Understanding Stainless Steel: Composition and Uses
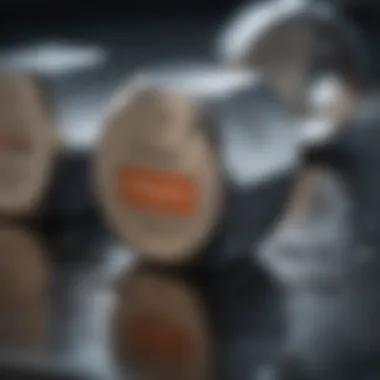
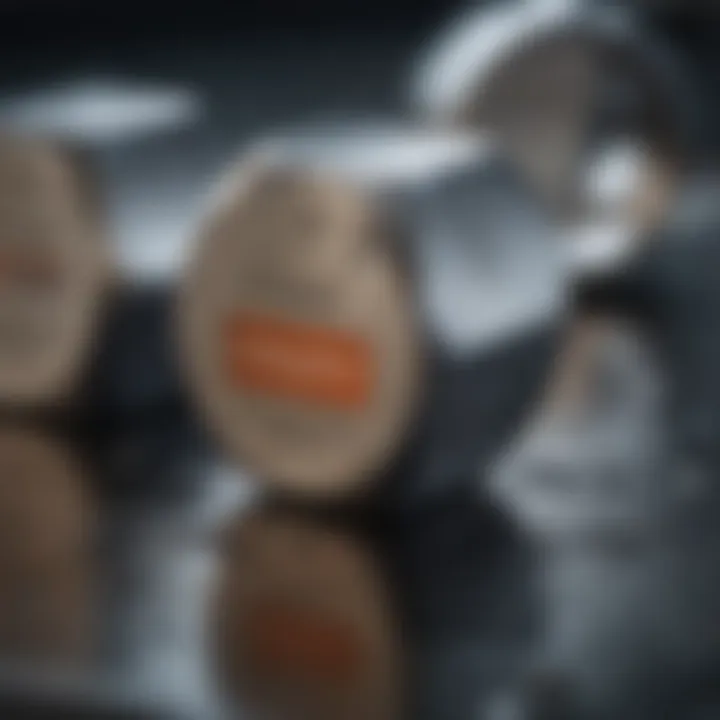
Intro
The world of materials is vast, yet few have captured the imagination and utility of engineers, builders, and everyday consumers quite like stainless steel. As an alloy, its resonance lies not just in its lustrous finish but in its remarkable properties, driven primarily by its composition which consists predominantly of iron, combined with chromium and often other elements like nickel and molybdenum. This unique concoction provides the material the distinct qualities that are revered across a multitude of industries.
In this article, we will embark on a detailed exploration of stainless steel, probing into its composition, intrinsic properties, and the myriad applications that underline its importance in modern manufacturing and construction. From its historical roots to its current role in promoting sustainability, our journey aims to illuminate why this material is so pivotal in today’s industrial landscape.
Without further ado, let's dive into the Research Highlights.
Prelims to Stainless Steel
Stainless steel stands as a pivotal material in contemporary society, an unsung hero in a multitude of applications. Understanding this alloy’s composition and properties not only unravels its significance but also shines a light on its versatile nature. From industrial settings to household kitchens, stainless steel's robustness against corrosion and exceptional strength make it a go-to choice for manufacturing and construction.
By exploring its various aspects, we can appreciate how vital stainless steel is in promoting durability and efficiency across different fields. Its adaptability is matched only by its promise of longevity, making it a worthy subject of discussion.
Defining Stainless Steel
Stainless steel is primarily an alloy of iron, but it is its key ingredient, chromium, that bestows its distinctive resistance to rust and corrosion. Typically, stainless steel contains a chromium content of at least 10.5%. This inclusion creates a thin, protective layer known as the passivation layer, which acts as a shield against oxygen and moisture.
Moreover, stainless steel comes in several types, each tailored for specific uses. This versatility is not merely a coincidence; it's a culmination of precise composition which might also include elements like nickel, molybdenum, and manganese, rounding out the characteristics that define the final product.
In the world of metallurgy, this alloy is often esteemed for its attractive appearance, mechanical toughness, and ability to withstand extreme temperature variations. Whether it’s for a sleek kitchen appliance or a robust engineering component, the defining traits of stainless steel make it worthy of the accolades it receives.
