency by dissipating excess heat generated during operation.
"Heat fins play a vital role in maintaining optimal operating temperatures in diverse applications, thus enhancing overall system performance."
Methodology Overview
Research Design
Investigating the functionality of heat fins primarily involves experimental and theoretical approaches. Researchers often use simulations alongside empirical testing to analyze performance under various conditions.
Experimental Procedures
Several methods are commonly employed:
- Thermal Testing: Measuring temperature variations helps assess the efficiency of heat fins.
- Computational Fluid Dynamics (CFD): Simulations provide insights into airflow patterns, which influence heat transfer rates.
- Material Testing: Evaluating thermal properties of different materials ensures optimal choices for specific applications.
By employing these methodologies, researchers can identify optimal designs and materials that maximize the performance of heat fins in their respective applications.
Preamble to Heat Fins
Heat fins play a pivotal role in thermal management systems across various fields, ranging from electronics to automotive engineering. The primary function of heat fins is to enhance the dissipation of heat generated by components, thereby preventing overheating and maintaining operational efficiency. Understanding their design and functionality facilitates the optimization of devices where thermal regulation is crucial.
One significant aspect is their capacity to increase the surface area exposed to the cooling medium, which can be air or liquid. This enhanced surface area allows for improved heat exchange, promoting more effective cooling mechanisms. Furthermore, the materials and configurations of heat fins are carefully chosen to maximize thermal conductivity and ensure longevity, which are vital factors in their respective applications.
In addition to improving performance, heat fins contribute to the safety of electronic equipment and vehicles by mitigating the risks associated with excessive heat. Their historical evolution demonstrates a consistent focus on enhancing materials and design strategies, reflecting the advanced technological landscape today.
Definition and Purpose
Heat fins, often referred to as heat sinks, are devices that help dissipate heat from a hot surface to the surrounding environment. They typically consist of a series of fins that extend from a base, which is connected to the heat-generating component. The purpose of these structures is quite straightforward: to manage excess heat effectively, ensuring that sensitive components do not exceed their operational temperature limits. Their performance is essential for maintaining the reliability and longevity of various devices, from computer CPUs to electric motors.
Historical Development
The concept of heat dissipation dates back to the early 20th century, although the term 'heat fin' was popularized later. Early heat sinks were simple in design, typically made from metals like aluminum and copper. As technology progressed, the understanding of thermodynamics led to advancements in material science, resulting in more sophisticated designs. Modern heat fins incorporate not just improved materials but also intricate geometric shapes to enhance efficiency. For instance, contemporary research explores the use of composite materials and even nanotechnology to revolutionize heat management.
In summary, the journey of heat fins reflects a continuous innovation cycle surrounding thermal management. This ongoing evolution is crucial as electronic devices grow in complexity and power density, making the study of heat fins ever more relevant in today's technological landscape.
Fundamental Principles of Heat Exchange
Understanding the fundamental principles of heat exchange is crucial for the effective design of heat fins. These principles provide a framework for evaluating how heat is transferred and managed in various applications. The benefits of a solid grasp of thermal exchange are numerous, especially when optimizing the performance of heat fins in different environments. Efficient heat management can enhance both the reliability and lifespan of electronic devices, automotive systems, and industrial equipment.
Thermal Conductivity Basics
Thermal conductivity is one of the key properties influencing heat fins. It defines the ability of a material to conduct heat. In essence, materials with high thermal conductivity, like copper and aluminum, are preferred for heat fins because they can transfer heat away from a heat source rapidly.
The choice of material affects the overall efficiency of heat dissipation. For example, aluminum is lightweight and cost-effective, making it a common choice in many applications. However, copper, with its superior conductivity, is often used in specialized settings where enhanced performance is necessary, despite its higher cost. Understanding these properties can guide engineers in selecting appropriate materials based on operational requirements.
Convection and Conduction
Convection and conduction are two fundamental modes of heat transfer critical to the operation of heat fins.
- Conduction is the process by which heat is transferred through direct contact between materials. In heat fins, effective conduction ensures that the heat is transferred from the source, such as an electronic component, to the fin itself.
- Convection, on the other hand, occurs when heat is transferred through a fluid (liquid or gas) moving around the fin. Natural convection relies on buoyancy forces, while forced convection involves external means, such as fans, to enhance heat transfer.
Both mechanisms must be optimized in heat fin design to achieve maximum thermal efficiency. For instance, fin spacing can influence airflow and thus affect convective heat transfer rates. Properly designed fins maximise both conduction and convection to ensure that heat dissipation is efficient.