Historical Context
Tracing back its origins, stainless steel is a product of gradual evolution in metalworking. The saga begins in the early 20th century when metallurgists like Harry Brearley discovered that adding chromium to steel significantly enhanced its resistance to corrosion. Brearley's 1913 discovery came after he was tasked with creating an improved gun barrel, leading to the birth of what we now understand as stainless steel.
Since then, the development of stainless steel has witnessed several milestones. The innovation didn't stop at Brearley’s initial alloy. In subsequent decades, many variations emerged, as researchers experimented with additional elements to bolster specific properties. The boom of industries post-World War II saw stainless steel being utilized in diverse sectors such as shipbuilding, architecture, and later electronics, further solidifying its role in modern manufacturing.
The historical context offers us a lens through which we can appreciate not just what stainless steel is today, but also how it became a cornerstone in various industries. It serves as a reminder that every material has its story, one filled with trials, errors, and triumphant innovations.
Composition of Stainless Steel
Understanding the composition of stainless steel serves as the backbone to appreciating its diverse applications and unique properties. The world's reliance on stainless steel across multiple industries stems from its specific blend of elements that confer attributes such as corrosion resistance, strength, and aesthetic appeal. This section will take a closer look at the primary components that make up stainless steel and the role of minor additives. Each element plays its part in defining the alloy's characteristics, thus influencing decisions in manufacturing and overall functionality.
Primary Components
Iron
Iron is the primary component of stainless steel, making up the largest portion of its structure. Its significant role includes providing essential strength and structural integrity to the alloy. One key characteristic of iron is its abundance in the Earth's crust, which makes it a readily available material.
Iron's unique feature is its malleability, allowing for easier shaping and forming in various manufacturing processes. However, it does have disadvantages, chiefly its susceptibility to rust and corrosion. This characteristic alone necessitates the addition of chromium, ensuring that stainless steel can withstand various environmental conditions.
Chromium
Chromium sets itself apart as a pivotal player in the composition of stainless steel. It usually comprises around 10.5% to 30% of the alloy, contributing to its hallmark corrosion resistance. A vital aspect of chromium is its ability to form a thin layer of oxide on the surface, effectively protecting the metal beneath from degradation.
This oxidation layer gives stainless steel its name and is integral for applications where hygiene and cleanliness are paramount, such as in food processing. A downside of chromium, though, lies in its potential to make the alloy brittle at higher concentrations, which must be balanced during production.
Nickel
Nickel complements the work of chromium by enhancing the overall ductility and toughness of stainless steel. Typically making up about 8% to 20% of the composition, nickel helps maintain a stable structure across a wide range of temperatures. The key characteristic of nickel is its ability to prevent the formation of carbide, a compound that could weaken the material.
One unique feature of nickel is how it improves the alloy's resistance to pitting, a type of localized corrosion that can be especially damaging. However, the use of nickel isn’t without concerns; fluctuations in its price can impact manufacturing costs, making it essential for manufacturers to keep that in mind.
Minor Additives and Their Effects
While iron, chromium, and nickel dominate the composition of stainless steel, minor additives also play vital roles, influencing specific properties and enhancing performance. These elements may not be present in large quantities but can amplify attributes such as corrosion resistance, strength, and overall durability.
Molybdenum
Molybdenum is often added to stainless steel in small amounts, usually around 2% to 5%. Its primary role is to enhance corrosion resistance, particularly in chloride environments. A key characteristic of molybdenum is its ability to improve high-temperature strength—beneficial for applications in chemical processing industries.
The unique feature of molybdenum is that it helps prevent pitting and crevice corrosion, making it invaluable in marine settings. On the flip side, it can increase the cost of production, which manufacturers must weigh against the benefits in applications demanding high resistance to corrosion.
Titanium
Titanium is another minor additive that can significantly influence the properties of stainless steel. Typically added in small amounts, around 0.5% to 1.5%, it serves mainly to stabilize the structure at high temperatures. One essential characteristic of titanium is its reactive nature, which binds with carbon in the alloy, minimizing the risk of carbide precipitation.
A unique aspect of titanium is its ability to enhance weldability, making it a popular choice in industries requiring complex fabrication. However, the need for precise control of titanium levels is vital, as excessive amounts can lead to brittleness.
Copper
Copper is not the usual suspect but is gaining traction as an additive in specific stainless steel grades. Adding around 1% of copper can enhance the alloy's resistance to corrosion, especially against strong acids. The main feature of copper is its ability to improve malleability and lower thermal conductivity.


One of the advantages of copper is its role in giving stainless steel a unique aesthetic appeal, making it a favored choice for building facades and design applications. However, excessive copper can lead to an increase in susceptibility to tarnishing, something designers need to watch for closely.
Types of Stainless Steel Alloys
Understanding the different types of stainless steel alloys is crucial as each type exhibits distinct characteristics that make them uniquely suited for various applications. These alloys are generally categorized by their microstructure, which significantly influences their mechanical properties and corrosion resistance. As we dive into the specifics, it becomes clear how critical these variations are when matching the material to the requirements of a particular task.
Austenitic Stainless Steels
Austenitic stainless steels are the most widely used form of stainless steel, known for their high corrosion resistance and excellent formability. This type, often alloyed with nickel and chromium, has a face-centered cubic structure that gives it superior toughness, even down to cryogenic temperatures. A notable characteristic of austenitic steels is their non-magnetic nature, making them appropriate for applications where magnetic fields are a concern, such as in electronic equipment.
Benefits of Austenitic Stainless Steels:
- High resistance to corrosion and oxidation
- Excellent weldability and formability
- Good impact strength at low temperatures
A common alloy in this category is the 304 grade, used widely in kitchen appliances and food handling equipment due to its ability to resist acidic environments. It's interesting to note that the addition of molybdenum in the 316 grade enhances its marine grade quality, making it suitable for use in coastal areas.
Ferritic Stainless Steels
Ferritic stainless steels contain high chromium content but little to no nickel, making them more economical. These steels typically have a body-centered cubic structure, leading to magnetic properties. Ferritic steels are known for their good resistance to stress corrosion cracking but are generally lower in toughness compared to austenitic varieties.
Considerations for Ferritic Stainless Steels:
- Lower ductility compared to austenitic types
- Good weldability, yet can be more brittle
A well-known example is the 430 grade, commonly employed in automotive applications and kitchen utensils. While they may not offer the same level of corrosion resistance as the austenitic grades, their affordability and decent corrosion resistance make them a popular choice in less harsh environments.
Martensitic Stainless Steels
Martensitic stainless steels are characterized by their high carbon content, but they also contain chromium, offering moderate corrosion resistance. These steels can be heat-treated to achieve higher hardness and strength. However, this transformation comes at the cost of lower ductility. Their reversible transformation makes them suitable for a range of engineering applications.
Key Points about Martensitic Stainless Steels:
- High strength and hardness
- Moderate corrosion resistance
- Can be heat treated for better performance
The popular 410 grade is widely utilized for cutting tools and medical instruments where hardness is a necessity. This type finds its way into applications demanding good wear resistance and strength, despite not being the best choice in highly corrosive environments.
Duplex Stainless Steels
Duplex stainless steels combine the properties of both austenitic and ferritic steels, resulting in higher strength and better resistance to pitting and stress corrosion cracking compared to their single-phase counterparts. They possess a mixed microstructure and often contain nickel, chromium, and molybdenum, balancing cost with excellent corrosion resistance.
Advantages of Duplex Stainless Steels:
- High strength-to-weight ratio
- Superior resistance to localized corrosion
- Cost-effective when compared to austenitic steels
An example of this type is the 2205 grade, which is commonly found in applications such as oil and gas industries, where resilience against harsh chemicals is paramount. The use of duplex alloys is soaring, especially in sectors where performance under pressure is non-negotiable.
Each type of stainless steel offers unique properties tailored to specific applications, making understanding these alloys essential for selecting the right material for the job.
Manufacturing Processes
Manufacturing processes are critical to understanding the development and utility of stainless steel. The way stainless steel is melted, alloyed, formed, shaped, and finished dictates its properties and, consequently, its applications. This section dives into various methods that underpin stainless steel production, emphasizing how each step plays a role in ensuring the material meets the exacting standards necessary for its diverse uses. By dissecting these processes, one can appreciate the blend of artistry and science that goes into making stainless steel an industrial staple.