Radiative Heat Transfer
Radiative heat transfer plays a vital role in situations where heat fins are exposed to environments with varying temperature levels. This process involves the transfer of heat in the form of electromagnetic waves. Unlike conduction and convection, radiative heat transfer does not require a medium to transfer heat; it can occur in a vacuum.
The effectiveness of radiative heat transfer depends on several factors, including surface emissivity and temperature difference.
- Higher emissivity materials can radiate more heat than lower emissivity materials. In many designs, the surface finish and coatings are modified to enhance emissivity.
- As the surface temperature increases, the rate of radiative heat transfer also increases significantly, making this principle especially relevant in high-temperature applications.
Overall, understanding radiative heat transfer allows engineers to improve the design of heat fins to ensure they function effectively in diverse thermal environments.
Types of Heat Fins
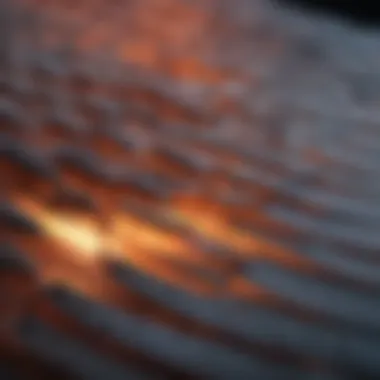
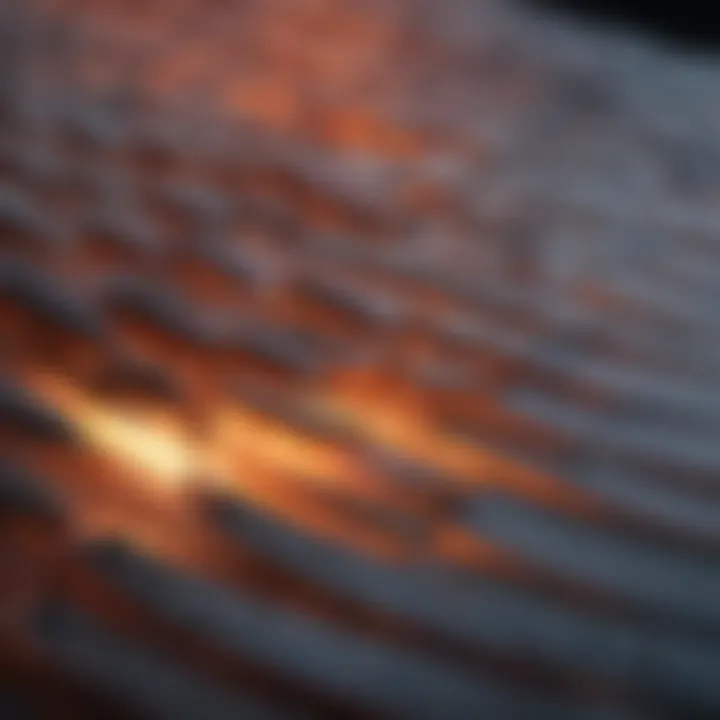
Understanding the different types of heat fins is important for evaluating their applications and effectiveness in various contexts. Heat fins are employed to enhance thermal management in numerous systems, ranging from electronics to automotive sectors. The decision on which type of heat fin to employ hinges on several pivotal aspects, including the specific cooling requirements, space availability, and environmental conditions. The classifications primarily divide into two categories: passive heat fins and active heat fins, both of which have distinct functionalities and applications.
Passive Heat Fins
Passive heat fins operate without any external power source. Instead, they rely on natural processes such as convection and conduction to promote heat dissipation. These fins are often made from materials with high thermal conductivity, like aluminum or copper, allowing them to effectively transfer heat away from critical components.
Some key points regarding passive heat fins include:
- Simplicity: Passive heat fins generally involve a straightforward design, which makes them cost-effective and easy to implement.
- No Added Energy Consumption: Operating without power usage contributes to energy efficiency.
- Reliability: Fewer moving parts translate to less risk of failure, which is crucial in many applications.
Examples of their use include heat sinks in computer processors where maintaining a low temperature is essential for performance. Knowing when to employ passive fins can greatly enhance the reliability of thermal management solutions.
Active Heat Fins
In contrast, active heat fins utilize external energy sources, typically fans or pumps, to enhance the heat dissipation process. These fins can achieve more effective cooling due to forced convection, which circulates air more efficiently than natural convection alone. Active heat fins are common in situations where heat generation is high and heat dissipation must occur rapidly to maintain system performance.