Melting and Alloying
Melting and alloying form the foundation of stainless steel production. These initial steps are not merely about heating metal to its liquid state; they are about achieving a precise balance of elements that defines the alloy's final properties. The right temperatures must be maintained, and each element carefully introduced to ensure uniformity. The process often involves electric arc furnaces or induction furnaces, where high temperatures allow the base iron to dissolve the alloying agents like chromium and nickel.
It's this careful control and integration of materials that foster the corrosion resistance and strength that stainless steel is known for.
Forming and Shaping
Casting
Casting is a fundamental method in shaping stainless steel. In this process, molten steel is poured into molds, forming various shapes like ingots or custom pieces tailored for specific applications. This technique allows for intricate designs and dimensions to be achieved, giving engineers and designers the flexibility they need. One remarkable aspect of casting is its ability to reproduce complex geometries accurately, unlike some other shaping methods like forging. However, the cooling rate can impact the final properties, occasionally leading to stresses within the material if not controlled properly.
Rolling
Rolling is another essential forming technique that takes advantage of the material's malleability when hot or cold. In this process, slabs of stainless steel are passed between rollers to reduce their thickness and shape them into sheets, plates, or other configurations. The uniqueness of rolling lies in its ability to produce large quantities of uniform material efficiently. Notably, hot rolling often improves ductility while cold rolling can enhance tensile strength. However, cold rolling can make the steel harder, requiring careful handling during further processing.
Welding
Welding is where the magic of joining happens. It’s a vital aspect of stainless steel fabrication, allowing separate pieces to be fused together without compromising their integrity. Various welding techniques, such as TIG (Tungsten Inert Gas) or MIG (Metal Inert Gas), cater to different thicknesses and types of stainless steel. What sets welding apart is its versatility; it allows for the repair and customization of structures that are already in place. The key characteristic here is thermal influence—the heat from the welding process can alter the microstructure of the steel, sometimes leading to a need for post-weld treatments to alleviate stresses, thus preserving the corrosion-resistant qualities of the steel.
Finishing Techniques
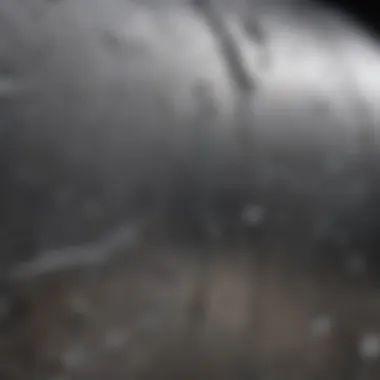
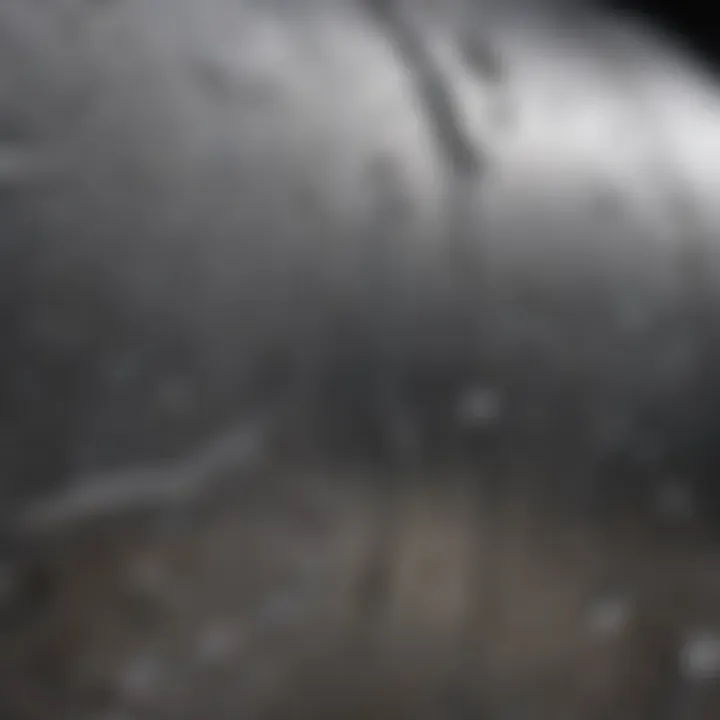
Pickling
Pickling is a finishing technique that removes impurities and oxides from stainless steel, usually through an acid bath. It plays a vital role in ensuring the aesthetic and functional integrity of the steel by providing a clean surface free from contamination. The characteristic feature of pickling is its effectiveness in restoring the corrosion resistance of stainless steel. However, the use of strong acids requires careful handling and disposal regulations, making it essential for manufacturers to adhere strictly to safety protocols.