Significant characteristics of active heat fins include:
- Improved Cooling Capacity: Active systems often outperform passive ones due to their ability to move air at higher rates.
- Versatility: They can be designed for a variety of environments and can adapt to different cooling needs by adjusting airflow.
- Cost Considerations: Initial costs may be higher due to the additional components, but they can save money in long-term operational efficiencies in high-demand scenarios.
An applicable instance might be in high-performance gaming systems or industrial machinery where overheating poses a substantial risk. Understanding when to incorporate active fins into a design can significantly influence performance outcomes.
Overall, the choice between passive and active heat fins is determined by the specific needs of the system being designed. Each type has its advantages and considerations, and knowing these can guide optimal solutions for effective heat management.
Materials Used in Heat Fin Design
The choice of materials for heat fins is crucial as it directly influences performance and efficiency. Different materials offer unique properties that can enhance their effectiveness in thermal management. Understanding materials is essential for optimizing heat dissipation in various applications.
Several factors come into play when selecting materials for heat fins. Factors include thermal conductivity, weight, corrosion resistance, and manufacturability. High thermal conductivity allows for more efficient heat transfer, while durability ensures that heat fins can withstand harsh working conditions.
Metallic Materials
Metallic materials are among the most common choices for heat fins. This preference relates to their high thermal conductivity, which is essential for effective heat transfer. Most notably, metals like copper and aluminum are often utilized.
Aluminum, known for its lightweight and good thermal conductivity, is also resistant to corrosion. This makes it ideal for applications in automotive and electronics cooling. Conversely, copper provides better thermal conductivity than aluminum but is heavier and more expensive. Its use is often seen in high-performance applications where heat dissipation is a primary concern.
"Copper’s superior thermal properties make it a preferred choice in applications where efficiency is key, despite higher costs."
However, it's worth noting that the choice between these metals also involves trade-offs regarding cost and weight. For larger applications, aluminum often prevails due to its balance between performance and economic viability.
Composite Materials
Composite materials are emerging as a viable alternative to traditional metals in the design of heat fins. These materials combine multiple constituents to achieve superior properties that single materials alone may lack. Common composites may involve a matrix of polymers reinforced with carbon fibers or ceramics.
The main advantage of composite materials lies in their versatility. They can be tailored to achieve specific thermal management needs, such as weight reduction and enhanced durability. Moreover, composites can offer improved resistance to chemical degradation, making them suitable for environments where exposure to harsh substances is a concern.
One significant drawback of using composite materials is their generally lower thermal conductivity compared to metals. Therefore, they need careful design considerations to enhance their effectiveness in heat dissipation.
In summary, the ongoing advancements in material science are broadening the horizon for researchers and engineers in heat fin design. By choosing the right material, one can profoundly affect the performance of thermal management systems and ensure optimal heat dissipation.
Design Considerations for Heat Fins
In the realm of heat fin technology, design considerations play a crucial role in enhancing efficiency and effectiveness in thermal management. Designers must recognize that the performance of heat fins does not solely depend on the materials used. Instead, elements such as surface area, geometric configurations, and heat transfer efficiency come together to dictate a heat fin's overall functionality. By prioritizing these considerations, one can improve thermal dissipation and contribute to the advancement of various applications ranging from electronics cooling to automotive systems.
Surface Area Optimization
Surface area is a vital factor in heat fin design. The basic principle is simple: a larger surface area fosters improved heat exchange. This is because more surface area enables greater exposure of the fin to surrounding air or fluid, thus increasing the transfer of thermal energy. Engineers typically maximize surface area through specific design techniques. For instance, fins are often designed with intricate patterns or added protrusions that increase their effective area without adding substantial weight or bulk.
The optimization does not just mean increasing size. It involves a meticulous balance. Too much surface area can lead to increased resistance to airflow, which ultimately hinders convection, a critical component in heat transfer. Hence, a well-optimized surface area can significantly boost the efficiency of thermal management systems.
Geometric Configurations
Another key consideration is the geometric configuration of heat fins. Different shapes can yield varied performance outcomes. Common configurations include straight, pin, and zigzag fins. Each design serves specific applications and performance requirements better than others.
- Straight fins are simple in shape and commonly used, but they may not be ideal for all situations.
- Pin fins present a compact design that increases the surface area to volume ratio, suitable for tight spaces.