Passivation
Passivation is another finishing step that enhances stainless steel's durability against corrosion. This process typically follows pickling and involves treating the metal with passivating solutions to promote the formation of a protective oxide layer. The advantage of passivation lies in its ability to further improve corrosion resistance without significantly altering the appearance of the steel. One unique feature is that while both pickling and passivation are crucial, they serve different yet complementary purposes in the surface treatment of stainless steel.
In summation, the manufacturing processes of stainless steel encapsulate a fascinating interplay of techniques, from the initial melting and alloying to the intricate details of forming and finishing. Each phase contributes uniquely to the final product, ensuring that stainless steel meets rigorous demands, whether it’s in construction, rank infrastructure, or household items.
Understanding these steps enriches our appreciation of stainless steel as a pinnacle of modern material science.
Properties of Stainless Steel
The significance of stainless steel lies not only in its composition but also in its distinctive properties. These properties greatly influence its applicability across various fields. Understanding these characteristics enables industries to select the right type of stainless steel for their specific needs. Below are the critical properties that make stainless steel a preferable choice.
Corrosion Resistance
One of the hallmark characteristics of stainless steel is its impressive resistance to corrosion. This property stems largely from the presence of chromium, which forms a passive layer of chromium oxide on the surface. This layer acts as a protective shield against moisture and corrosive environments. As a result, stainless steel is favored in applications where exposure to harsh chemicals or wet conditions is common, such as in chemical processing plants and offshore structures. The durability provided by this resistance contributes significantly to the longevity of the material, reducing maintenance costs over time.
"Stainless steel's resistance to corrosion is essential for protecting investments made in critical infrastructure and machinery."
Mechanical Strength
Stainless steel offers considerable mechanical strength, making it suitable for applications that require robust materials. Depending on its composition and processing, it can possess high tensile strength and yield strength, translating into superior performance under stress and load. For example, austenitic stainless steels, known for their ductility, can stretch without breaking, whereas martensitic varieties exhibit hardening properties ideal for cutting tools. This balance of strength and flexibility is why stainless steel is used in the automotive and construction sectors.
Thermal Properties
Thermal properties play a crucial role in how stainless steel behaves under various temperature conditions. This section divides into two subcategories: conductivity and expansion.
Conductivity
Stainless steel generally has lower thermal conductivity compared to other metals, such as copper or aluminum. This means it doesn't transfer heat as efficiently. While this can be seen as a disadvantage in applications requiring high heat transfer, it is beneficial in environments where temperature control is vital, providing safety by preventing overheating. The unique feature of low conductivity allows stainless steel to maintain its shape and integrity even when subjected to extreme thermal cycles, making it a desired option for certain kitchen appliances and industrial equipment.
Expansion
Thermal expansion refers to how materials change size or shape in response to temperature fluctuations. Stainless steel expands when heated and contracts when cooled, yet it does so at a predictable rate. This characteristic is essential in designing machinery and structures, ensuring proper fit and function during temperature changes. While stainless steel’s expansion properties are generally manageable, they require careful consideration in applications where precision is required, such as in aerospace components or high-pressure systems. Understanding this property helps engineers mitigate potential issues related to thermal stress, thereby enhancing the reliability of their designs.
Applications of Stainless Steel
Stainless steel is not just another alloy; it has become a cornerstone in various industries and daily life. The versatility and durability of stainless steel make it the material of choice for a wide range of applications. Understanding its applications allows for a deeper appreciation of its utility and the benefits it brings to different sectors. Given its properties, such as resistance to corrosion and ease of maintenance, stainless steel stands out as an ideal candidate for both industrial and domestic uses. Let's explore some of the most significant applications across different fields.
Industrial Uses
Chemical Processing
In chemical processing, stainless steel is invaluable due to its ability to withstand harsh environments. The industry regularly deals with aggressive chemicals that can corrode other materials. Because of its resistance to corrosion, stainless steel is often used in reactors, heat exchangers, and storage tanks. One key characteristic of stainless steel in this application is its ability to maintain structural integrity in both high and low pH settings. Thus, it is a favored choice.