- Zigzag fins can disrupt airflow and enhance turbulence, leading to better heat transfer rates.
Choosing the right geometry requires an understanding of the application environment. Factors such as fluid flow, thermal load, and available space should guide the decision-making process. Decisions need to consider not just heat dissipation but also manufacturability and cost-effectiveness.
Heat Transfer Efficiency
Heat transfer efficiency is the culmination of various design aspects. It involves understanding the principles of conduction, convection, and radiation. Efficient heat fins must facilitate rapid conduction of heat from the source through the material. Subsequently, they need to promote effective convection as the heat migrates away into the surrounding medium. The effectiveness of this transfer is influenced by all discussed elements, reinforcing their interconnectedness.
Testing and analysis of heat transfer efficiency often utilize simulations or experimental evaluations. Methods like Computational Fluid Dynamics (CFD) allow engineers to visualize buoyancy-driven airflow patterns around fins, contributing to better design choices. Results from these evaluations inform necessary adjustments to optimize performance further.
"Designing efficient heat fins requires attention to detail and an understanding of the complex interactions between surface area, geometry, and heat flow."
Through attentive consideration of these design aspects, developers not only address current challenges in thermal management, but they also pave the way for innovative solutions that adapt to the evolving technological landscape.
Applications of Heat Fins
The application of heat fins is central to efficient thermal management in various industries. Their design and functionality are critical in dissipating heat effectively, ensuring that systems operate within safe temperature ranges. Heat fins serve multiple purposes, from cooling electronic components to managing automotive temperatures and supporting industrial processes. This section dives into these applications, illustrating their significance in modern technology and engineering.
Electronics Cooling
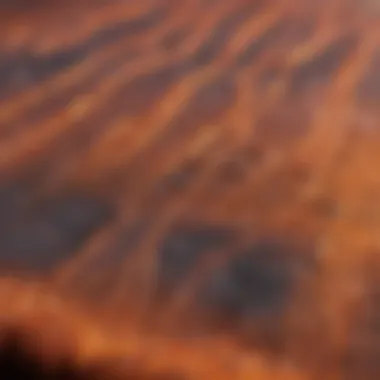
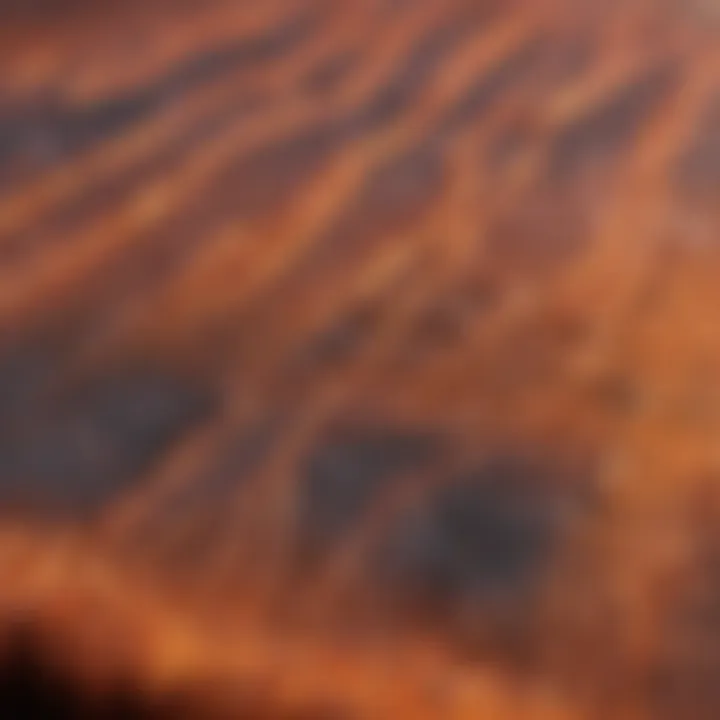
Electronics cooling is one of the most prominent applications of heat fins. In devices like computers and smartphones, heat sinks with fins are utilized to absorb heat generated by components such as processors and graphics cards. Without effective cooling, these components can overheat, leading to reduced performance or even permanent damage.
Heat fins in electronics are often made from materials with high thermal conductivity, such as aluminum or copper. Their design focuses on maximizing surface area to facilitate better heat dissipation. Additionally, the use of passive cooling solutions, like natural convection through fins, eliminates the need for moving parts, thus enhancing reliability.