One unique feature lies in the fact that the high chromium content in certain stainless steels provides a protective layer that prevents rust. This is not only beneficial for longevity but also for safety, as the material does not degrade or pollute the substances it contains. However, the cost can be a consideration, as stainless steel generally runs higher than other metals, but the trade-off can be worth it in maintaining chemical purity and safety.
Aerospace
The aerospace sector hinges on material performance where weight and strength are crucial. Stainless steel shines in this regard, particularly in components exposed to extreme temperatures and pressures. Aerospace applications typically require materials that have high tensile strength, and certain alloy variants excel in this.
In addition, the unique feature of aerospace-grade stainless steel, which often includes nickel and molybdenum, allows for excellent performance under stress conditions. This makes it a popular choice due to its reliability. On the downside, while the installation and maintenance require specialized knowledge, the durability of stainless steel reduces the frequency of replacements, making it an appealing option despite the upfront costs.
Construction
In construction, the use of stainless steel has surged due to its aesthetic appeal and structural benefits. It is often chosen for architectural elements like railings, facades, and roofing materials. The key characteristic here is resilience; stainless steel performs admirably against weathering and does not require frequent repainting or maintenance, which translates to cost savings over time.
One unique aspect of stainless steel is its ability to be molded into various forms, allowing for innovative and artistic designs in modern architecture. While it can be more expensive than carbon steel, its lifecycle benefits and visual appeal make it a popular choice among architects and builders.
Household Applications
Kitchenware
Stainless steel kitchenware is a staple in homes around the globe. The principal reason is its hygienic properties; stainless steel does not harbor bacteria, making it ideal for food preparation. Additionally, its durability allows it to withstand the rigorous demands of daily cooking.
A special feature is its non-reactivity; it doesn’t impart flavors or odors to food. This can be particularly advantageous when working with acidic ingredients, such as tomatoes or vinegar, which can react negatively with other metals. Yet, one downside is that stainless steel can lose luster over time if not cared for properly, but this is easily remedied with proper cleaning techniques.
Appliances
Stainless steel appliances are increasingly favored in modern kitchens. The sleek, contemporary look not only elevates the kitchen aesthetic but also matches well with various décor styles. The key characteristic of appliances made from stainless steel is their robustness; they are resistant to scratches and fingerprints, making them easy to maintain.
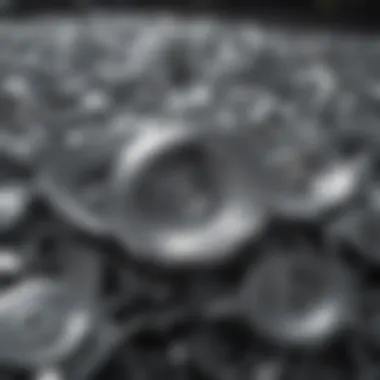
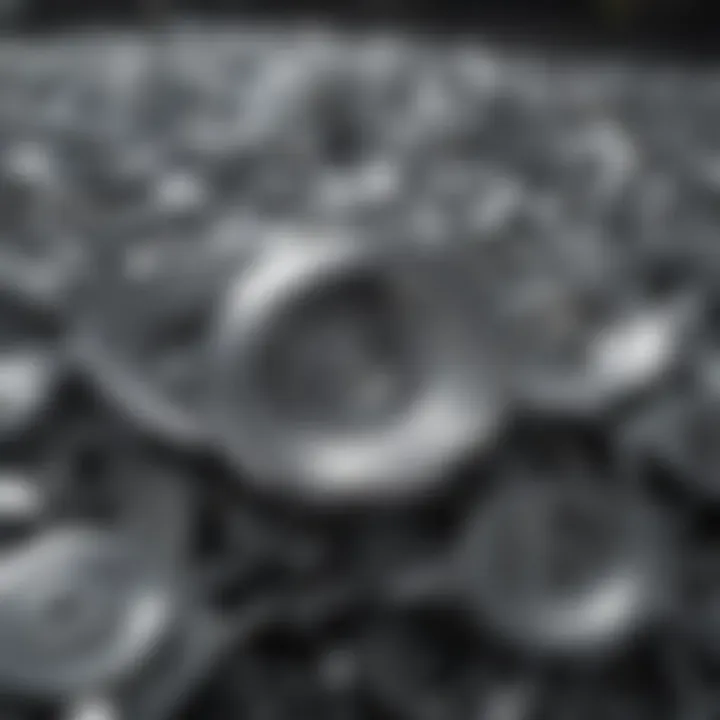
One unique benefit is their thermal efficiency; stainless steel evenly distributes heat. This feature enhances cooking performance and energy efficiency. However, the initial purchase cost may be higher than that of other materials, and they can be prone to denting if not handled with care, which is worth considering.