"Effective electronics cooling via heat fins significantly extends the lifespan of devices while maintaining optimal performance."
Automotive Heat Management
In the automotive industry, heat fins are essential for managing temperatures in engines, radiators, and exhaust systems. As vehicles operate, various components generate heat that must be controlled to prevent overheating. Heat fins assist in distributing heat away from critical systems, maintaining optimal operating conditions.
Automotive heat management is not just about performance; it also affects safety and fuel efficiency. Improper heat dissipation can lead to failures in engine components, affecting overall vehicle reliability. In modern vehicles, the integration of advanced materials and innovative designs for heat fins has become common.
Moreover, the trend towards electric vehicles adds new challenges and opportunities for heat fin design. Battery systems in electric cars require efficient thermal management to enhance performance and longevity. Heat fins play a vital role in ensuring that battery temperatures remain within safe limits.
Industrial Processes
The use of heat fins extends to various industrial processes, where temperature regulation is critical. Equipment like heat exchangers often incorporate fins to increase surface area for heat transfer. In manufacturing, managing heat helps maintain optimal processing conditions, enhancing product quality and safety.
Industries such as food processing, chemical production, and metalworking benefit from using heat fins in their systems. These fins help in efficiently dissipating heat generated during processes, ensuring systems operate effectively and sustainably. Understanding the specific thermal requirements of different applications aids in the design of tailored heat fin solutions.
In summary, heat fins play a vital role across a broad range of applications. Their ability to manage heat efficiently ensures optimal performance and safety in electronics, automotive systems, and industrial processes. As technology continues to advance, the demand for effective heat dissipation solutions will only grow.
Efficiency Evaluations of Heat Fins
The evaluation of heat fins efficiency is crucial in understanding their performance in thermal management systems. This assessment is vital for engineers and designers aiming to optimize heat dissipation in various applications. Knowing how effectively a heat fin transfers heat influences decisions regarding design and material selection. Understanding efficiency evaluations assists professionals in making informed choices that enhance the functionality of thermal systems.
There are several key elements to consider in the efficiency evaluations of heat fins.
- Thermal Performance: This refers to how well a heat fin can transfer heat from its surface to the surrounding environment. Higher thermal performance correlates with improved efficiency, which is essential in scenarios like electronics cooling.
- Design Parameters: The geometry and orientation of the heat fins have profound effects on their efficiency. Evaluating these parameters helps in understanding how they affect airflow and, consequently, heat transfer rates.
- Materials: The selection of materials directly impacts the thermal conductivity of heat fins. Evaluating efficiency involves analyzing the impact of various materials on heat dissipation.
The benefits of efficient heat fins are manifold. First, they enable systems to operate at lower temperatures, ensuring greater reliability and longevity. Efficient designs also contribute to energy savings, which is increasingly important in a world focused on sustainability. Most importantly, evaluating the efficiency of heat fins leads to enhanced performance in diverse applications, from automotive systems to consumer electronics.
Considerations for efficient evaluations include both computational and experimental approaches. Each method has its own strengths and weaknesses, allowing for a comprehensive understanding of performance in real-world scenarios. Evaluating heat fins efficiency requires a detailed approach, as it directly correlates to the successful application and functionality across different industries.
"Understanding efficiency evaluations of heat fins lays the foundation for advancements in thermal management technologies."
Assessment methods play a significant role in the overall design and implementation of heat fins in practical applications.
Computational Fluid Dynamics
Computational fluid dynamics (CFD) is a powerful method used to evaluate the performance of heat fins. CFD simulations allow researchers and engineers to visualize fluid flow and heat exchange around heat fins without physical prototypes. This offers several advantages:
- Predictions: CFD can predict how heat fins will perform under various operating conditions, thus enabling better design adjustments before production.
- Cost-effective: Utilizing CFD can save both time and resources that might be spent on extensive physical testing.
- Detailed Analysis: It provides insights into flow patterns, temperature distributions, and potential hotspots. This helps in identifying areas that need improvement for enhanced efficiency.
CFD software is becoming more sophisticated, allowing for increasingly accurate modeling of complex systems. By integrating this tool into the design phase, engineers can iterate and optimize designs rapidly.
Experimental Methods
Experimental methods are crucial in validating the predictions made by computational fluid dynamics. Physical testing allows one to assess the performance of heat fins in real scenarios.
- Test Setup: Different setups can be employed, including wind tunnel experiments or heat exchangers, depending on the specific application.