Medical Applications
Surgical Instruments
Surgical instruments are often made from stainless steel due to the stringent requirements for hygiene and durability in the medical field. The corrosion resistance and bio-compatibility of stainless steel mean that these instruments can be sterilized effectively without losing their quality. A notable feature is that stainless steel can maintain a sharp edge over time, critical for precision in surgical procedures.
While synthesis of stainless steel instruments can be expensive, the reliability that comes with their use far outweighs initial costs. They are a popular choice due to their longevity and ability to withstand repeated sterilization processes.
Implants
In terms of medical implants, stainless steel’s biocompatibility is key. It is often used for temporary implants or in certain bone fixation devices. The resilience against body fluids combined with strength ensures effective performance over time.
A unique characteristic of stainless steel in this application is its adaptability; it can be engineered for various degrees of flexibility or rigidity depending on the need. On the flip side, potential allergic reactions to certain metal alloys can occur, making careful selection and testing essential.
Overall, the applications of stainless steel across different sectors highlight its versatility and undeniable value. Its unique properties not only enhance performance but also offer solutions that other materials cannot provide.
Sustainability of Stainless Steel
In the face of global environmental challenges, the sustainability of materials we use has become crucial. Stainless steel stands out as a champion in this arena. Its unique properties not only make it a preferred choice for various industries but also contribute significantly to sustainable practices. As we navigate through pressing issues like waste management and energy usage, understanding the sustainability attributes of stainless steel is imperative. It is essential to evaluate how this material aligns with eco-friendly goals and the role it plays in a circular economy.
Recyclability
Stainless steel is not just a single-use material; it's remarkably recyclable, making it an environmental favorite. The recycling process of stainless steel is energy-efficient and requires less energy compared to producing new stainless steel from raw materials. This is noteworthy because:
- High Recycling Rates: Over 80% of stainless steel is recycled globally, which speaks volumes about its value as a resource.
- Virtually 100% Recoverable: Unlike many materials, stainless steel can be recycled indefinitely without loss of quality. This characteristic is particularly beneficial for heavy industrial applications.
- Environmental Savings: Recycling stainless steel saves significant amounts of raw materials and reduces the energy required to produce new steel, which helps in cutting down the greenhouse gas emissions.
The ability to recycle stainless steel turns waste into valuable resource, helping to conserve earth’s minerals. This monumental aspect of recyclability helps industries reduce their carbon footprint, and it also plays a vital role in sustainable urban development.
Environmental Impact
When talking about the environmental impact of stainless steel, several factors come into play. It starts with the raw materials, where extraction can have consequences, yet stainless steel's lifecycle can help mitigate many of these effects through longevity and sustainability. Here are the key aspects:
- Durability and Longevity: Stainless steel is tough. It resists corrosion and wear, which implies that products made from it last longer and need to be replaced less frequently. That's a win-win for sustainability.
- Low Maintenance: The maintenance of stainless steel structures or pieces is fairly low, which further prevents additional resource expenditure over time.
- Sustainable Production Techniques: Efforts are underway to make the production of stainless steel greener by reducing energy consumption and employing renewable energy sources in manufacturing.
"In every stage of its lifecycle, stainless steel's durability and recyclability contribute to its sustainability while offering a wide array of uses across various sectors."
Through careful consideration of its recyclability and overall environmental effect, we see that stainless steel embodies a responsible choice. Not only does it cater to the functional needs of modern society, it also aligns with the ethical considerations accompanying sustainability. As the push for a more sustainable future intensifies, stainless steel’s role is likely to grow even more pivotal.