- Measurements: Instruments are used to measure temperature, flow rates, and heat transfer coefficients. This data is essential for evaluating how closely the performance aligns with CFD predictions.
- Data Analysis: Analyzing experimental data helps in refining models and improving future designs by understanding discrepancies between simulated and actual performance.
The combination of computational and experimental methods provides a comprehensive view of heat fin efficiency. This integrated approach is crucial for advancing understanding in thermal management systems, ultimately leading to better designs and improved technologies.
Recent Advancements in Heat Fin Technology
The field of heat fin technology has evolved significantly in recent years due to several advancements in materials science and engineering practices. These changes reflect the growing need for efficient thermal management solutions in various sectors such as electronics, automotive, and industrial processes. Understanding these advancements is crucial for harnessing their benefits effectively.
Innovations in Materials Science
Innovations in materials science have led to the development of new materials that enhance the performance of heat fins. Traditional materials like aluminum and copper are still widely used, but recent advancements include the exploration of advanced alloys and composites.
For instance, materials such as graphene and carbon nanotubes are gaining traction due to their exceptional thermal conductivity properties. These materials can improve heat dissipation while potentially reducing the weight of heat fins. Furthermore, the introduction of phase change materials can enhance thermal management by absorbing and releasing heat during phase transitions.
These advancements lead to multiple benefits, including:
- Increased efficiency: New materials can improve the heat transfer efficiency substantially.
- Weight reduction: Lower weight materials can reduce the overall system mass, crucial for applications in aerospace and automotive.
- Extended lifespan: Advanced coatings can improve corrosion resistance, extending the operational life of heat fins.
Integration with Nanotechnology
The integration of nanotechnology into heat fin design represents a significant leap forward. Nanomaterials can modify several key properties of heat fins, such as thermal conductivity, mechanical strength, and corrosion resistance.
By manipulating materials at the nanoscale, engineers are developing heat fins that are not only robust but also remarkably efficient.
One area of focus is the use of nanofluids in conjunction with heat fins. Nanofluids, which are suspensions of nanoparticles in standard fluids, significantly enhance heat transfer capabilities. The addition of nanoparticles can improve thermal conductivity by several times compared to conventional fluids. This can lead to better cooling performance in various applications, including clothing, automotive engines, and electronic devices.
Overall, the integration of nanotechnology offers promising avenues for improving the performance and functionality of heat fins. This also raises considerations about scalability and the cost of production, making it essential to balance innovation with practical implementation in real-world applications.
"Recent advancements in heat fin technology highlight the critical role of material properties on efficiency and performance."
As the discipline continues to advance, ongoing research and development will likely introduce even more significant changes, shaping the future of thermal management systems.
Challenges in Heat Fin Design
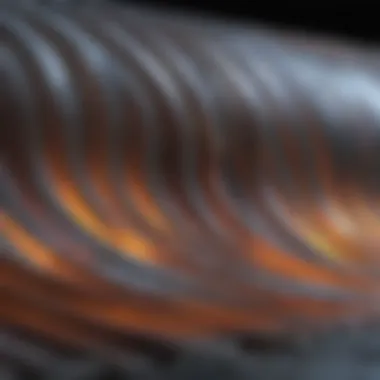
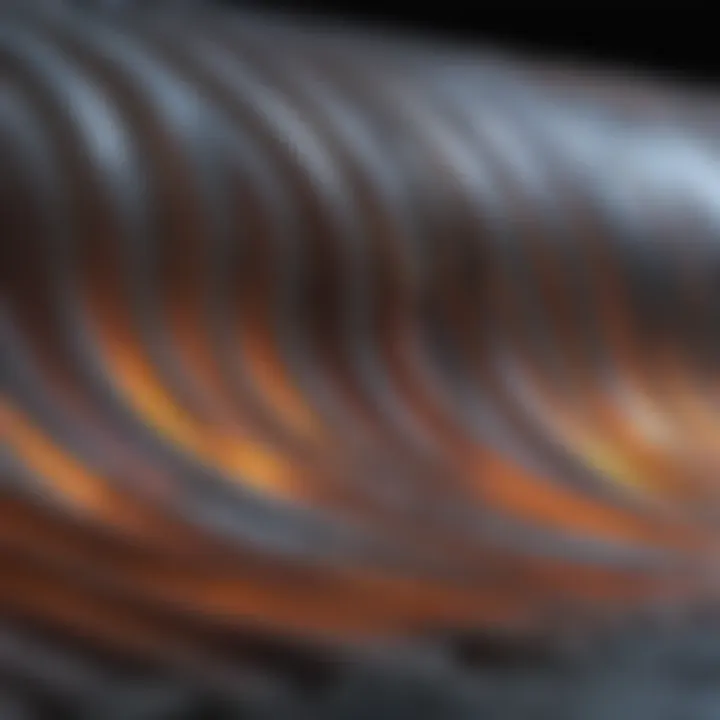
The design of heat fins does not come without its challenges. As crucial components in thermal management systems, heat fins must meet specific requirements to effectively dissipate heat while balancing cost and sustainability. Understanding these challenges is vital for engineers and researchers alike, as they drive innovation and influence future designs.