Future of Stainless Steel
The future of stainless steel is shaped by several dynamic factors emphasizing innovation, sustainability, and technological advancements. With society increasingly valuing durable and environmentally friendly materials, stainless steel is likely to remain at the forefront of material science and engineering. The importance of this topic lies in its multifaceted implications—ranging from advancements in its properties to its role in various industries. As global economic activities shift towards more sustainable practices, understanding the trends and innovations in stainless steel becomes crucial for a variety of stakeholders, including students, researchers, educators, and professionals.
Innovation and Research
Innovation in stainless steel focuses on improving its characteristics and expanding its applications. Researchers are particularly dedicated to developing new alloys that enhance specific properties like strength, corrosion resistance, and thermal stability. For instance, alloys that integrate copper are being explored to enhance antimicrobial properties, making them suitable for healthcare settings. This line of research not only aims to improve performance but also works on reducing costs and environmental impacts. Moreover, companies are investing in smart manufacturing technologies, such as 3D printing. This allows for the creation of complex stainless steel components that were previously difficult or even impossible to produce, thus revolutionizing production methods.
In the field, academic institutions and industry leaders often collaborate to investigate the potential of stainless steel in renewable energy applications. For example, the use of stainless steel in solar energy technologies is gaining traction. The research focuses on how specific compositions can improve efficiency and durability in harsh environmental conditions. By prioritizing innovative solutions, we can expect stainless steel to play a pivotal role in sustainable energy practices.
Trends in Manufacturing
The manufacturing landscape for stainless steel is shifting its focus towards both efficiency and sustainability. Automation and artificial intelligence are becoming more prevalent in production lines to enhance precision and reduce waste. These advancements are crucial in keeping pace with the rising demand for high-quality stainless steel products, especially in sectors like aerospace and medical devices.
Furthermore, there is a notable trend towards adopting green manufacturing processes. These practices involve using less energy and reducing emissions during production. For example, electric arc furnaces, which are more energy-efficient than traditional blast furnaces, are becoming popular in stainless steel production. This shift not only helps manufacturers cut costs but also aligns with the global push towards sustainability.
"Innovations in manufacturing not only enhance product quality but also significantly reduce the environmental footprint of stainless steel production."
Additionally, the recycling of stainless steel is becoming a prominent practice. With a high recyclability rate, around 90%, businesses are ramping up efforts to reclaim and repurpose scrap metal. This aspect offers significant benefits, like conserving resources and minimizing pollution, making stainless steel an even more appealing choice for various applications.
As we look ahead, it’s evident that the future of stainless steel lies not only in enhancing its qualities but also in evolving how it is produced and used across many sectors. Keeping an eye on these trends will be essential for anyone involved in the field.
Culmination
In wrapping up this exploration into stainless steel, it's vital to consider the multifaceted nature of this alloy which has evolved significantly over time. From its foundational composition to its wide-ranging applications, stainless steel's role in both industry and daily life cannot be overstated. It serves not just as a material but as a benchmark for durability and versatility.
Summary of Key Points
The key takeaways regarding stainless steel are paramount for anyone looking to fully grasp its significance.
- Composition: Stainless steel primarily consists of iron, chromium, and varying amounts of nickel, molybdenum, and other elements. This unique blend provides attributes that are essential for its various applications.
- Types of Alloys: The article outlined different types of stainless steel: austenitic, ferritic, martensitic, and duplex steels. Each has distinct properties tailored for specific uses.
- Properties: Its resistance to corrosion, mechanical strength, and thermal properties position stainless steel as a preferential material for many sectors including medical, aerospace, and construction.
- Manufacturing Processes: Methods like casting, rolling, and welding showcase both traditional and modern techniques that shape the final product, impacting its overall performance and quality.
- Sustainability: The recyclable nature of stainless steel links it to environmental considerations, addressing waste and promoting a circular economy.
Final Thoughts on Stainless Steel
In summary, stainless steel stands as a hallmark of engineering prowess, blending utility with aesthetic appeal. As new innovations emerge, its applications expand, and its significance within sustainable practices grows, it's clear that stainless steel is not just a material of the present but also a critical component for future advancements.
Understanding its composition and applications equips students, researchers, educators, and professionals alike with the necessary knowledge to leverage stainless steel for innovative solutions in diverse fields.
"Stainless steel isn't just about strength; it's about enhancing life’s potential through design and reuse."
In this light, the continuous research and development in stainless steel technologies and processes will undoubtedly pave the way for breakthroughs, ensuring that this remarkable alloy remains at the forefront of material science.