Cost Factors
Cost is a significant concern in the design and production of heat fins. High-quality materials, advanced manufacturing processes, and research-driven innovations can quickly escalate expenses. Engineers must find ways to create efficient heat fins without excessively increasing production costs.
Factors to consider include:
- Material Selection: Metals like aluminum and copper are excellent conductors of heat but can be expensive. Using less costly materials may reduce effectiveness.
- Manufacturing Techniques: Processes like extrusion and stamping can add to production costs but are essential for producing high-quality fins.
- Economies of Scale: Large-scale production can lower costs, but the initial investment in tools and technology can be sizeable.
Careful planning and budget assessments are essential to address these cost challenges while achieving the desired performance in heat dissipation.
Sustainability Considerations
Sustainability is increasingly important in the design of heat fins. As industries shift towards environmentally friendly practices, choosing materials and processes that minimize ecological impact plays a critical role.
Key sustainability factors include:
- Material Sourcing: Selecting recyclable or sustainably sourced metals reduces the carbon footprint associated with production.
- Energy Efficiency: Designing fins that maximize heat dissipation can lead to lower energy consumption in devices.
- Lifecycle Assessments: Evaluating the full lifecycle of heat fins, from production to disposal, helps identify opportunities for improvement.
By addressing these sustainability issues, engineers can contribute to a more eco-conscious manufacturing process without sacrificing performance.
"Sustainable heat fin design not only benefits the environment, but it also can lead to cost savings in the long run."
Case Studies of Heat Fin Implementations
Case studies provide invaluable insights into the practical applications of heat fins across various industries. They reveal how specific designs, materials, and configurations contribute to effective thermal management. Furthermore, these studies offer evidence of increased efficiency, reduced costs, and improved system reliability, making them essential for anyone involved in thermal management or engineering.
Analyzing successful implementations helps to understand the direct impact of heat fins in real-world scenarios. Evaluating these cases illustrates how theoretical principles apply in practice, allowing for knowledge transfer and refinement of designs.
Successful Industrial Applications
In industry, heat fins have proven critical in managing heat loads across diverse applications. For example, consider their role in the electronics sector. Devices like CPUs and GPUs generate significant heat during operation. Companies such as Intel and NVIDIA have integrated advanced heat fin designs into their cooling systems. This not only protects components from overheating but also enhances performance through sustained operational efficiency.
Another sector benefiting from effective heat fin design is the automotive industry. Vehicles must manage heat generated by engines and electrical systems. Manufacturers such as Ford utilize heat fins in radiators and cooling systems, leading to a more efficient engine operation and reduced fuel consumption.
The following points summarize benefits observed in successful industrial applications of heat fins:
- Enhanced Cooling Efficiency: Optimized designs allow for better heat dissipation.
- Cost Reduction: Improved heat management can lower energy costs.
- Reliability: Helps prevent failures in components due to overheating.
Innovative Research Projects
Research projects continue to explore new possibilities in heat fin technology. Academic institutions and innovation centers focus on improving materials and design methodologies. For instance, recent studies at MIT have looked into lightweight composite materials that offer superior thermal properties. This research aligns with the growing trend of lightweighting in the automotive and aerospace sectors.
Another interesting development comes from universities experimenting with microstructured fins. These designs maximize surface area and improve heat exchange efficiency significantly. Projects like these lay the groundwork for next-generation heat management systems, emphasizing the importance of continual innovation.
Key aspects of innovative research projects include:
- Material Development: Focus on composites and nanomaterials to improve performance.
- Design Strategies: Implementing microstructures and advanced geometries for better efficiency.
- Cross-Disciplinary Collaboration: Engaging engineers, material scientists, and environmental experts to address sustainability and performance simultaneously.
"The integration of advanced materials in heat fin design not only enhances performance but also aligns with global sustainability efforts."
In summary, case studies illustrate the tangible benefits of heat fins in industrial applications and ongoing research. By analyzing real-world implementations and innovative projects, one can gain insights that guide future developments and improvements in thermal management technologies.
Future Trends in Heat Fin Technology
The field of heat fins is evolving rapidly. In contemporary times, various factors drive advancements in their design and performance. Understanding these trends is essential for professionals and researchers in thermal management systems. They reveal how heat fins can become more efficient and effective, which aligns with the broader goals of energy conservation and system performance optimization.
Emerging Technologies
Innovations in materials science play a crucial role in the future of heat fins. For example, the development of advanced composite materials and enhanced phase change materials has shown significant promise. These materials can potentially improve thermal conductivity and overall efficiency.
- Graphene: This material possesses remarkable thermal properties. Its high conductivity enables better heat dissipation, which is desirable in electronics cooling applications.
- Metallic Alloys: New alloys formulated with high thermal conductivities are being designed to offer improved performance in extreme conditions.
- Nanotechnology: Nanostructured fins can enhance the surface area without a significant increase in size. This increases the heat transfer area which is essential in many applications.
It is noteworthy that integrating smart technologies into heat fins is also gaining traction. For instance, heat fins equipped with sensors can monitor real-time performance and adjust based on operational conditions, thereby optimizing heat management.
Predicted Market Growth
Market research indicates a significant growth trajectory for the heat fin technology sector. As industries increasingly prioritize efficiency and sustainability, heat fins are becoming a focal point of investment and innovation.
- Rapid Industrial Expansion: Sectors like automotive, electronics, and renewable energy are driving demand for better cooling solutions. The growing number of electric vehicles also increases the need for sophisticated heat management technologies.
- Regulatory Support: Governments are enforcing regulations that favor energy efficiency. This encourages industries to adopt advanced thermal management systems, including heat fins.
- Investment in R&D: Companies are channeling funding into research and development focused on heat fins. This investment is pivotal in developing next-generation materials and technologies.
In summary, the future trends in heat fin technology suggest not only an evolution in materials and design but also a substantial market evolution driven by contemporary needs and regulations. As these trends unfold, they will shape the landscape of thermal management solutions in diverse sectors.
Culmination
The conclusion serves as a critical component of the article, summarizing the essential elements discussed throughout the sections. A clear synthesis of these key points not only reinforces the reader's understanding but also emphasizes the overarching significance of heat fins in thermal management systems. Heat fins play a pivotal role in enhancing heat dissipation, which is vital across various applications from electronics to automotive engineering. This underscores their necessity in modern technology, highlighting how they facilitate efficient energy use and extend the lifespan of devices.
Summation of Key Points
- Heat Exchange Mechanisms: The article explored the fundamental principles that govern heat exchange processes, including thermal conductivity, convection, conduction, and radiative heat transfer.
- Material Choices: It delved into the materials commonly used in heat fin design, such as metals and composites, detailing their unique properties and suitability for various applications.
- Design Considerations: Various factors influencing heat fin design were discussed, particularly surface area optimization, geometric configurations, and overall heat transfer efficiency.
- Applications and Advancements: The diverse applications of heat fins in electronics cooling, automotive sectors, and industrial processes highlight their utility. Recent advancements in materials science and integration with nanotechnology were notably significant for future innovations.
- Challenges: The discussion on challenges, including cost factors and sustainability considerations, provides insight into future research domains.
Importance for Future Research
Future research is essential in maximizing the performance and effectiveness of heat fins. Key areas that warrant attention include:
- Material Innovation: Developing new materials with superior thermal properties will enhance heat transfer capabilities. Research into nanomaterials could yield significant improvements in performance.
- Enhanced Design: Advanced computational methods can be utilized to simulate and optimize heat fin designs, resulting in more efficient configurations.
- Sustainability Initiatives: Balancing cost and environmental impact is critical. New approaches that promote sustainable practices in heat fin manufacturing and application are needed.
- Integration in Emerging Technologies: As technology evolves, understanding how heat fins can be integrated into newer systems like renewable energy solutions will be crucial.
"The future of heat fins relies on innovation, material development, and a commitment to sustainable practices in design."
In summary, the exploration of heat fins in this article not only sheds light on their scientific and engineering importance but also frames a roadmap for ongoing and future investigations. The intricate systems of heat exchange they facilitate remain vital to enhancing operational efficiency in a world increasingly reliant on advanced technology.